Lost Foam Casting Coating Enhancing Precision and Quality
Lost foam casting (LFC) is a revolutionary process in metal casting that allows for the production of complex shapes with high dimensional accuracy, minimal material waste, and excellent surface finish. A critical component of this process is the coating applied to the foam patterns before they are surrounded by the casting material. This coating enhances the overall quality of the final product and plays a significant role in the efficiency of the casting process.
The Basics of Lost Foam Casting
In lost foam casting, a foam pattern is created to represent the final shape of the cast part. This pattern is then coated with a refractory material, typically a mixture of fine sand and a binding agent. Once the coating has dried, the foam pattern is surrounded by molten metal. The heat from the metal causes the foam to vaporize, hence the term lost foam. The result is a casting that captures the intricate details of the pattern, with a surface finish that often requires little to no machining.
The Importance of Coating
The coating serves multiple purposes in the LFC process
1. Thermal Barrier It acts as an insulator, preventing rapid heat transfer from the molten metal to the foam. This regulation of temperature helps to maintain the integrity of the casting while preventing defects that can arise from premature vaporization.
2. Surface Finish A well-applied coating improves the surface finish of the final casting. This is essential for components that require tight tolerances or specific aesthetic qualities. The coating can fill in minor imperfections in the foam pattern, resulting in a smoother final product.
lost foam casting coating
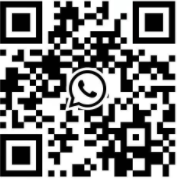
3. Control Over Sand Grain Structure The coating affects how the sand particles interact with each other and the molten metal. A uniform coating can lead to a more consistent grain structure in the sand mold, which in turn influences the mechanical properties of the final casting.
4. Bond Strength The quality of the coating determines the bond strength between the sand and the foam pattern. A strong bond minimizes the risk of sand erosion during the pouring of the molten metal, which can lead to defects in the casting.
5. Vaporization Management Properly formulated coatings can control the rate and manner of foam vaporization. This control is crucial in preventing defects such as burn-on surfaces, which occur when foam residues burn onto the casting surface.
Advancements in Coating Technologies
Recent advancements in coating technologies have improved the lost foam casting process. Innovations such as the development of new binding agents and refractory compounds have resulted in coatings that can withstand higher temperatures and provide even better insulation. These advancements have led to a broader range of materials that can be cast using the LFC process, including higher-strength alloys and complex composites.
Moreover, the use of nanotechnology in coatings has shown promise in enhancing the properties of the coating materials, providing better adhesion, improved heat resistance, and enhanced surface finish. As industries continue to demand components with higher precision and quality, these advancements in coating technologies will play a vital role in meeting these expectations.
Conclusion
Lost foam casting is an innovative method that offers significant advantages over traditional casting techniques. The role of coating in this process cannot be overstated, as it directly influences the thermal properties, surface finish, and overall integrity of the final product. As technology advances, the development of more effective coatings will continue to enhance the capabilities of lost foam casting, enabling manufacturers to produce increasingly complex and high-quality components. This combination of precision and efficiency positions lost foam casting as a leading choice in modern metal fabrication.
Post time:វិច្ឆិកា . 27, 2024 07:43
Next:The Significance of Sand Casting in Modern Manufacturing and Engineering Practices