Physical Properties of Foundry Sand
Foundry sand plays a crucial role in the metal casting industry, serving as a primary molding material. Its physical properties directly affect the casting process and the quality of the final product. Understanding these properties is essential for foundry engineers and operators to optimize production and ensure that the cast components meet stringent quality standards.
Composition and Grain Size
The primary ingredient of foundry sand is silica (SiO₂), though other materials, such as clay or coal dust, may be added to enhance certain properties. Silica sand is preferred due to its high melting point, excellent thermal stability, and resistance to chemical reactions during casting. The grain size of foundry sand influences mold permeability, strength, and surface finish. Generally, a well-graded blend of coarse and fine grains can promote optimal packing density while ensuring adequate airflow through the mold. Fine grains contribute to a smoother surface finish, while coarser grains enhance strength.
Permeability
Permeability refers to the ability of sand to allow gases to escape during the casting process. It is a vital property that helps prevent defects, such as gas porosity in the castings. Foundry sand should possess sufficient permeability to accommodate the gases generated from the molten metal without causing blisters or other surface imperfections. The ideal permeability level depends on the type of casting and the metal alloy being used; thus, foundry operators often conduct standardized tests, such as the AFS permeability test, to measure this property accurately.
Strength
physical properties of foundry sand
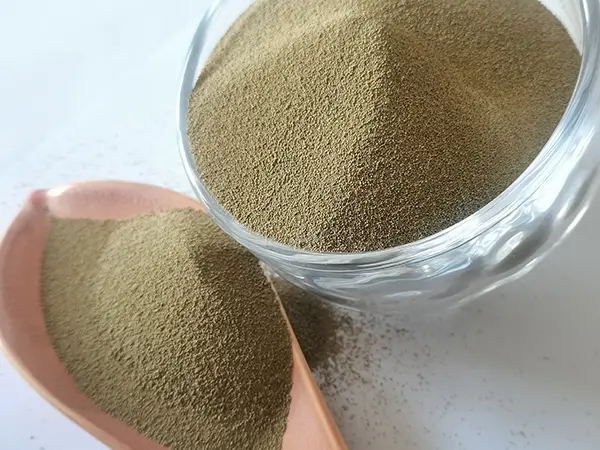
The strength of foundry sand is another essential physical property, impacting the sand mold's ability to retain its shape under the weight of molten metal. The strength is typically defined in terms of compressive strength, shear strength, and tensile strength. To achieve the necessary strength, bonding agents such as clay are often added to the sand mixture. The moisture content also plays a significant role; adequate moisture can enhance the cohesiveness and strength of the sand, while overly wet or dry conditions can lead to mold failure. Therefore, maintaining the right balance of moisture and bonding agents is crucial for producing stable molds.
Thermal Conductivity
Thermal conductivity is a property that affects how heat is transferred from the molten metal to the sand mold. High thermal conductivity can lead to faster cooling rates, which can affect the solidification process and the properties of the casting. Conversely, lower thermal conductivity can help control cooling rates, potentially leading to improved mechanical properties in the final casting. Therefore, the choice of foundry sand and its specific thermal characteristics can significantly impact casting quality.
Reusability and Environmental Impact
Another critical physical property of foundry sand is its reusability. Good foundry sand should be recyclable, allowing it to be reused multiple times without significant degradation of its physical properties. However, the accumulation of impurities and degraded particles over time can affect the strength and permeability of the sand. Thus, foundries often have processes in place for reclamation and reconditioning to maintain the quality of the sand while minimizing environmental impact.
In summary, the physical properties of foundry sand—such as grain size, permeability, strength, thermal conductivity, and reusability—are fundamental to the casting process. Leveraging these properties effectively can lead to higher quality castings, improved operational efficiency, and reduced waste, ultimately contributing to a more sustainable foundry industry. As technology advances and environmental regulations become stricter, understanding and innovating in foundry sand properties will continue to be essential for the industry’s future.
Post time:វិច្ឆិកា . 30, 2024 09:18
Next:Resin Coated Frac Sand for Enhanced Oil and Gas Extraction Efficiency