The Sand Casting Process An Overview
Sand casting, a widely utilized metal casting technique, has been a cornerstone in manufacturing for centuries. This process, known for its versatility and cost-effectiveness, is employed to create metal components in various industries, including automotive, aerospace, and construction. The sand casting process involves several key steps pattern making, sand preparation, mold making, pouring, and finishing.
1. Pattern Making
The first step in the sand casting process is the creation of a pattern, which serves as a replica of the final product. Patterns can be made from various materials, such as wood, metal, or plastic, depending on the complexity and volume of the production. The pattern is typically slightly larger than the final product to accommodate the shrinkage that occurs as the metal cools. This pattern also includes cores if internal features are required in the final casting.
2. Sand Preparation
The next stage involves preparing the sand mixture. The primary component of the mold is sand, often mixed with a binding agent, typically clay, and moisture to enhance its cohesiveness. The sand used in the process is usually silica sand, known for its high melting point and thermal stability. Properly prepared sand is crucial for creating molds with the desired surface finish and dimensional accuracy.
3. Mold Making
Once the sand mixture is prepared, the sand is packed around the pattern to form a mold. This is done in two halves, known as the cope and the drag, which can be held together as a complete mold using pins or clamps. The packing technique is critical; it must be tight enough to withstand the weight of the molten metal but not so compressed that it hinders mold removal. After the mold is formed, the pattern is removed, leaving a cavity in the shape of the desired object.
describe sand casting process
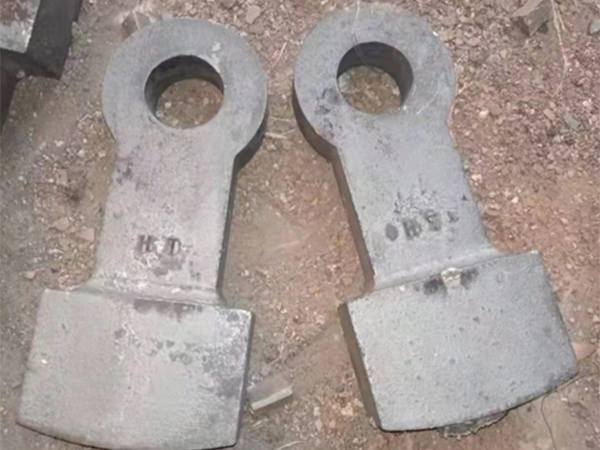
4. Pouring
With the mold ready, it's time for pouring. The metal, typically aluminum, iron, or steel, is melted in a furnace and heated to its required temperature. Once molten, the metal is carefully poured into the mold cavity through a pouring cup and down the sprue. The pouring temperature must be regulated to avoid defects, such as porosity or inclusions. Careful pouring is essential for preventing sand erosion and ensuring that the metal fills the mold completely.
5. Cooling and Finishing
After the mold is filled, the molten metal is allowed to cool and solidify, which typically takes several hours depending on the size and thickness of the casting. Once cooled, the mold is broken apart to reveal the cast metal piece. At this point, excess sand is removed, and the casting is cleaned to eliminate any remnants of sand or metal. Finishing processes such as grinding, machining, and surface treatment may follow to achieve the desired dimensions and surface quality.
Benefits of Sand Casting
One of the most significant advantages of sand casting is its adaptability. It can be used for a wide range of metals and alloys, making it suitable for various applications. Additionally, sand casting is particularly efficient for producing large parts or small production runs, as it does not require expensive tooling compared to other casting methods. Furthermore, the raw materials for sand casting are relatively inexpensive and readily available.
Conclusion
Sand casting remains a vital process in modern manufacturing due to its simplicity, flexibility, and cost-effectiveness. As industries continue to evolve and demand more specialized components, the sand casting process adapts to meet these needs, utilizing advancements in technology and automation. Its rich history and proven reliability ensure that sand casting will continue to play a critical role in the production of high-quality metal components for years to come. Whether for large-scale industrial applications or bespoke manufacturing, the sand casting process stands as a testament to the enduring principles of craftsmanship and innovation.
Post time:ធ្នូ . 19, 2024 23:22
Next:sanding resin 3d prints