How to Make Foundry Sand
Foundry sand plays a crucial role in the metal casting industry, helping to create molds and cores for various metal products. The quality and properties of foundry sand can significantly affect the final cast product's integrity. While many foundries use silica sand, it's important to know how to prepare and enhance foundry sand to meet specific casting requirements. In this article, we’ll explore the process of making foundry sand, including its composition, preparation, and important considerations.
Understanding Foundry Sand
Foundry sand is a specially graded form of silica sand that is used in foundries for casting. It is characterized by its excellent thermal stability and ability to retain moisture, making it ideal for creating molds. The primary component of foundry sand is silica (SiO2), usually ranging from 90% to 99%, along with other materials, such as clay and water, to enhance its binding properties. High-quality foundry sand is essential for achieving smooth surface finishes and dimensional accuracy in castings.
Raw Materials
To make effective foundry sand, gather the following materials
1. Silica Sand Choose high-grade silica sand with a uniform grain size. The size usually ranges between 0.2 mm to 0.8 mm for optimal molding characteristics. 2. Clay Bentonite clay is often used to improve the bonding properties of the sand. It should be added in small percentages (typically around 5%). 3. Water Water is necessary to activate the clay and ensure that the sand holds its shape during the molding process. 4. Additives (Optional) Depending on the specific application, various additives may be included to increase strength, improve thermal stability, or enhance flowability.
Preparation Steps
how to make foundry sand
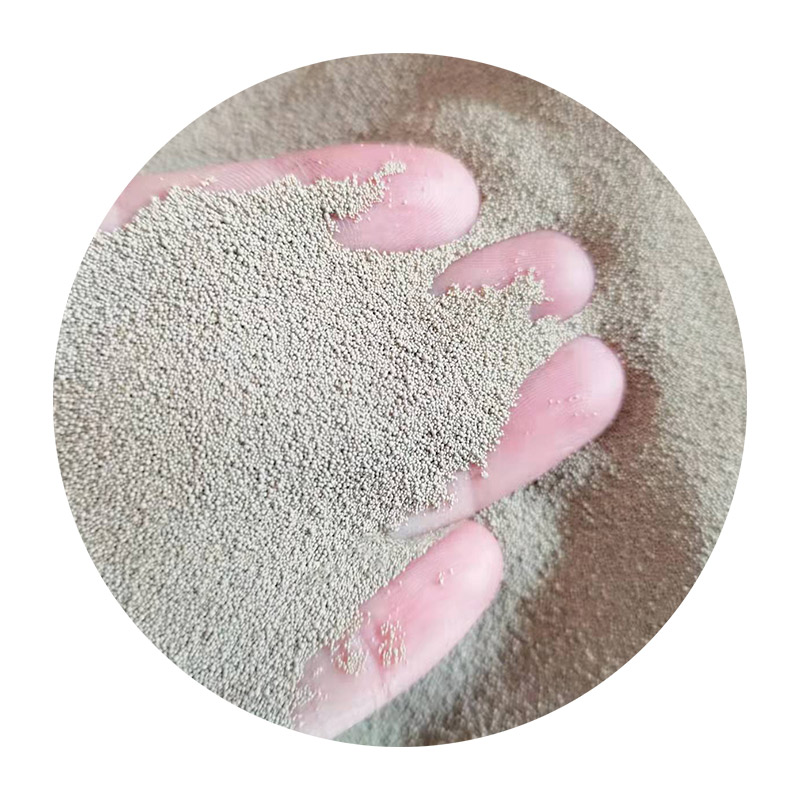
1. Sand Selection Start with selecting the silica sand. Make sure it is clean and free of impurities, as contaminants can negatively impact the casting process.
2. Mixing In a large mixing container, combine the silica sand and bentonite clay. Thoroughly mix the two until the clay is evenly distributed throughout the sand. This is a critical step to ensure that the binding properties are optimally enhanced.
3. Moisture Addition Gradually add water to the mixture. The amount of water depends on the specific requirements of the casting process, but it is generally around 2-5% of the total weight of the sand. Mix thoroughly to achieve a uniform consistency. The right moisture content is crucial as too little can make the sand dry and crumbly, while too much can lead to poor mold integrity.
4. Testing Consistency Before using your prepared sand, you should perform a consistency test. A simple method is to take a handful of the mixture and squeeze it. If it holds its shape without falling apart, it is ready for use.
5. Storage If not used immediately, store the prepared foundry sand in a cool, dry place to maintain its quality. Moisture buildup can lead to clumping and reduced performance.
Conclusion
Creating foundry sand involves careful selection of materials and precise preparation techniques. The quality of foundry sand directly influences the efficiency of the casting process and the quality of the final product. By following the steps outlined in this guide, you'll be well on your way to producing high-quality foundry sand tailored to your specific metal casting needs. Whether you're a hobbyist or working in a professional foundry, mastering the art of making foundry sand can enhance your casting results significantly.
Post time:វិច្ឆិកា . 08, 2024 03:37
Next:Understanding the Materials Utilized in Sand Casting Processes for Effective Manufacturing