How to Sand Cast A Step-by-Step Guide
Sand casting is a versatile and widely used metal casting process that has been around for centuries. This method is ideal for creating metal parts and components in various industries, from automotive to art. Whether you’re a hobbyist or a professional, understanding the sand casting process can greatly enhance your ability to produce high-quality castings. In this article, we will outline the steps involved in sand casting, highlighting essential techniques and considerations.
Materials Needed
Before diving into the sand casting process, you’ll need some essential materials 1. Sand Typically, fine silica sand is used, often mixed with clay for binding. 2. Binder Clay or a mixture of clay and water that helps hold the sand together. 3. Pattern The object you wish to cast, usually made of wood, metal, or plastic. 4. Metal The type of metal you will be casting (aluminum, bronze, etc.) 5. Mold Box A container used to hold the sand and form the mold. 6. Tools Such as trowels, rammers, and scraping tools for prepping the mold.
Step 1 Create the Pattern
The first step in the sand casting process is to create or obtain a pattern of the object you want to cast. This pattern needs to be slightly larger than the final product, allowing for the shrinkage that occurs as the metal cools. Patterns can be solid or hollow, depending on the complexity of the part.
Step 2 Prepare the Mold
Once you have your pattern, the next step is to prepare the mold. To do this, place the pattern in the mold box and fill the surrounding space with a mixture of sand and binder. It’s important to pack the sand tightly around the pattern to maintain its shape. Use a trowel or ramming tool to ensure the sand is compacted well.
When the sand has been packed around the pattern, you need to carefully remove the pattern from the sand. This creates a cavity that will be filled with molten metal. Make sure to create pins or alignment features in the mold design to keep the two halves aligned during casting.
Step 3 Assemble the Mold
In many cases, you will need to make two halves of the mold (cope and drag) to create a complete cavity for the casting. After removing the pattern, inspect the mold closely for defects or inconsistencies, as these will transfer to the final cast. If the mold halves fit well together, secure them using clamps or pins.
how to sand cast
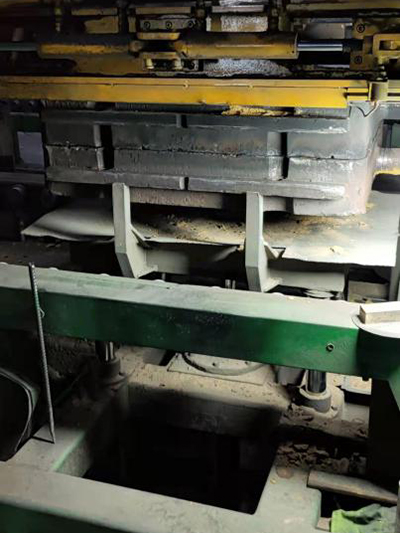
Step 4 Pour the Metal
Before pouring the metal, preheat the mold if necessary, especially when casting metals like aluminum, which can cool too quickly. Melt your chosen metal in a furnace until it reaches a liquid state. Carefully pour the molten metal into the mold through the designated sprue, ensuring that it fills the cavity completely without trapping air.
Step 5 Allow to Cool
Once the metal has been poured, allow it to cool and solidify. Cooling times will vary depending on the type of metal and thickness of the casting. It’s typically best to wait until the metal has completely hardened before attempting to dismantle the mold.
Step 6 Remove the Casting
After the metal has cooled, carefully separate the mold halves to retrieve your casting. Be cautious of any sharp edges or residual sand on the casting.
Step 7 Finishing Touches
Lastly, clean the casting by removing any sand and inspecting it for quality. You can use tools such as grinders, sanders, or files to achieve the desired surface finish. Depending on the application, additional treatments like annealing or coating may improve the casting’s properties.
Conclusion
Sand casting is an accessible and effective method for producing metal parts and components. By following these steps, you can create high-quality castings suitable for various applications. With practice and attention to detail, you'll be able to refine your sand casting technique and create impressive results. Enjoy the process and the satisfaction of bringing your designs to life through sand casting!
Post time:វិច្ឆិកា . 27, 2024 15:23
Next:Current Trends in Gold and Sand Prices and Their Market Impact