Lost Foam Casting Coating A Comprehensive Overview
Lost foam casting is an innovative manufacturing process that allows for the creation of complex shapes and designs, particularly in metal casting. This method is favored for its ability to produce intricate details without the need for complex tooling. One crucial aspect of the lost foam casting process is the coating, which plays an essential role in ensuring the quality and precision of the final product. In this article, we will explore the importance of lost foam casting coating, its types, application methods, and the challenges faced in the process.
Importance of Coating in Lost Foam Casting
In lost foam casting, a polystyrene foam pattern is created and then coated with a layer of refractory material. This coating serves several critical functions
1. Surface Detail Preservation The coating is necessary to capture the fine details of the foam pattern. A good-quality coating prevents distortion or damage to the foam during the casting process.
2. Mold Integrity The coating provides structural integrity to the mold. It must withstand the heat and pressure of the molten metal without cracking or breaking, ensuring consistent and repeatable casting performance.
3. Heat Resistance Refractory coatings are designed to endure high temperatures. They must not only protect the foam from the molten metal but also resist thermal shock.
4. Metal Flow Control The coating helps in managing the flow of molten metal. It influences how the metal fills the mold cavity, which in turn affects the final shape and surface finish of the cast part.
Types of Lost Foam Casting Coatings
There are various types of coatings used in lost foam casting, each with distinct properties and applications
1. Ceramic Coatings These are the most common types of refractory coatings. They are made from a mixture of silica and clay, which provide excellent thermal resistance and can handle extreme temperatures.
2. Colloidal Silica Coatings This type utilizes a suspension of silica particles in water, offering high strength and excellent surface finish. Colloidal silica coatings are particularly useful for achieving fine details in the cast.
3. Acrylic Coatings These are lighter and easier to apply but may not offer the same level of heat resistance as ceramic or silica coatings. They are used in applications where the operating temperature is relatively lower.
4. Epoxy Coatings Known for their durability and strong bonding properties, epoxy coatings can be used to create a rigid outer shell around the foam pattern. They provide excellent protection against abrasion and impact.
lost foam casting coating
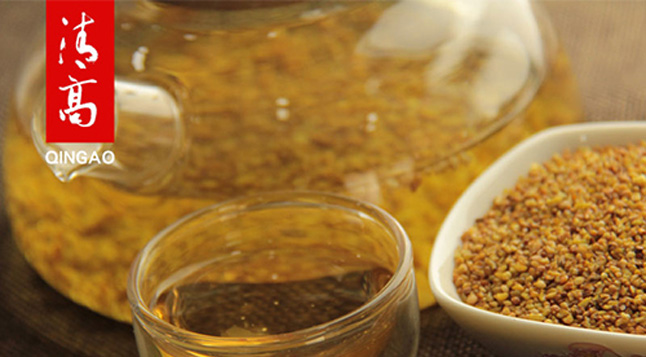
Application Methods
The application of coatings in lost foam casting can be performed using various techniques
1. Spraying This is one of the most common methods for applying coatings. It allows for even distribution and can create a smooth finish. Spray guns can be adjusted to control the thickness of the coating.
2. Dipping In this method, the foam pattern is submerged in a coating material. Dipping ensures that every part of the foam is adequately coated, which is crucial for preserving intricate details.
3. Brushing Although more labor-intensive, brushing may be used for smaller or complex patterns where precision is required. This method allows for greater control over the application thickness.
4. Casting For certain types of coatings, particularly those that are thicker, pouring the coating directly onto the foam pattern can be effective.
Challenges in Coating Application
While coating application may seem straightforward, several challenges need to be addressed
1. Temperature Control Maintaining the correct temperature during the coating process is essential to avoid premature drying or degradation of the coating material.
2. Environmental Conditions Humidity and temperature can significantly impact the coating’s performance. Ideally, the coating should be applied in a controlled environment to ensure consistency.
3. Coating Thickness Achieving the right thickness is critical. Too thick a coating can lead to defects in the final casting, while too thin may not provide sufficient protection.
4. Adhesion Issues Finding the right bond between the coating and foam is vital. Poor adhesion can lead to flaking and ultimately affect the quality of the cast part.
Conclusion
Lost foam casting coating is a pivotal factor that significantly influences the quality, detail, and integrity of cast products. By understanding the different types of coatings, their application methods, and the challenges faced, manufacturers can better navigate the lost foam casting process, ultimately resulting in superior castings that meet specific industry standards and customer expectations. As technology advances, innovations in coating materials and application methods will continue to evolve, further enhancing the capabilities of lost foam casting in various industries.
Post time:វិច្ឆិកា . 25, 2024 00:31
Next:Innovative Applications of 3D Printed Sand Casting in Modern Manufacturing Techniques