Understanding Cast Iron Sand Casting
Cast iron sand casting is a traditional manufacturing method that has stood the test of time, widely recognized for its efficiency and versatility. This process involves the use of sand as the primary mold material for shaping molten iron into desired forms. Cast iron, an iron-carbon alloy with a carbon content greater than 2%, offers excellent castability, durability, and wear resistance, making it an ideal material for various applications.
The sand casting process begins with the creation of a pattern, which is a replica of the final object to be produced. Patterns can be made from wood, metal, or plastic, and are designed to withstand the stress of repeated use. Once the pattern is ready, it is placed in a sand mixture, usually composed of silica sand, clay, and water, which binds the particles together. The sand is compacted around the pattern to form a mold cavity.
After the mold is created, the pattern is removed, leaving a hollow impression that mirrors the shape of the desired product. This is known as the mold cavity. Depending on the complexity of the design, the mold may consist of multiple parts. The next step involves the melting of cast iron, which can be achieved using electric arc furnaces, induction furnaces, or cupola furnaces. The molten iron is then poured into the mold cavity, filling it to create the final product.
cast iron sand casting
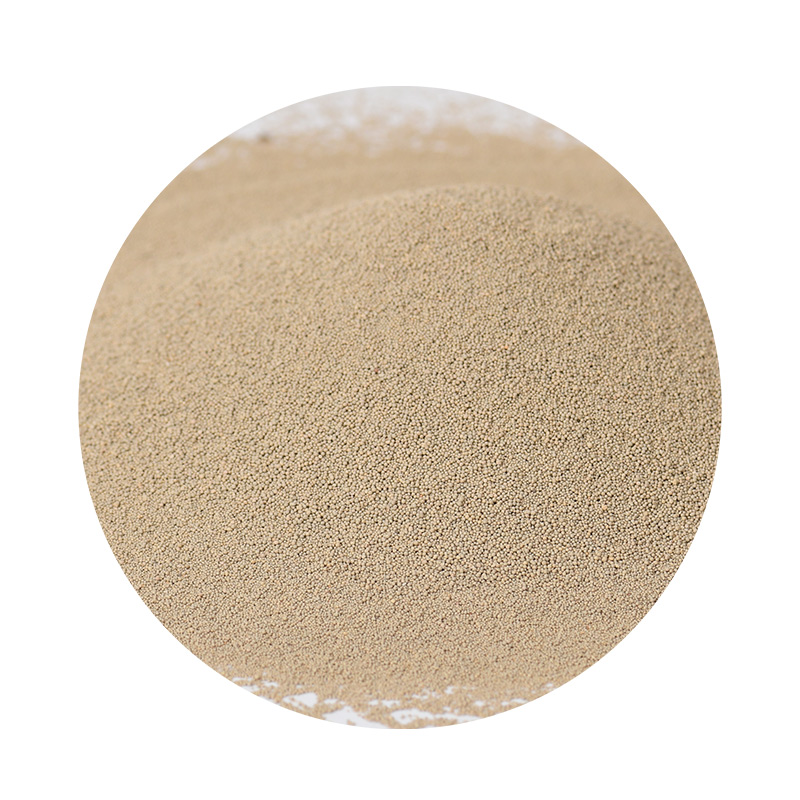
One of the key advantages of sand casting is its ability to produce large and intricate shapes. The flexibility of sand as a molding material allows for the easy production of complex geometries that might be challenging to achieve with other casting methods. Additionally, sand casting can accommodate various sizes, from small components to large industrial parts, making it an essential technique in manufacturing sectors such as automotive, aerospace, and machinery.
Another significant benefit of cast iron sand casting is its cost-effectiveness. The raw materials—sand and iron—are relatively inexpensive, and the sand molds can be reused multiple times. This reduces waste and enhances the overall efficiency of the casting process. Moreover, the sand can be treated and recycled after the casting, further minimizing environmental impact.
However, like any manufacturing process, cast iron sand casting comes with its challenges. Achieving a high level of surface finish can be difficult, often necessitating secondary machining processes to meet strict specifications. Additionally, the cooling rate of cast iron affects its microstructure, which can in turn influence the mechanical properties of the final product. Proper control of the pouring temperature and cooling environment is essential to mitigate defects like shrinkage or porosity.
In conclusion, cast iron sand casting is a highly effective and versatile manufacturing process, combining traditional methods with modern engineering practices. Its ability to produce intricate designs at a relatively low cost makes it an enduring choice within the industry. As technology advances, improvements in materials and techniques promise to enhance the efficiency and quality of sand casting, ensuring its continued relevance in the manufacturing landscape. Whether used for industrial machinery, automotive parts, or artistic sculptures, cast iron sand casting remains a vital process, illustrating the blend of craftsmanship and innovation that defines modern manufacturing.
Post time:តុលា . 13, 2024 07:37
Next:Hiekka-valukohteet ja niiden valmistus hartsilla innovatiivisilla menetelmillä