Foundry Sand A Critical Component in Metal Casting
Foundry sand, a vital material in the metal casting industry, primarily consists of silica sand. Its unique properties make it suitable for creating molds and cores that shape molten metal into desired forms. The use of foundry sand dates back thousands of years, although modern practices have significantly evolved to improve efficiency and reduce environmental impact.
One of the most important characteristics of foundry sand is its ability to withstand high temperatures. When metal is poured into a mold made from this sand, the material must endure extreme heat without breaking down or losing its integrity. Silica sand is favored because of its high melting point, which allows it to maintain shape and support during the casting process. Additionally, its fine grain size provides a smooth surface finish, which is crucial for producing high-quality metal components.
The casting process begins with the preparation of the sand mixture. Foundry sand is often treated with bonding agents to enhance its cohesiveness and strength. Common binders include clay, resin, and various chemical additives that help stabilize the sand, improve its tensile strength, and reduce moisture content. The specific mixture used often depends on the type of metal being cast and the desired properties of the final product.
After the sand is prepared, it is molded into the desired shape. This can be done using various molding techniques, including green sand molding, lost foam casting, and investment casting. Each method has its advantages and is chosen based on production requirements. For instance, green sand molding, which utilizes a mixture of sand, clay, and water, is widely adopted for its cost-effectiveness and simplicity.
foundry sand
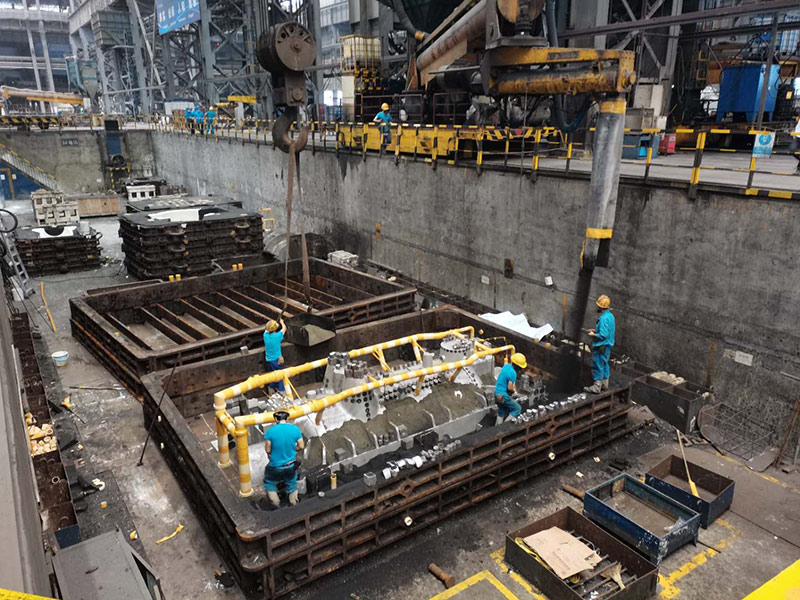
Once the mold is formed, molten metal is poured into it. The thermal conductivity of foundry sand plays a crucial role here, as it allows for even heat distribution, minimizing the risk of defects like cold shuts or misruns in the final cast. After the metal has cooled and solidified, the sand is typically broken away to reveal the finished product.
The lifecycle of foundry sand does not end with casting. In fact, one of the primary concerns within the foundry industry is the sustainable management of sand. As a non-renewable resource, the extraction and disposal of foundry sand must be carefully controlled. Fortunately, many foundries are now implementing recycling processes that allow treatment and reuse of sand multiple times before disposal. This practice not only minimizes waste but also reduces the environmental footprint of foundry operations.
Moreover, the proper disposal of used foundry sand is essential to prevent environmental contamination. Innovative solutions, such as using it in construction materials or as a soil amendment, have been explored to ensure that foundry sand contributes positively to the environment after its primary use.
In conclusion, foundry sand serves as a cornerstone in the metal casting industry, providing the necessary properties for effective mold creation and durability during the casting process. As the industry moves towards more sustainable practices, the management and recycling of foundry sand will remain a focal point, ensuring that this vital resource continues to support metal casting for years to come.
Post time:កញ្ញា . 14, 2024 19:01
Next:supersands