How to Make Foundry Sand
Foundry sand is a crucial material used in the metal casting industry. It plays an essential role in creating molds and cores for various metal components. The quality of foundry sand directly impacts the final product's surface finish and overall integrity. In this article, we will explore the process of making foundry sand, including its components, preparation, and usage.
Understanding Foundry Sand
Foundry sand is predominantly made from silica (SiO2), which is known for its excellent thermal stability and ability to withstand high temperatures. The sand used in foundries often undergoes processes to enhance its properties, making it suitable for casting purposes. Besides silica, foundry sand may contain additives such as clay and other bonding agents to improve its cohesiveness and facilitate the mold-making process.
The Components of Foundry Sand
1. Silica Sand The primary ingredient that forms the base of foundry sand. The size and shape of the sand grains are vital as they affect how well the sand can retain its form when molded.
2. Clay Often added to bind the sand grains together, clay helps improve the strength and integrity of the mold. Common types of clay used include bentonite, which can absorb water and swell, providing excellent mold-making properties.
3. Additives Other materials like olivine sand, chromite sand, or zircon sand may be included to impart specific properties, such as improved thermal resistance or reduced reactivity.
Steps to Make Foundry Sand
Step 1 Selecting the Sand
Begin with selecting high-quality silica sand. The sand should be clean, free from impurities, and have a consistent grain size. It's essential to choose the right type of sand based on its intended application – whether for ferrous or non-ferrous metals.
Step 2 Preparing the Sand Mixture
how to make foundry sand
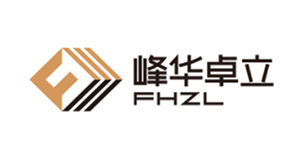
1. Washing Clean the selected sand to remove any contaminants such as dust, dirt, or clay. This washing process is crucial to ensure a high-quality final product.
2. Drying Once washed, the sand needs to be dried to eliminate any moisture content. This step can be done using rotary dryers or in the sun, depending on the scale of operations.
3. Mixing with Clay After drying, mix the sand with a specific percentage of clay (usually around 2-5%) to improve its binding properties. The clay should be well-dispersed throughout the sand to ensure uniformity.
4. Adding Water Gradually introduce water to the mixture while continuously mixing. The desired moisture content will depend on the specific application, so it's important to achieve the right consistency – not too dry, which would lead to poor mold strength, or too wet, which could cause mold failure.
Step 3 Testing the Mixture
Conduct a series of tests on the sand mixture to ensure it meets the required specifications. Common tests include
- Green Compression Strength Measures the strength of the mold before drying. - Permeability Test Ensures that gases can escape from the mold during the casting process. - Moisture Content Test Verifies that the right amount of moisture is added.
Step 4 Using the Foundry Sand
Once the foundry sand is prepared and tested, it is ready to be used in the molding process. The sand can be packed around patterns to form molds or used to create cores for hollow parts. The quality of the sand directly influences the casting's surface finish and dimensional accuracy.
Conclusion
Making foundry sand is a detailed process that requires a good understanding of materials and their properties. By selecting the right silica sand, blending it with appropriate additives, and closely monitoring moisture content, one can create high-quality foundry sand that meets industry standards. Whether for automotive parts or intricate machinery components, proper preparation of foundry sand is fundamental to achieving superior casting results.
Post time:តុលា . 10, 2024 21:39
Next:Creative Concepts for Sand Casting Techniques and Innovations