The Versatile Applications of Foundry Sand
Foundry sand, primarily composed of silica (SiO₂), has a critical role in the metal casting industry. Its unique properties, such as grain size, shape, and thermal conductivity, make it an indispensable material in various foundry operations. This article explores the diverse uses of foundry sand, highlighting its significance and potential in numerous applications.
1. Metal Casting
The most prominent use of foundry sand is in the production of metal castings. Foundries utilize this sand to create molds and cores that shape molten metals. Foundry sand is favored due to its ability to withstand high temperatures—often exceeding 1,500°F—without breaking down. The sand's fine grain structure allows for detailed patterns and smooth finishes, which are crucial for producing intricate components such as automotive parts, machinery, and aerospace components. These molds ensure that metals cool and solidify uniformly, minimizing defects and improving the overall quality of the cast products.
2. Reclamation Processes
As foundry operations grow increasingly environmentally conscious, the reclamation of used foundry sand has become paramount. Through advanced techniques, foundries can recycle used sand, removing impurities and restoring its properties for reuse. This not only reduces waste but also cuts costs associated with buying new sand. Reclaimed foundry sand can be utilized to produce new molds and cores, contributing to a more sustainable casting process.
In recent years, reclaimed foundry sand has found a significant role in construction. Its composition and stability make it an excellent material for various construction applications, including concrete production, asphalt mixtures, and road base materials. By incorporating foundry sand into concrete, engineers can enhance the physical properties of the material while also reducing the environmental impact associated with mining virgin sands. Studies have shown that using foundry sand can improve the compressive strength of concrete, offering a sustainable alternative to traditional aggregates.
foundry sand uses
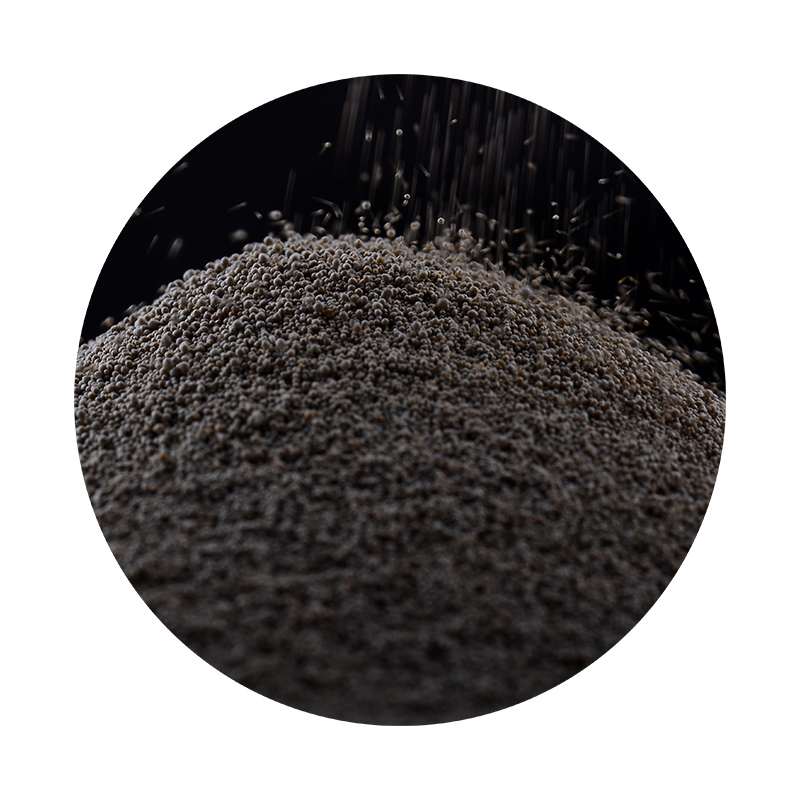
4. Environmental Applications
Foundry sand's unique properties have also led to its application in environmental initiatives. It is often used as a sustainable filtration medium in stormwater management systems. The fine grains of foundry sand act as effective filters that assist in removing pollutants from water, making it an essential component in the treatment of industrial and urban runoff. Additionally, using foundry sand in landscaping helps improve soil structure and drainage, benefiting both commercial and residential properties.
5. Sand Blasting and Abrasives
The use of foundry sand extends beyond casting and construction into the realm of abrasive materials. Its angular grain structure makes it ideal for sandblasting applications, where it can be used to clean or finish various surfaces. Foundry sand serves as an effective media for preparing surfaces for painting, coating, or welding, ensuring optimal adhesion and finish quality. Moreover, it is often employed in the production of sandpaper and other grinding tools, further emphasizing its versatility.
6. Artistic and Decorative Uses
Finally, foundry sand is also making waves in artistic applications. Sculptors and artisans build intricate designs and works of art using molds made from foundry sand. Additionally, the unique textures and finishes achieved with foundry sand can enhance various decorative projects, allowing artists to explore new dimensions in their craft.
In conclusion, foundry sand is more than just a material for metal casting; it serves a myriad of purposes across various industries. From construction to environmental management to artistic endeavors, the versatility of foundry sand emphasizes its importance in modern applications. As industries continue to seek sustainable practices and innovative solutions, foundry sand's role will undoubtedly expand, making it a cornerstone of future developments in numerous fields.
Post time:វិច្ឆិកា . 19, 2024 05:03
Next:Sanding Techniques for Achieving Smooth Finish on 3D Printed Resin Models