Dry Sand Casting An Overview of the Process and Benefits
Dry sand casting is a widely utilized manufacturing process that involves the use of dry sand molds to produce metal castings. This method is particularly advantageous for producing complex shapes and high-quality surface finishes while minimizing the overall production costs. In this article, we will explore the various aspects of dry sand casting, including its process, benefits, applications, and considerations.
The Process of Dry Sand Casting
The dry sand casting process begins with the preparation of the sand. Dry sand is selected based on its properties, such as grain size and permeability. The sand is then mixed with a binding agent, typically a phenolic resin, which helps the sand particles adhere together when subjected to heat. This binding agent is essential because it allows the sand mold to maintain its shape during the casting process and ensures a high-quality finish on the final product.
Once the sand mixture is ready, it is compressed into a mold using a molding machine. The mold consists of two halves the cope (top half) and the drag (bottom half). After the mold halves are formed and any necessary cores are placed within them to create internal cavities, the two halves are assembled, and the mold cavity is ready for pouring.
The next step involves heating the metal to its molten state, typically using induction furnaces or cupola furnaces. Once the metal reaches the desired temperature, it is poured into the mold cavity through a designated pouring gauge, overcoming gravity. The liquid metal fills the mold, taking on its shape. After cooling, which usually takes a few hours, the mold is opened, and the casting is removed.
Benefits of Dry Sand Casting
One of the primary advantages of dry sand casting is its ability to produce intricate shapes with a high level of detail
. The dry sand mold can capture fine features, leading to high-quality surface finishes that often require minimal machining after casting.Additionally, the use of dry sand molds allows for good heat conductivity, facilitating even and efficient cooling of the metal. This feature helps reduce defects such as porosity and shrinkage, ultimately enhancing the integrity of the casting.
Dry sand casting also offers flexibility in terms of production volume. It is suitable for both prototype and high-volume production runs, making it an appealing option for numerous industries, including automotive, aerospace, and consumer goods.
dry sand casting
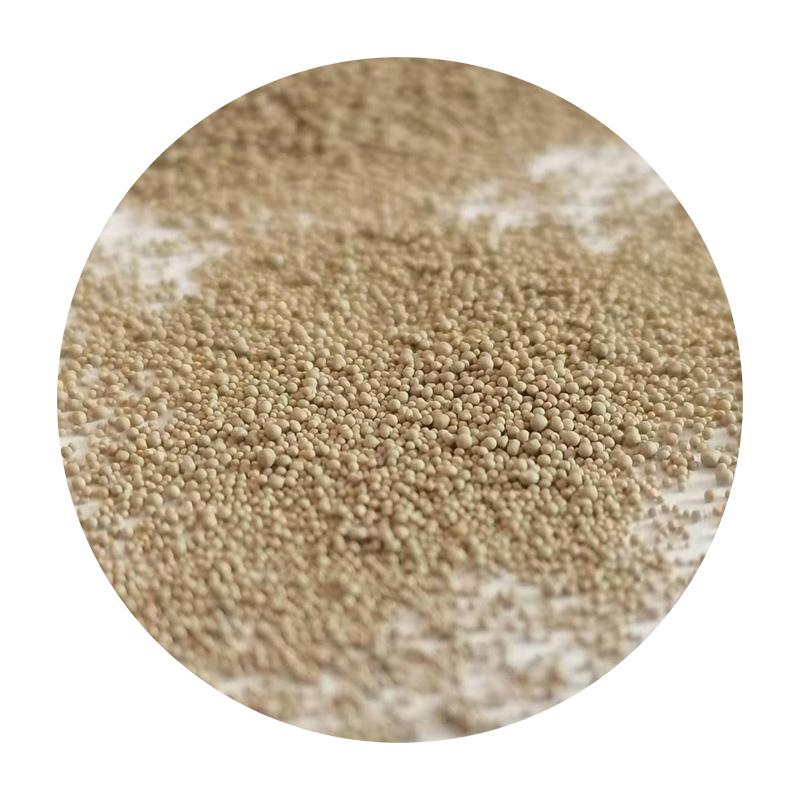
Moreover, the process is environmentally friendly compared to other casting methods. The dry sand used is often recyclable, reducing waste and lowering material costs. The absence of water in the mold preparation minimizes the environmental footprint, aligning with sustainable manufacturing practices.
Applications of Dry Sand Casting
Dry sand casting is employed in various industries where precision and quality are paramount. Components made from this process include engine blocks, pump housings, brackets, and various machinery parts. The automotive industry, in particular, benefits from dry sand casting for producing lightweight and durable components.
The aerospace sector also utilizes dry sand casting for critical components that require both strength and weight reduction. High-performance alloys are often cast using this method, resulting in parts that withstand high temperatures and stress.
Considerations in Dry Sand Casting
Despite its many advantages, dry sand casting comes with a few considerations. One key aspect is the initial setup cost, which can be relatively high due to the need for specialized equipment. Furthermore, the process may require expertise in mold design and preparation, which could limit its use for smaller operations without the necessary know-how.
Another consideration is the need for strict quality control measures during the pouring and cooling phases. Any inconsistencies in metal temperature or pouring speed may lead to defects in the final casting.
Conclusion
In summary, dry sand casting is a versatile and effective method for producing high-quality metal castings. Its ability to create intricate designs while ensuring durability and surface quality makes it an attractive option across multiple industries. As technology advances and companies shift towards sustainable practices, the demand for dry sand casting is likely to continue growing, further establishing its importance in the manufacturing landscape.
Post time:ធ្នូ . 03, 2024 18:06
Next:Achieve Flawless 3D Prints Effortlessly Without the Need for Sanding Techniques