The Importance of Large Sand Casting in Modern Manufacturing
Large sand casting is a pivotal process in the realm of manufacturing, particularly in producing intricate metal components. This technique utilizes sand as a primary molding material, offering numerous advantages that have made it a cornerstone of the foundry industry. In this article, we delve into the details of large sand casting, exploring its applications, benefits, and future prospects.
At its core, large sand casting involves creating a mold from sand that is then filled with molten metal to form various shapes and sizes. This method is particularly advantageous for large items such as engine blocks, large gears, and other significant components used in industries ranging from automotive to aerospace. The flexibility of sand casting allows for the creation of complex designs that are often challenging to achieve with other casting methods.
One of the most significant advantages of large sand casting is its cost-effectiveness. The materials used in this process are relatively inexpensive compared to other molding materials like metal or ceramic. Sand molds can be reused multiple times, further reducing production costs. Additionally, large sand casting allows for greater design freedom. Designers can create intricate shapes without the constraints faced by alternative casting methods, making it an ideal choice for custom and large-scale production.
Another critical benefit of large sand casting is its scalability. The process can be easily adapted to produce both small quantities of unique items and large batches of identical products. This adaptability is particularly crucial in industries where rapid prototyping and production are essential for maintaining a competitive edge.
large sand casting
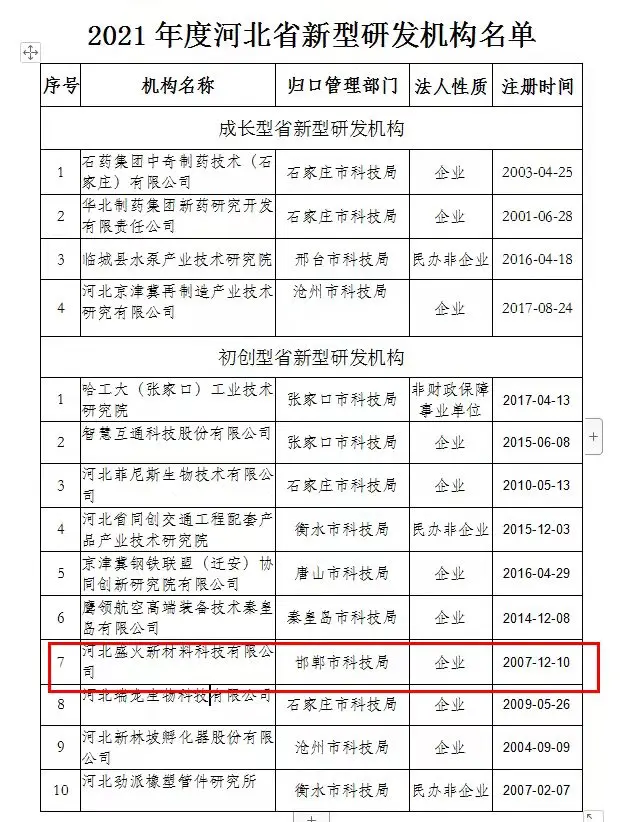
Furthermore, large sand casting promotes sustainability through its ability to use recycled materials. The sand from previous castings can often be cleaned and reused, significantly minimizing waste. Advances in technology are also enhancing the efficiency of this process, with innovations like 3D printing techniques paving the way for more precise sand molds, thereby reducing material consumption and improving overall production quality.
However, it is essential to acknowledge the challenges associated with large sand casting. Issues such as mold defects, surface finish quality, and dimensional accuracy can arise, necessitating stringent quality control measures during production. Nonetheless, continuous improvements in technology and practices have made it possible to mitigate these challenges effectively.
Looking to the future, large sand casting is poised to play a critical role in the ongoing evolution of manufacturing. As industries increasingly emphasize sustainability and efficiency, the demand for adaptable and cost-effective casting processes will likely grow. Innovations in automation and digital technologies promise to enhance the capabilities of sand casting, making it an even more appealing option for manufacturers around the globe.
In conclusion, large sand casting remains an indispensable method in manufacturing, providing a blend of cost-efficiency, design flexibility, and scalability. As technology continues to evolve, its relevance in various sectors is expected to expand, ensuring that it remains at the forefront of industrial processes for years to come.
Post time:កញ្ញា . 19, 2024 03:54
Next:iron sand casting