Different Types of Foundry Sand
Foundry sand plays an essential role in the metal casting process, providing the mold for shaping molten metal into various products. The choice of sand greatly affects the quality of the final castings, the production efficiency, and the overall cost of the casting operation. There are several types of foundry sand, each with unique characteristics and applications. In this article, we will explore the most common types of foundry sand, their properties, and their uses.
1. Silica Sand
Silica sand is the most widely used type of foundry sand due to its abundance and cost-effectiveness. It is primarily composed of silicon dioxide (SiO2) and features excellent thermal stability and moldability. Silica sand is suitable for producing a variety of metal castings, particularly iron and steel. Its grains can vary in size and shape, influencing the surface finish and dimensional accuracy of the castings. However, it has a high hardness that can lead to wear on the machinery used in the casting process.
2. Chromite Sand
Chromite sand is a special type of sand derived from chromite ore, which is primarily composed of chromium oxide. This type of sand exhibits high thermal conductivity, thermal stability, and low expansion rates, making it particularly advantageous for the casting of high-performance alloys. Chromite sand is often used for casting processes that require superior surface finish and dimensional accuracy. Its resistance to deformation under high temperatures helps maintain the integrity of the molds, resulting in excellent casting quality.
3. Zircon Sand
Zircon sand is another high-performance foundry sand made from zirconium silicate. It is known for its high melting point, low thermal expansion, and excellent chemical stability. Zircon sand is often used in applications where high precision and excellent surface finishes are required. Castings made using zircon sand are often showcased in industries such as aerospace and automotive, where the performance and durability of components are critical. However, zircon sand is more expensive than silica or chromite sands, which limits its use to specialized applications.
different types of foundry sand
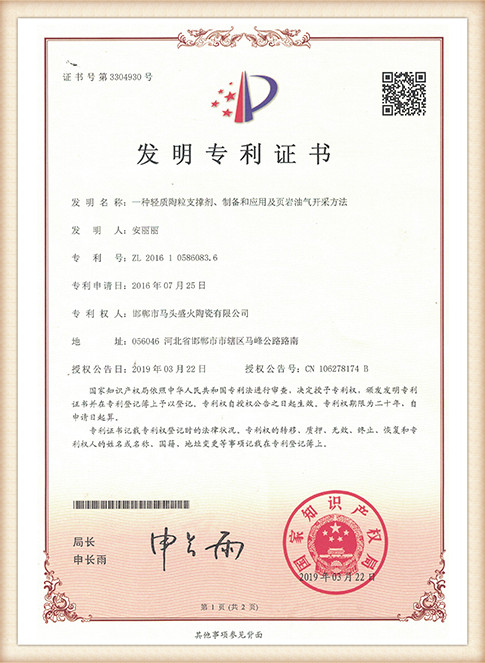
4. Olivine Sand
Olivine sand is derived from the mineral olivine and is characterized by its high thermal stability and resistance to thermal shock. Olivine sand’s low expansion characteristics make it well-suited for casting applications that demand dimensional accuracy and a low defect rate. It can be particularly advantageous in the production of ferrous and non-ferrous castings, often finding use in the automotive industry. Although it offers unique benefits, olivine sand is not as widely used as silica or chromite sand, mainly due to availability and cost factors.
5. Green Sand
Green sand is a mixture of silica sand, clay, and water, making it one of the most traditional types of foundry sand. This type of sand gets its name from the moisture content present in the mixture when it is prepared for casting. Green sand molds are versatile and can be used for a wide variety of casting processes, particularly in iron and aluminum foundries. The clay in green sand helps bind the grains together, promoting excellent mold details and allowing for easy reusability after the casting process. However, green sand does require tempering to ensure consistency in performance.
6. Resin-Coated Sand
Resin-coated sand is an innovative foundry material that combines sand with a thermosetting resin. This type of sand has gained popularity due to its enhanced properties, which include high strength and improved surface finish. Resins can be cured using various methods, such as heat or chemical catalysts, allowing for a quick turnaround time in the casting process. Resin-coated sand is particularly useful in the production of complex shapes and thin-walled castings. Its ability to withstand high temperatures makes it suitable for various alloys and applications.
Conclusion
The choice of foundry sand significantly influences the efficiency and quality of the casting process. Each type of foundry sand has its unique properties and applications, catering to specific industrial requirements. By understanding the differences between silica, chromite, zircon, olivine, green, and resin-coated sands, foundry operators can make informed decisions that optimize their casting operations and enhance the overall production quality.
Post time:ធ្នូ . 14, 2024 04:44
Next:Exploring the Benefits and Techniques of Sand Casting for Metal Fabrication