Understanding Metal Casting Sand Types, Properties, and Applications
Metal casting is a crucial manufacturing process that involves pouring molten metal into a mold to create a desired shape. One of the key components in this process is casting sand. The choice of sand used plays a vital role in determining the quality and efficiency of the castings produced. This article explores the various types of casting sand, their properties, and applications in metal casting.
Types of Casting Sand
There are several types of sand used in the metal casting process. The most common types include
1. Green Sand This is the most widely used casting sand. It is a mixture of silica sand, clay, and moisture. The moisture present in green sand helps in binding the particles together, providing the necessary strength to hold the mold shape. Green sand is favored for its reusability and cost-effectiveness.
2. Dry Sand Unlike green sand, dry sand is baked in ovens to remove moisture, making it stronger and more durable. It is formed by mixing sand with a binding agent such as resin. Dry sand molds have high dimensional stability and are typically used for high-precision components.
3. Sodium Silicate Sand This type of sand uses sodium silicate as a binder and is known for its environmentally friendly properties. The sand is hardened by the reaction with carbon dioxide. Sodium silicate sand molds are less common but are utilized in applications where specific environmental conditions are required.
4. Furan Sand This sand is made using furan resin as a binder. It possesses excellent strength and resistance to thermal shock. Furan sand is particularly advantageous for casting complex shapes and is often used in industries requiring intricate designs.
Properties of Casting Sand
metal casting sand
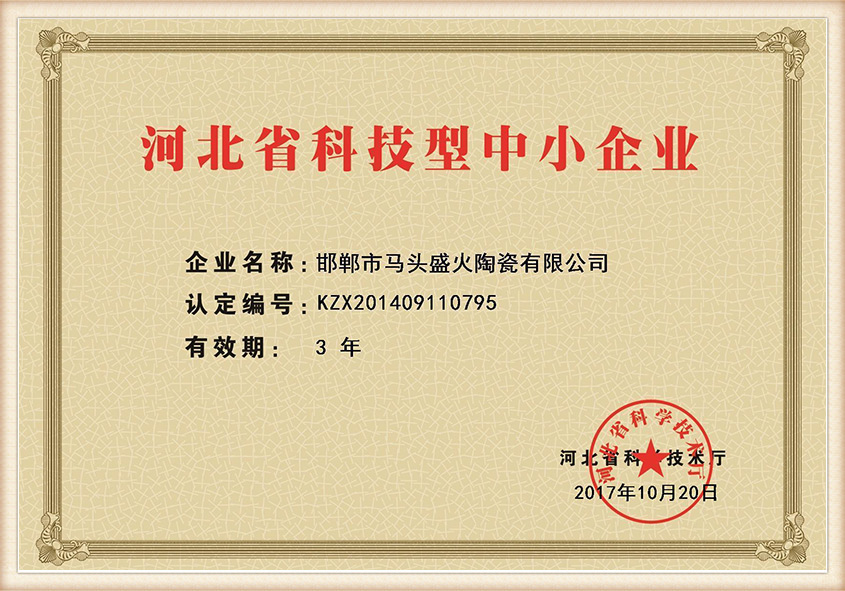
The effectiveness of casting sand can be evaluated based on several key properties
- Grain Size and Distribution The size of the sand grains influences the mold's ability to withstand high temperatures and pressure. A uniform grain size promotes better packing and results in smoother surface finishes.
- Moisture Content The amount of moisture in the sand plays a crucial role in mold strength. While some moisture is necessary for the binding properties of green sand, excessive moisture can lead to defects in the casting process.
- Permeability This property refers to the ability of sand to allow gases to escape during the casting, preventing defects such as blowholes. High permeability is essential for ensuring the quality of the final casting.
- Reusability The longevity of casting sand is a significant factor in its overall cost-effectiveness. Green sand can be reclaimed and reused multiple times, making it a popular choice.
Applications of Casting Sand
Casting sand is used across various industries, including automotive, aerospace, machinery, and more. The choice of sand type often depends on the complexity of the casting, the material being cast, and the desired surface finish. For example, green sand is extensively used for producing intricate automotive parts, while dry sand may be preferred for high-precision aerospace components.
In conclusion, metal casting sand is an integral component of the metal casting process. Understanding the different types of casting sands, their properties, and applications is crucial for producing high-quality castings. As technology advances, the development of new types of casting sands continues to enhance the capabilities of the metal casting industry, ensuring productivity and innovation.
Post time:កញ្ញា . 25, 2024 19:17
Next:what is sand casting