The Difference Between Die Casting and Sand Casting
Casting is a fundamental manufacturing process wherein molten material is poured into a mold to solidify and form intricate shapes and components. Among the various casting techniques available, die casting and sand casting are two widely used methods, each with its unique advantages, applications, and characteristics. Understanding the differences between these two processes is essential for engineers, manufacturers, and designers when selecting the suitable casting method for specific projects.
Overview of Die Casting
Die casting is a high-pressure casting process primarily used for manufacturing metals, with aluminum and zinc being the most common materials. In this method, molten metal is injected into a metal die under high pressure, which allows for a high level of dimensional accuracy and surface finish. The dies are typically made from hardened steel and can be reused many times, making die casting a cost-effective option for high-volume production runs.
The die casting process offers several advantages, such as
1. Precision and Detail Die casting allows for the production of complex shapes with tight tolerances, making it ideal for applications that require intricate designs and parts.
2. High Production Rates The speed at which parts are produced in die casting is significantly higher compared to sand casting, making it suitable for mass production.
3. Excellent Surface Finish The high pressure used in the injection process results in smooth and refined finishes, often reducing the need for extensive post-processing.
4. Material Efficiency Die casting typically generates less waste than other casting methods, as the molten metal is injected directly into the mold with minimal excess material.
However, die casting also has limitations, including higher tooling costs and the inability to use certain metals that have a high melting point.
Overview of Sand Casting
Sand casting, on the other hand, is one of the oldest and most versatile casting methods. It involves creating a mold from a mixture of sand, clay, and water, which is then used to cast parts from various metals. The process starts with the creation of a pattern, which is a replica of the desired component. The pattern is placed in a mold box filled with sand, which is then compacted around it. Once the pattern is removed, molten metal is poured into the cavity to create the final product.
Sand casting has its distinct advantages, including
difference between die casting and sand casting
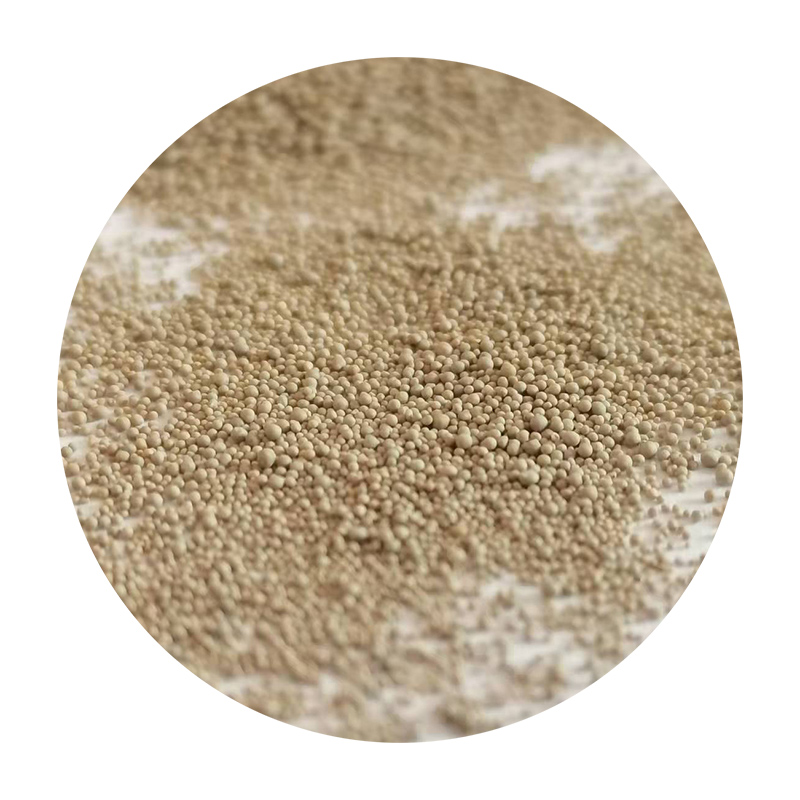
2. Material Versatility Almost any metal that can be melted can be used in sand casting, including cast iron, steel, and aluminum.
3. Lower Tooling Costs The molds used in sand casting are generally less expensive to produce compared to die casting molds, making it a more cost-effective choice for low-volume or one-off production.
4. Easy Pattern Change The design and dimensions of the product can be adjusted relatively easily by changing the pattern, which is advantageous for custom projects.
However, sand casting also has its downsides, such as lower dimensional accuracy and surface finish compared to die casting, requiring additional machining to meet strict tolerances.
Key Differences
When comparing die casting and sand casting, several key differences stand out
- Material Type and Quality Die casting is predominantly used for non-ferrous metals like aluminum and zinc, providing superior surface quality and finish. Sand casting, however, accommodates a wider variety of metals, including ferrous alloys.
- Production Efficiency Die casting is preferred for high-volume production due to its quick cycle times, while sand casting is better suited for low to medium production volumes.
- Cost Implications The high initial tooling costs of die casting may be justified by the long-term savings from high production rates, whereas sand casting benefits from lower setup costs, making it more affordable for limited runs.
- Geometric Complexity Die casting can achieve intricate designs with high precision, unlike sand casting, which, although versatile, generally produces parts that may require additional finishing processes.
In conclusion, the choice between die casting and sand casting depends on various factors, including production volume, material type, design complexity, and cost considerations. Each method has its strengths and weaknesses, making it essential for manufacturers to evaluate their specific requirements before deciding on the appropriate casting technique. Understanding these differences enables better decision-making and optimizes production processes across various industries.
Post time:តុលា . 12, 2024 11:25
Next:sand casting factory