Understanding Foundry Sand Composition
Foundry sand, primarily used in metal casting processes, plays a crucial role in achieving high-quality casts. The composition of foundry sand is a critical factor that affects the performance of molds and cores, impacting the overall quality of the final product. This article delves into the key components of foundry sand, their sources, properties, and implications for casting operations.
Composition of Foundry Sand
The primary component of foundry sand is silica sand, which is known for its thermal stability and ability to withstand high temperatures during the casting process. The silica content in foundry sand typically ranges from 85% to 95%. The shape and size of the sand grains are also pivotal; round grains provide better flow characteristics and compaction compared to angular grains, which can hinder mold integrity.
In addition to silica, foundry sand may contain other minerals such as clay and coal dust. Clay, often added to enhance the binding properties of the sand, improves the strength and cohesion of the mold. It helps in retaining the shape of the mold during pouring and cooling of the metal. Coal dust, or other carbonaceous materials, can be added to facilitate the molding process and reduce oxidation of the molten metal.
Sources of Foundry Sand
The extraction of foundry sand typically comes from natural sources like riverbeds and quartzite deposits. The quality of foundry sand is determined by its mineral composition, grain shape, and size distribution. High-quality silica sand should have minimal impurities and a consistent grain size to ensure uniform performance in casting applications.
foundry sand composition
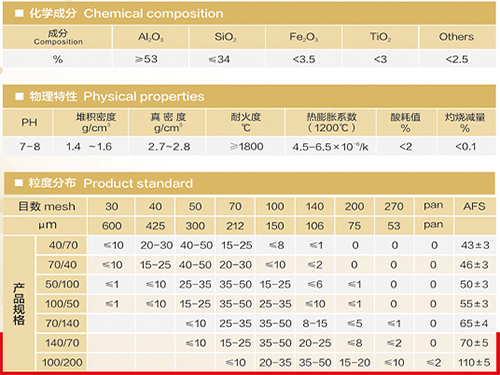
Recycling of foundry sand is also an emerging trend in the industry. Used sand, after being properly processed and cleaned, can be reclaimed and reused, significantly reducing waste and improving sustainability. Recycled foundry sand retains many of the properties of virgin sand, making it a viable alternative in various applications.
Properties Affecting Casting Performance
The performance of foundry sand directly influences casting results. Key properties include permeability, thermal stability, and strength. Permeability allows gases generated during metal pouring to escape, preventing defects such as blowholes. Thermal stability ensures that the sand maintains its structural integrity under extreme temperatures, critical for achieving precise molding.
Mold strength, influenced by the sand's composition and moisture content, determines the mold's ability to withstand the pressure of the molten metal without collapsing. Managing the moisture content is essential, as it affects the sand's bonding capabilities and, therefore, the overall quality of the casting.
Conclusion
In conclusion, the composition of foundry sand is integral to the casting process and the quality of the final product. By understanding the significance of silica content, the role of additives like clay and coal dust, and the impact of physical properties, foundry operators can make informed decisions to optimize their processes. Emphasizing sustainability through recycling further enhances the efficiency and environmental responsibility of foundry operations. As technology advances, the exploration of new materials and compositions may lead to even greater improvements in foundry practices, ensuring a promising future for the industry.
Post time:វិច្ឆិកា . 02, 2024 10:20
Next:foundry sand definition