Understanding the Differences Between Sand Casting and Die Casting
Casting processes are integral to modern manufacturing, allowing for the creation of metal components with complex shapes and sizes. Among the various casting techniques, sand casting and die casting are two of the most commonly used methods. While both serve the primary purpose of shaping metal, they differ significantly in terms of materials, processes, applications, and end results. This article delves into the key differences between sand casting and die casting, helping to highlight their respective advantages and ideal use cases.
1. Casting Process An Overview
Sand casting, as the name suggests, involves forming a mold from sand mixed with other materials. The sand is packed around a pattern that represents the shape of the final product, and then the mold is created by removing the pattern. Once the mold is ready, molten metal is poured into it and allowed to cool and solidify. The mold is then broken apart to retrieve the cast part.
In contrast, die casting utilizes a metal mold (or die) that is pre-made to shape the desired component. This die is typically made of high-strength steel and can withstand the high pressures involved in the casting process. Molten metal is injected into the die under significant pressure, allowing for a high level of detail and precision in the final product.
2. Materials Used
The materials involved in sand casting and die casting also differ significantly. Sand casting can accommodate a wide range of metals, including aluminum, bronze, brass, and iron. The flexibility of sand casting allows for various alloys and composite materials to be used, making it suitable for a diverse set of applications.
Die casting primarily employs non-ferrous metals, with aluminum, zinc, and magnesium being the most common choices. These metals are favored for their excellent casting properties, light weight, and resistance to corrosion. Additionally, the properties of the metals used in die casting enable manufacturers to create parts with thinner walls and tighter tolerances than those typically achievable in sand casting.
The tolerances and surface finishes achieved through sand casting and die casting also show stark differences. Sand casting typically has a rougher surface finish due to the nature of the sand mold. While this can be improved with additional machining processes, the inherent characteristics of the sand can limit the precision of the final product. Tolerances are generally less tight, which means that additional machining may be necessary for parts that require a higher level of precision.
difference between sand casting and die casting
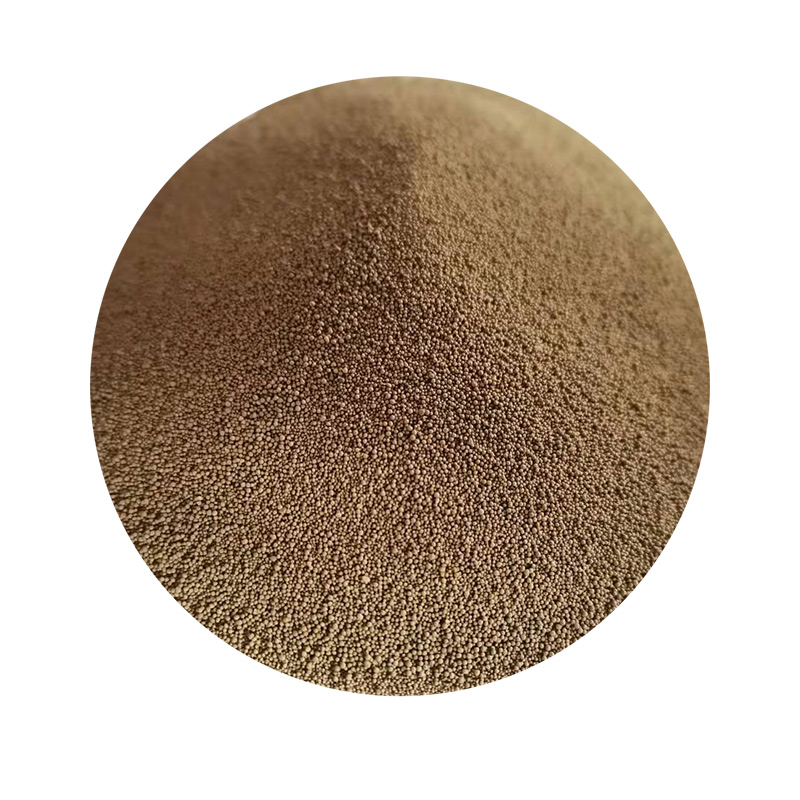
On the other hand, die casting allows for much tighter tolerances and a superior finish. The high-pressure injection of metal into the die results in a smooth surface and highly detailed designs that generally require minimal post-processing. This precision makes die casting especially advantageous for parts that demand exact specifications and aesthetic appeal, such as automotive components, consumer electronics housings, and intricate machinery.
4. Production Rates and Costs
When it comes to production rates and costs, sand casting and die casting exhibit distinct profiles. Sand casting is generally more cost-effective for low to medium production volumes. The initial setup costs are lower since the molds can be created relatively easily and inexpensively. However, the process can be slower, and the overall production rate can decrease for high-volume needs due to longer cooling times and the more labor-intensive processes involved.
Die casting, while more costly in terms of initial setup due to the creation of metal molds and the need for high-pressure machinery, shines in high-volume production scenarios. The speed of the injection process allows manufacturers to produce large quantities of parts in a shorter time frame, making die casting more economical per unit as production scale increases.
5. Applications and Industries
Considering their distinct characteristics, sand casting and die casting find their place in different industries and applications. Sand casting is widely utilized in automotive, aerospace, and art casting industries, where intricate parts or prototypes are necessary. Its ability to work with various metal types also makes it a versatile choice for many manufacturers.
Die casting, with its emphasis on precision and efficiency, is predominantly used for producing components in the automotive industry, electronics, and appliances, where uniformity and detail are paramount.
Conclusion
In summary, both sand casting and die casting play vital roles in the manufacturing landscape, each offering unique advantages based on the specific needs of the project. Understanding the differences between these two methods helps manufacturers choose the right process for their products, balancing factors such as cost, precision, material type, and production volume. As industries continue to evolve, the choice between sand casting and die casting will remain an essential consideration for engineers and manufacturers alike.
Post time:ធ្នូ . 12, 2024 20:49
Next:A Comprehensive Guide to Successful Sand Casting Techniques and Tips