Understanding the Accuracy of Sand Casting A Comprehensive Overview
Sand casting is one of the oldest and most versatile casting processes used in manufacturing. This technique involves the use of sand as the primary mold material. While it offers various advantages, one of the critical aspects that engineers and manufacturers consider is the accuracy of the sand casting process. Understanding how accurate sand casting can be is essential for various applications, from automotive components to intricate artistic pieces.
The Basics of Sand Casting
Sand casting begins with creating a mold from a pattern of the desired object. The pattern is typically made of metal, plastic, or wood and is designed to be slightly larger than the final product to account for shrinkage. The mold is formed by packing sand around the pattern, which is then removed to leave a cavity in the shape of the final part. Molten metal is poured into the cavity, allowed to cool, and then the sand mold is broken away to reveal the cast metal part.
Accuracy Factors in Sand Casting
While sand casting is known for its flexibility and ability to produce complex shapes, its accuracy is influenced by several factors
1. Pattern Accuracy The precision of the pattern is vital to ensure that the final product matches the intended dimensions. Any inaccuracies in the pattern will translate directly to the cast part.
2. Mold Integrity The quality of the sand mold plays a significant role in the final accuracy. Factors such as the grain size of the sand, the binder used, and the moisture content can affect how well the mold holds its shape during pouring and cooling.
3. Shrinkage Metals tend to shrink as they cool. This phenomenon can lead to dimensional discrepancies between the cast part and the original pattern. Understanding the specific shrinkage characteristics of the metal being used is essential for achieving the desired accuracy.
4. Pouring Temperature The temperature of the molten metal when poured can impact the final accuracy. If the metal is too hot, it can lead to defects such as pouring sand inclusions, while pouring at too low a temperature can cause inadequate filling of the mold.
how accurate is sand casting
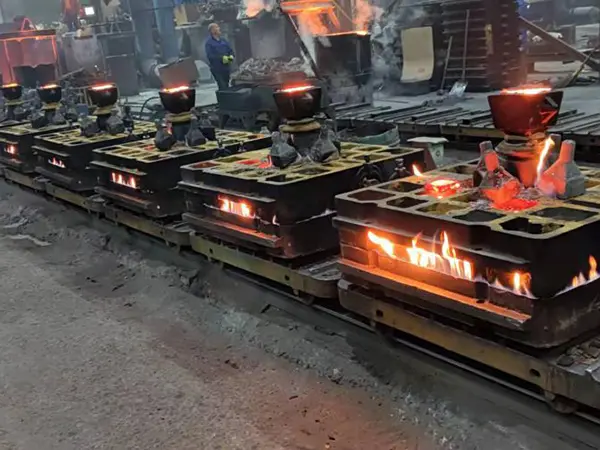
5. Cooling Rate The cooling rate affects not only the dimensions of the part but also its mechanical properties. Uneven cooling can lead to warping or cracking, further impacting accuracy.
6. Finish and Tolerance The surface finish of sand-cast components can vary significantly. Generally, sand casting provides a rougher finish compared to other methods like die casting. This roughness can affect how closely the finished part meets specific tolerances required for assembly with other components.
Achieving Greater Accuracy
To enhance the accuracy of sand casting, manufacturers often employ several strategies
- Use of Core Sand By incorporating core sand techniques, manufacturers can create internal cavities that help improve the dimensional accuracy of the cast product.
- 3D Printing The advent of 3D printing technology has allowed for the creation of highly accurate patterns, reducing discrepancies that arise during traditional pattern making.
- Post-Casting Operations Many manufacturers also rely on machining processes after casting to achieve precise dimensions and tolerances where required.
- Quality Control Implementing strict quality control practices during the casting process can help catch and rectify inaccuracies early, ensuring a higher quality output.
Conclusion
In conclusion, while sand casting is a widely used production method known for its flexibility and cost-effectiveness, achieving accuracy can be challenging due to various influencing factors. Understanding these factors and employing techniques to mitigate inaccuracies can significantly enhance the precision of sand-cast parts. As technology advances and new techniques are introduced, the accuracy of sand casting will likely continue to improve, making it an even more viable option for a variety of manufacturing applications. Whether in artistic creations or industrial components, achieving the right balance of flexibility and precision is key to the success of sand casting in today's competitive landscape.
Post time:វិច្ឆិកា . 07, 2024 16:45
Next:Techniques for Wet Sanding 3D Printed Models for a Smooth Finish