The Importance of Sand Casting in Manufacturing
Sand casting is one of the oldest and most versatile manufacturing processes used in the production of metal components. With a history that dates back thousands of years, it remains a fundamental technique in today's industrial landscape. The importance of sand casting can be highlighted through its advantages, applications, and its role in modern manufacturing.
Versatility and Adaptability
One of the greatest strengths of sand casting is its versatility. It can be used to create parts of various sizes, shapes, and complexities. From small jewelry components to large industrial machinery parts, sand casting can accommodate a wide range of applications. This adaptability makes it a preferred method for manufacturers in various industries, including automotive, aerospace, and engineering.
Moreover, sand casting can handle a diverse array of materials. Ferrous and non-ferrous metals, such as aluminum, iron, and brass, can all be cast using this method. The ability to work with different materials increases its utility across various manufacturing sectors, allowing businesses to meet specific requirements and preferences for their products.
Cost-Effectiveness
In terms of cost, sand casting is often more economical than other casting methods. The materials used, primarily sand, are relatively inexpensive and readily available. Additionally, the process can be easily scaled to accommodate both small and large production runs without significant upfront investment. This cost-effectiveness is particularly beneficial for small to medium-sized enterprises that may lack the financial resources for more expensive manufacturing techniques.
Sand casting also requires less sophisticated equipment compared to other casting methods like die casting or investment casting. The simplicity of the setup allows manufacturers to begin production quickly, reducing lead times and enhancing overall productivity. This efficiency is crucial in industries where time-to-market can significantly impact competitiveness.
Design Flexibility
The mold-making process in sand casting offers significant design flexibility. Patterns can be made from various materials, including wood, metal, or plastic, and can be easily modified to meet specific design changes. This flexibility enables manufacturers to innovate and iterate on designs without the need for substantial retooling or additional costs.
importance of sand casting
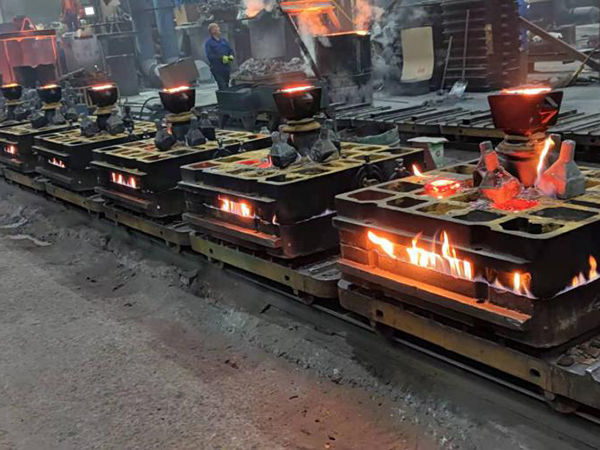
The process also allows for complex geometries, which are often challenging for other casting methods. Intricate designs with internal cavities, undercuts, or thick sections can be effectively produced, leading to lightweight components without compromising strength. This ability to create complex shapes is crucial in modern engineering applications, where functionality and weight reduction are essential.
Skill Development and Employment Opportunities
Sand casting also plays a vital role in skill development within the manufacturing workforce. As a traditional technique, it provides a foundation for understanding the principles of casting and metalworking. Skilled workers in this field are essential for maintaining quality and precision in the casting process, and their expertise is invaluable in troubleshooting and improving production techniques.
The sand casting industry creates numerous employment opportunities, ranging from pattern-making and mold preparation to machining and finishing. This direct connection to the labor market ensures that knowledge and skills in sand casting are passed down through generations, promoting a skilled workforce capable of supporting various manufacturing sectors.
Environmental Considerations
In recent years, environmental concerns have brought renewed attention to manufacturing processes, and sand casting is proving to be relatively sustainable. As sand is a natural resource that can be recycled and reused numerous times, the environmental impact of this method is lower than many alternatives. Many foundries now implement recycling systems to reclaim and reuse sand, minimizing waste.
Additionally, the use of sand casting can lead to reduced energy consumption compared to other casting methods. Since sand molds do not require heating, the overall energy input is lower, contributing to a smaller carbon footprint for manufacturers.
Conclusion
In summary, the importance of sand casting in manufacturing cannot be overstated. Its versatility, cost-effectiveness, design flexibility, and contribution to skill development all solidify its role as a cornerstone of metalworking. As industries continue to evolve and adapt to new technologies and sustainability challenges, sand casting remains a relevant and vital process in the production of high-quality metal components. Embracing the benefits of sand casting ensures that manufacturers can continue to innovate while maintaining efficiency and competitiveness in the market.
Post time:ធ្នូ . 04, 2024 18:26
Next:casting sand suppliers