Lost foam casting is a revolutionary manufacturing process that has gained prominence in various industries due to its ability to produce complex metal parts with high precision. This technique involves creating a foam pattern that is subsequently coated with a ceramic shell, after which the foam is vaporized when molten metal is poured into the mold. This method offers numerous advantages over traditional casting processes, making it an appealing option for manufacturers looking to improve efficiency and reduce costs.
One of the most significant benefits of lost foam casting is its capacity for intricate designs. The foam patterns can be easily shaped to create complex geometries that would be difficult or impossible to achieve with traditional casting techniques. This flexibility in design allows engineers and designers to push the boundaries of what is possible, leading to innovative products that can enhance performance in various applications, from automotive components to aerospace parts.
Additionally, lost foam casting eliminates the need for elaborate core and pattern systems, which can streamline production. In many conventional casting processes, manufacturers must create molds and cores from metal or sand, requiring additional materials and labor. In contrast, the use of foam patterns reduces the overall material consumption and processing time, which can result in lower production costs. As a result, companies can produce parts more quickly and at a lower cost, providing a competitive edge in today’s fast-paced market.
Furthermore, lost foam casting is known for its excellent surface finish and dimensional accuracy. The process allows for tighter tolerances compared to other casting methods. This precision is crucial in industries where components must fit together perfectly to function correctly. As a result, manufacturers can minimize the need for post-casting machining, further saving time and costs.
lost foam casting
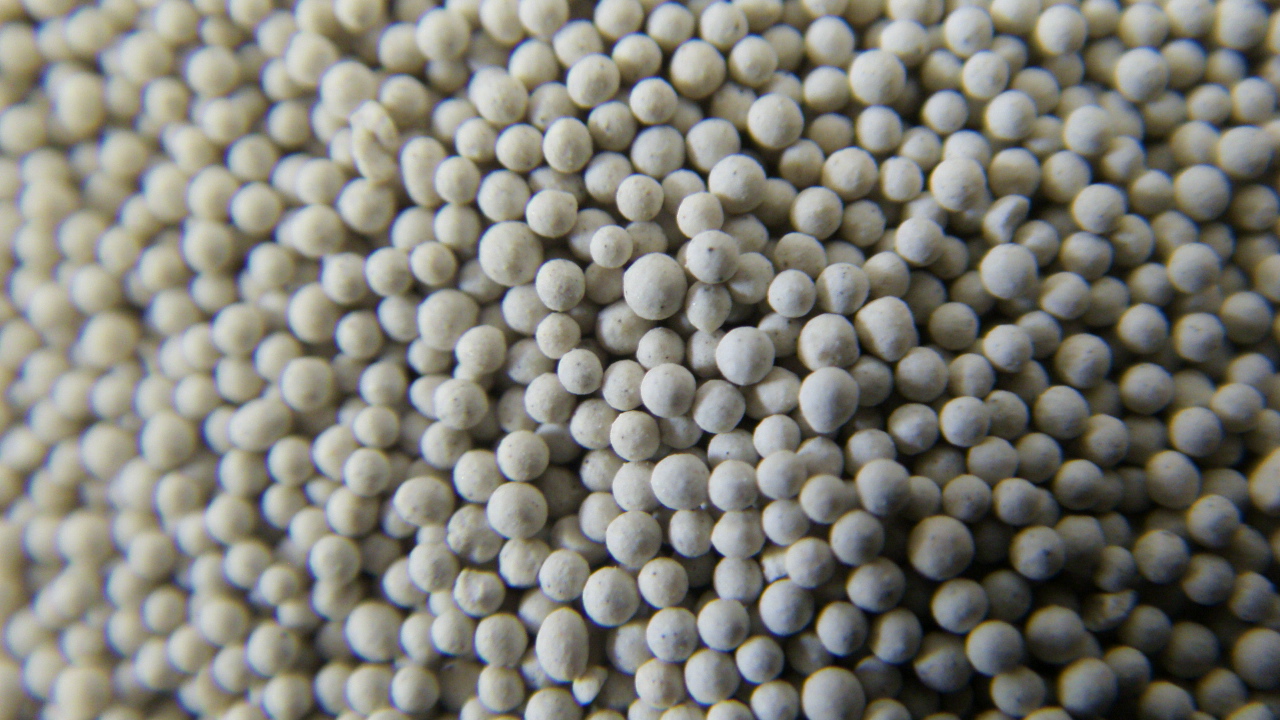
Environmental considerations also play a role in the appeal of lost foam casting. The process generates less waste than traditional methods since there is no need for additional materials like sand. Moreover, the foam used in this process can often be made from recyclable materials, contributing to a more sustainable manufacturing approach. This focus on sustainability is increasingly important as companies look to reduce their environmental impact and comply with stricter regulations.
One of the challenges associated with lost foam casting is the need for careful control of the pouring process to avoid defects such as misruns or inclusions. Additionally, the technology is still relatively specialized, which means that not all foundries may have the necessary expertise or equipment to implement it. However, as more organizations recognize the benefits of this technique, training and advancements in technology are helping to overcome these hurdles.
In conclusion, lost foam casting represents a significant advancement in manufacturing technology. By allowing for complex designs, reducing material waste, improving surface finish, and enhancing dimensional accuracy, this process has become an attractive option for various industries. As technology continues to evolve and industries demand more efficient production methods, lost foam casting is likely to play an increasingly important role in shaping the future of manufacturing.
Post time:តុលា . 31, 2024 22:01
Next:The Invention Timeline of Sand Casting Techniques and Their Historical Significance