Understanding the Components of Sand Casting
Sand casting, a versatile and widely-used manufacturing process, plays a crucial role in creating metal components for various industries. This method involves pouring molten metal into a sand mold, allowing it to solidify and take on the desired shape. With its unique properties and processes, sand casting offers several advantages, making it a preferred choice for producing complex geometries and large quantities of parts. This article will explore the essential components of sand casting, providing insight into how this method works and its significance in manufacturing.
1. Pattern
The pattern is a replica of the final product and serves as a template for the mold. Patterns can be made from various materials, including wood, metal, or plastic, depending on the complexity and size of the final component. The pattern must account for the shrinkage of metal during the cooling process, so it is typically crafted slightly larger than the desired final shape. The pattern is crucial because it determines the accuracy and quality of the finished part.
2. Mold
The mold is created by packing a mixture of sand and a binding agent around the pattern. The sand used in sand casting is often a silica-based material, combined with clay and water to provide cohesion. The mold consists of two halves—the cope (top) and the drag (bottom)—which are clamped together to create a cavity into which the molten metal will be poured. Molds can be designed for single use (in expendable molds) or can be reused multiple times (in permanent molds).
3. Core
Cores are additional components made from sand or metal that are placed inside the mold to create internal cavities or complex features in the final casting. They are essential for producing shapes that cannot be achieved with the outer mold alone. Cores are often held in place within the mold by metal pins or by the weight of the metal itself during casting. After the metal solidifies, the cores are removed to reveal the interior details of the cast part.
components of sand casting
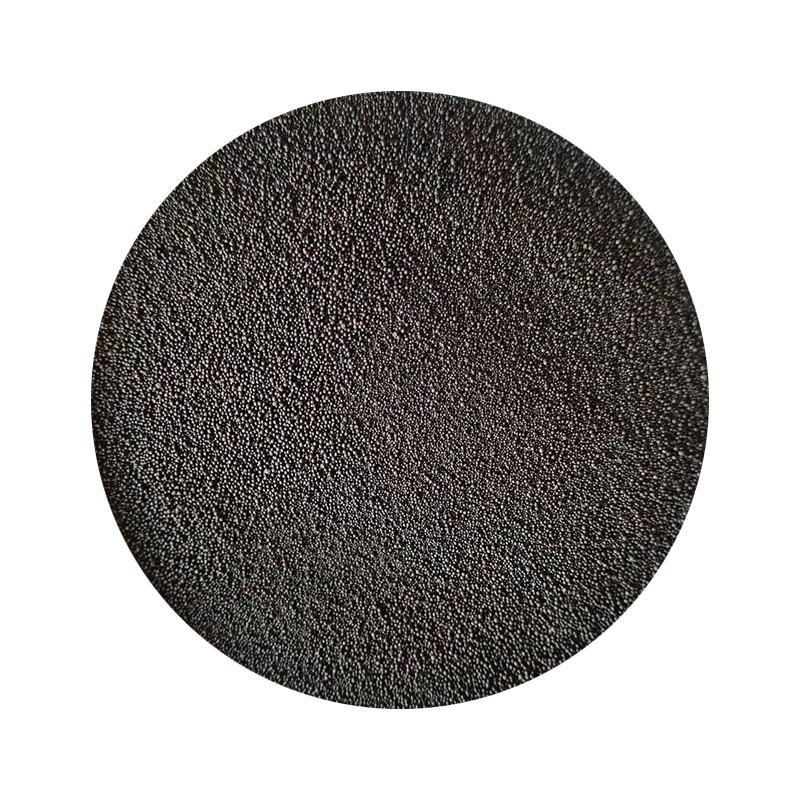
To convert solid metal into a liquid form, a melting furnace is used. Various types of furnaces can be employed, including electric arc furnaces, induction furnaces, and crucible furnaces, depending on the metal type and production scale. The choice of furnace affects the efficiency, cost, and environmental impact of the casting process. The molten metal is poured into the mold at the correct temperature to ensure optimal flow and fill throughout the cavity, minimizing defects in the casting.
5. Pouring System
The pouring system includes channels and gates designed to control the flow of molten metal from the furnace to the mold cavity. This system is crucial for maintaining the temperature of the metal and ensuring that it fills the mold evenly. A well-designed pouring system reduces the likelihood of defects such as air pockets and cold shuts, promoting the overall quality and integrity of the finished product.
6. Finishing Processes
Once the metal has cooled and solidified, the casting is removed from the mold. The finishing processes involve cleaning the casting by removing any sand residues and excess material. Techniques such as sandblasting, machining, or grinding may be employed to achieve the desired surface finish and dimensional accuracy. These final steps are crucial for ensuring that the casting meets the required specifications for its intended application.
Conclusion
Sand casting remains one of the most popular manufacturing processes due to its cost-effectiveness, versatility, and ability to produce complex shapes. Understanding the components of sand casting, from the pattern to the melting furnace and finishing processes, is essential for anyone involved in metalworking or manufacturing. As industries continue to evolve, advancements in sand casting technology will likely enhance its efficiency and capabilities, further cementing its role as a cornerstone of modern manufacturing.
Post time:តុលា . 01, 2024 01:23
Next:रेशमी कास्टिंग बनाने की प्रक्रिया और सुझाव