Different Types of Foundry Sand
Foundry sand plays a crucial role in the metal casting process, providing a moldable material that can withstand high temperatures. It is essential for producing high-quality castings in various metals, including aluminum, iron, and brass. There are several types of foundry sand, each with unique properties suited to specific applications. This article explores the most common types of foundry sand, emphasizing their characteristics and uses.
1. Silica Sand
Silica sand, or quartz sand, is the most widely used type of foundry sand. Composed primarily of silicon dioxide (SiO2), it has excellent thermal and chemical stability, making it ideal for high-temperature applications. Silica sand is available in various grain sizes, allowing foundries to select the appropriate type based on the desired finish and mold strength. Its high melting point helps prevent deformation during the casting process. However, the fine grains can create a dust hazard, necessitating proper handling procedures.
2. Olivine Sand
Olivine sand is another significant type of foundry sand, primarily composed of magnesium iron silicate. It has a high melting point and excellent thermal conductivity, making it suitable for casting ferrous and non-ferrous metals. The unique feature of olivine sand is its low thermal expansion, which minimizes mold distortion. Additionally, it has a relatively low density, making it lightweight and easy to handle. While olivine sand is more expensive than silica sand, its beneficial properties often justify the cost for high-quality castings.
3. Clay-based Sand
different types of foundry sand
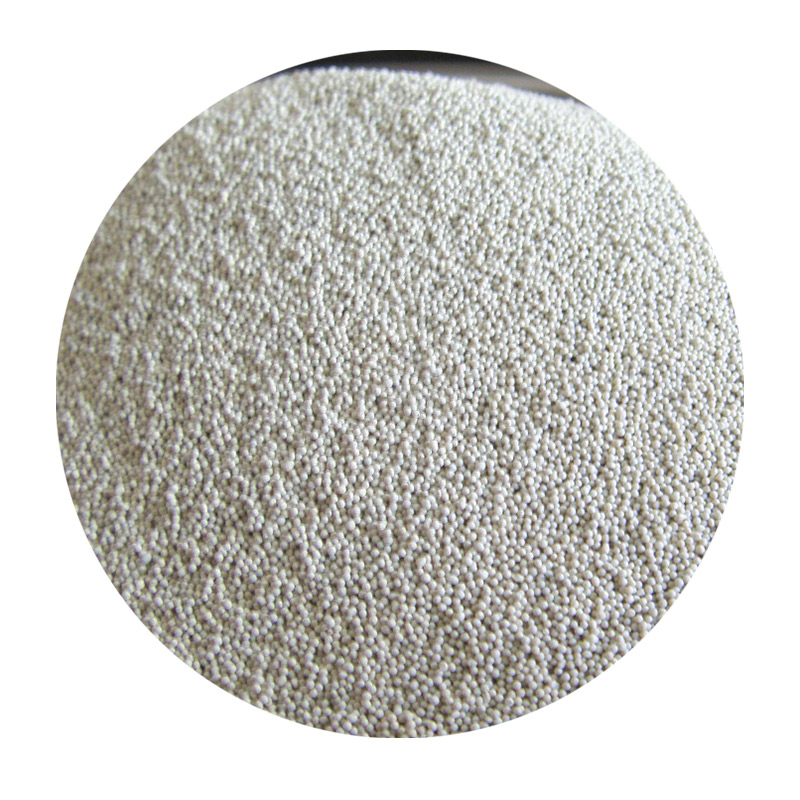
Clay-based sand includes a mixture of sand, clay, and water, commonly referred to as green sand. This type of sand is favored for its plasticity, allowing it to conform easily to the mold patterns. The clay binder provides strength and helps retain moisture, which is essential for the sand's cohesion. Green sand is particularly effective for producing castings quickly and is often used in iron and steel foundries. However, it may not provide the same level of detail as other types of sand, affecting surface finishes.
4. resin-coated Sand
Resin-coated sand is a modern alternative to traditional sands. It consists of regular sand particles coated with phenolic resin, which hardens upon heating. This type of sand allows for enhanced mold strength and dimensional accuracy, making it ideal for high-stress applications. The use of resin-coated sand also improves the surface finish of the casting, reducing the need for extensive machining processes afterward. While more expensive than conventional sands, its advantages often outweigh the costs in precision applications.
5. Zircon Sand
Zircon sand, primarily composed of zirconium silicate, is known for its exceptional thermal stability and resistance to chemical corrosion. Although more costly than silica or olivine sands, it is favored for producing high-quality castings in demanding applications, such as aerospace and automotive industries. Zircon sand's low thermal expansion ensures precise mold sizes, contributing to the overall quality of the final casting. Its properties make it an ideal choice for complex geometry and thin-walled castings.
Conclusion
In conclusion, foundry sand is an integral component of the metal casting industry, with various types catering to different casting requirements. Silica sand remains the most popular choice due to its availability and cost-effectiveness. However, alternative sands like olivine, clay-based, resin-coated, and zircon offer specialized properties that may be more suitable for specific applications. Ultimately, the selection of foundry sand depends on the desired characteristics of the final product, mold integrity, and overall production efficiency. By understanding the various types and their respective benefits, foundries can make informed decisions that enhance the quality of their castings and optimize their production processes.
Post time:ធ្នូ . 11, 2024 09:11
Next:Understanding and Managing Contamination in Foundry Sand for Improved Casting Quality