Understanding Casting Sand Suppliers A Key to Quality Metal Casting
Casting is an integral process in metalworking, allowing manufacturers to create complex shapes and designs. One of the essential ingredients in this process is casting sand, which serves as the mold material for shaping molten metal. Here, we delve into the role of casting sand suppliers, their significance in the industry, and what to consider when choosing one.
What is Casting Sand?
Casting sand is a type of sand used in the foundry industry to create molds for metal casting. It must possess certain characteristics to ensure that it can withstand the high temperatures of molten metal while also allowing for detailed precision in the final product. The most commonly used type of casting sand is silica sand, known for its durability, high melting point, and ease of availability. Other types include zircon sand, chromite sand, and olivine sand, each chosen based on specific casting requirements.
The Role of Casting Sand Suppliers
Casting sand suppliers play a crucial role in the metalcasting industry by providing the essential materials used in the molding process. They source, refine, and distribute various types of casting sands, ensuring that foundries have access to high-quality materials that meet their specific needs. A reliable supplier not only provides quality sand but also ensures timely delivery, which is essential for maintaining production schedules.
Why Quality Matters
The quality of casting sand directly impacts the outcome of metal casting. Poor-quality sand can lead to defects in the final product, such as inclusions, surface defects, and dimensional inaccuracies. For foundries, this can result in increased rework, higher scrap rates, and ultimately, increased costs. Therefore, partnering with a reputable casting sand supplier that prioritizes quality is essential for manufacturers who want to maintain competitive production processes.
Factors to Consider When Choosing a Supplier
casting sand suppliers
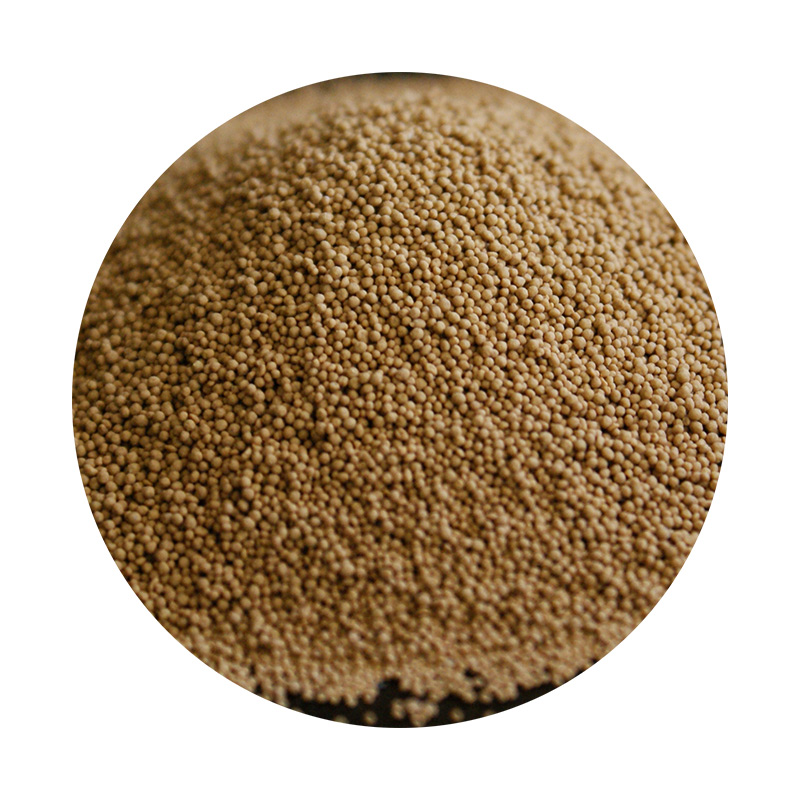
1. Product Quality Look for suppliers that provide consistent quality. This often involves testing the sand for its properties, such as grain size, shape, and thermal conductivity.
2. Range of Products A supplier offering a variety of sand types can cater to different casting needs, whether it be for ferrous or non-ferrous metals.
3. Logistics and Delivery Timeliness is crucial in manufacturing. Evaluate the supplier’s logistics capabilities, including shipping times and their ability to handle bulk orders.
4. Technical Support Suppliers that offer technical assistance can add significant value, helping foundries optimize their processes and choose the right sand for specific projects.
5. Sustainability Practices Increasingly, manufacturers are looking to partner with suppliers who engage in sustainable practices, ensuring that the extraction and delivery of materials have minimal environmental impact.
6. Cost While it's essential to consider cost, it should not be the sole deciding factor. Investing in quality materials often results in better end products, which can lead to cost savings in the long run.
Conclusion
Casting sand suppliers are a pivotal component of the metalcasting industry, directly influencing the quality and efficiency of production processes. By understanding the importance of casting sand and the factors to consider when selecting a supplier, foundries can enhance their production capabilities and maintain high standards of quality. As the industry evolves, forging strong partnerships with reliable suppliers will remain vital for success in the competitive landscape of metal casting.
Post time:វិច្ឆិកា . 12, 2024 07:06
Next:sand casting cost