Parting Sand in Foundry Understanding Its Role and Importance
The foundry industry has long been an essential pillar of manufacturing, providing key components and products that are foundational to numerous other sectors, including automotive, aerospace, and construction. One of the critical materials utilized in the casting process within foundries is sand, specifically parting sand. This article delves into the importance, characteristics, and applications of parting sand in foundries, offering insights into its role in the casting process and how it contributes to quality manufacturing.
Parting sand is typically a fine-grained sand used in the molding process of metal casting. Its primary purpose is to facilitate the separation of two halves of a mold, allowing the foundry workers to remove the casting from the mold cavity without damaging either the mold or the finished product. The use of parting sand is crucial in ensuring that the mold halves can be parted cleanly, thereby achieving a high-quality casting that meets the required specifications.
Parting Sand in Foundry Understanding Its Role and Importance
Another important aspect of parting sand is its compatibility with the other materials used in the mold making process. Foundries typically use various binders and additives to enhance the properties of the sand, creating a mold that can withstand the high temperatures of molten metal. Parting sand must not react adversely with these materials, as any chemical interaction could compromise the integrity of the mold and negatively impact the quality of the cast metal.
parting sand in foundry
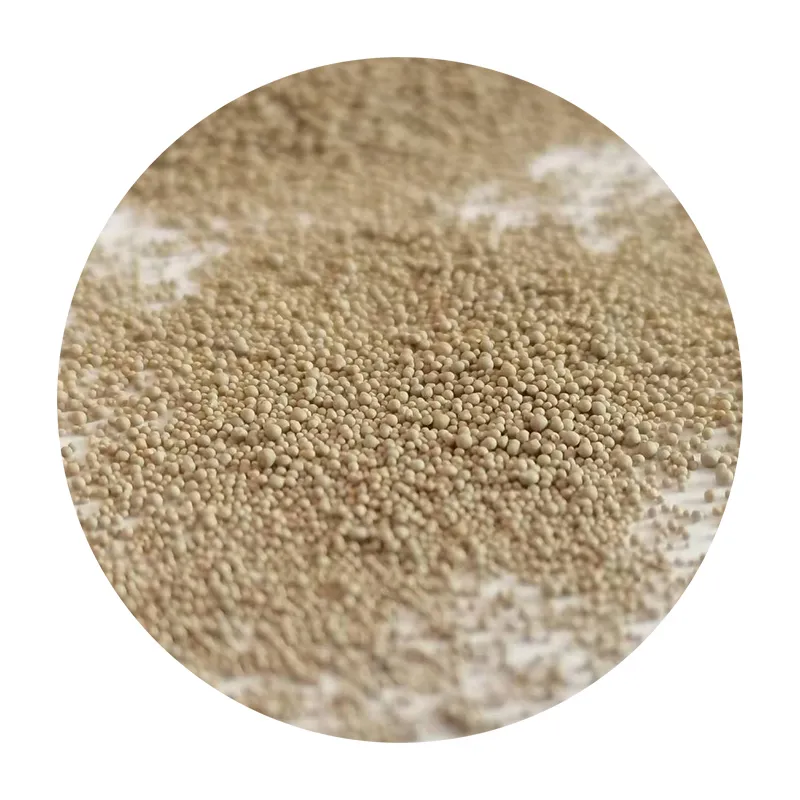
In practice, parting sand is often applied to the surface of a mold before the two halves are joined together. This application acts as a lubricant, facilitating the separation process after the metal is poured and has solidified. The use of parting sand is especially important in complex mold designs, where intricate shapes and features can make mold separation particularly challenging. By reducing friction, parting sand allows for a smoother, easier release of the casting, preventing the risk of damage to both the mold and the finished product.
Moreover, parting sand can also play a role in the aesthetic qualities of the final cast product. By providing a smooth release surface, it helps to eliminate surface imperfections that could otherwise arise from sticking or tearing during the removal process. This smooth finish is particularly vital for components that require a high level of aesthetic appeal or precise dimensions, such as those found in the aerospace and automotive industries.
The sourcing and selection of parting sand are also critical considerations in the foundry process. Foundries often choose silica sand due to its excellent thermal stability and desirable mechanical properties. However, it is essential for foundry operators to regularly assess the quality and performance of their parting sand. Factors such as environmental conditions, casting volume, and material specifications can all impact the effectiveness of the sand, necessitating continuous monitoring and adjustments as needed.
In conclusion, parting sand is an indispensable material in the foundry industry, playing a pivotal role in mold separation and ultimately influencing the quality of the finished cast products. Its unique properties, including grain size, compatibility with other materials, and contribution to surface finish, underline its significance in the casting process. By understanding and utilizing parting sand effectively, foundries can enhance their manufacturing capabilities and produce components that meet the quality and performance standards required in today’s demanding market. As the industry continues to advance, the importance of optimizing every element of the foundry process, including the careful selection and application of parting sand, will remain paramount in achieving excellence in casting.
Post time:តុលា . 12, 2024 16:54
Next:Fundición de arena de bajo volumen para producciones eficientes y personalizadas