Understanding the Physical Properties of Foundry Sand
Foundry sand plays a crucial role in the casting process, which involves shaping molten metal into desired forms using molds. The effectiveness of this process largely hinges on the physical properties of the sand used in foundries. By examining these properties, we can gain insight into how they affect the quality of castings and the efficiency of the foundry operations.
1. Composition and Granulation
Foundry sand is typically composed of high-purity silica (SiO₂), which provides essential properties such as high melting point and resistance to thermal shock. The sand's granulation, or particle size distribution, is critical; it influences the sand's flowability, packing density, and surface finish of the casting. Fine sands are generally better for creating detailed molds, while coarser sands offer better flow and are typically used in larger castings.
The standard grading of foundry sand is often determined by sieve analysis, where the sand is passed through various mesh sizes to evaluate the particle size distribution. This analysis helps in optimizing the mix of fine and coarse grains to achieve the desired mold properties.
2. Moisture Content
The moisture content of foundry sand is another vital physical property that can affect the mold's strength and durability. A certain level of moisture is necessary for the chemical bonding process, especially when using clay as a binder in sand casting. However, excessive moisture can lead to defects such as mold collapse or sand expansion, which may result in imperfections in the final casting.
Maintaining the right balance of moisture is essential for achieving optimal mold tenacity and ensuring smooth casting operations
. Foundries often monitor moisture levels closely throughout the sand preparation process.physical properties of foundry sand
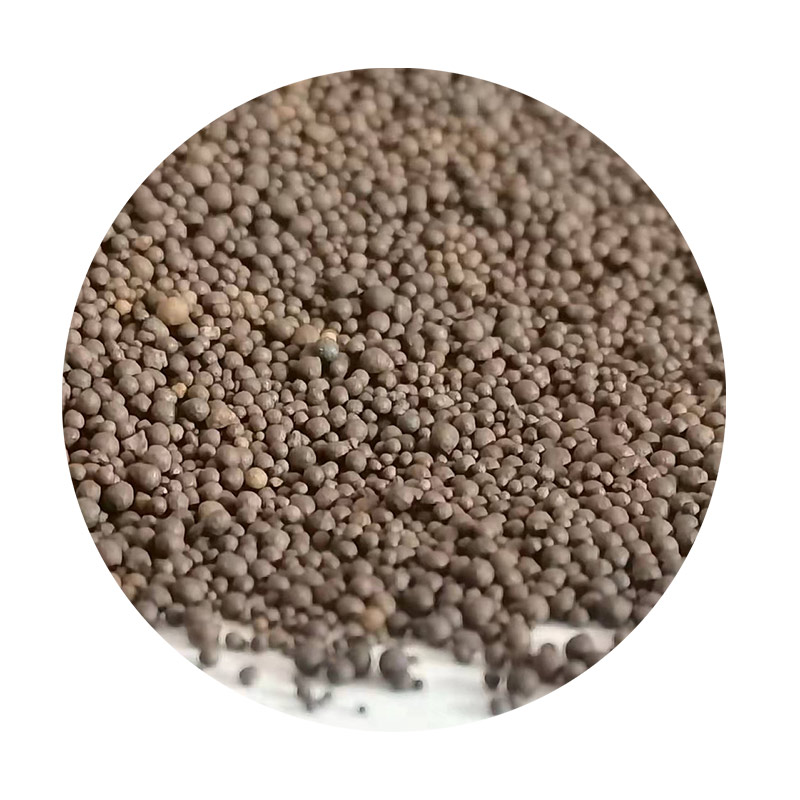
3. Permeability
Permeability refers to the ability of the sand mold to allow gases to escape during the casting process. Chemical reactions and metal vaporization can produce gases that need to be vented; otherwise, they can cause defects in the casting, such as blowholes and sand inclusions. The permeability of foundry sand is largely dependent on particle size, distribution, and the nature of the binder used.
A well-structured foundry sand should have enough permeability to allow gases to escape while maintaining sufficient strength to withstand the pouring of molten metal. Testing for permeability is typically done using a standardized apparatus that measures the sand's airflow resistance.
4. Green Strength and Dry Strength
Green strength refers to the compressive strength of the mold before it undergoes drying or baking. It is crucial for maintaining the mold's integrity against the weight of the molten metal. Higher green strength enables the mold to retain its shape during the pouring process. Dry strength, on the other hand, pertains to the mold's strength after it has been heated and dried. Both properties are essential for ensuring quality in the casting process.
These strength measurements can be optimized through the selection of appropriate sand grades and binder systems, taking into consideration the specific requirements of the casting application.
Conclusion
The physical properties of foundry sand significantly influence the performance of the casting process. Understanding the composition, granulation, moisture content, permeability, and strength characteristics of the sand used in foundries allows for better control over the molding process and improved quality of castings. As foundry practices continue to evolve, the role of advanced materials and better testing methods will further enhance the effectiveness of foundry sand, contributing to more efficient and reliable production processes in the metalworking industry.
Post time:ធ្នូ . 13, 2024 13:49
Next:sand ceramic