The Role of Casting Sand in Metal Foundry Processes
Casting is a critical process in metalworking that involves pouring molten metal into a mold to create specific shapes and components. One of the fundamental materials that contribute to the casting process is casting sand, which plays a pivotal role in shaping and defining the characteristics of the final metal product. Understanding the properties, types, and applications of casting sand can greatly enhance the efficiency and quality of metal casting operations.
What is Casting Sand?
Casting sand, primarily composed of silica, is utilized in the creation of molds for casting metals. It provides the essential structure needed to hold molten metal in shape until it cools and solidifies. The sand used in casting is generally a high-quality, fine-grained material that offers the right balance of strength and permeability. This combination allows the molten metal to flow easily into the mold while ensuring that the mold maintains its shape under the pressure of the pouring process.
The effectiveness of casting sand is often gauged through its grain structure, moisture content, and chemical composition. Properly chosen sand can also help to enhance the surface finish of the casting, reduce shrinkage, and minimize defects in the final metal product.
Types of Casting Sand
There are several types of casting sand employed in metal foundries, each offering unique properties that cater to different applications.
1. Green Sand This is one of the most common types of casting sand, a mixture of silica sand, clay, and water. The moisture content in green sand allows it to hold together well, creating sturdy molds. It is primarily used for iron and steel castings and is favored for its ability to produce intricate shapes.
2. Dry Sand Unlike green sand, dry sand lacks moisture. It is typically used in applications that require a more durable mold. Dry sand molds are often more rigid and can withstand higher temperatures, making them suitable for metals with high melting points.
3. Resin Sand This type of sand incorporates synthetic resins as a bonding agent. Resin sand offers higher strength and precision in casting, making it ideal for complex shapes and critical applications. However, it is usually more expensive than traditional sands.
casting sand for metal
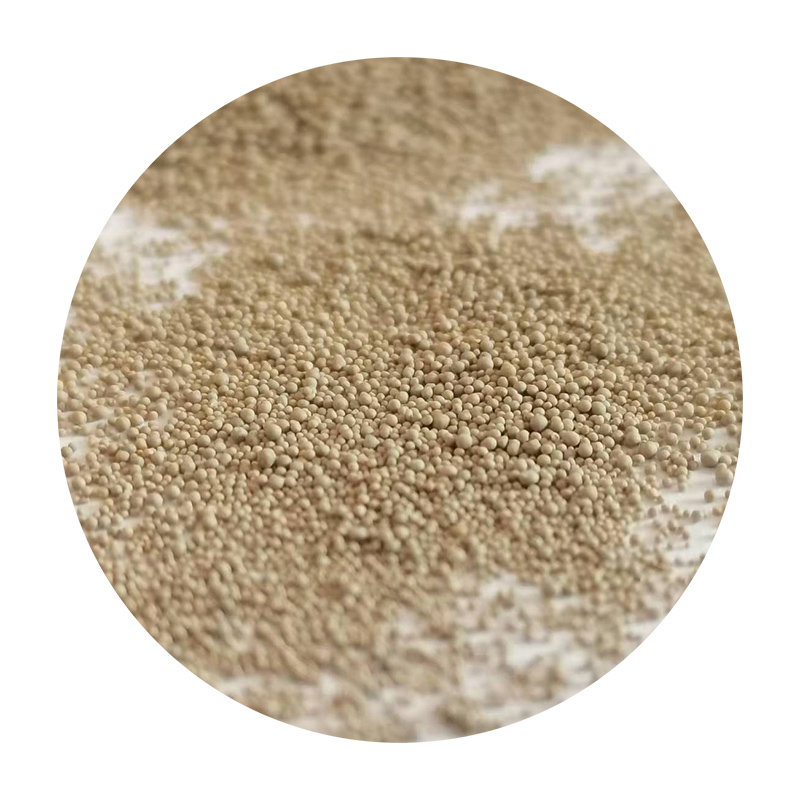
4. Investment Casting Sand For high-precision applications, investment casting uses a fine-grain sand mixed with a binder. This method allows for the production of intricate designs with exceptional surface finishes and dimensional accuracy.
The Importance of Casting Sand Properties
The properties of casting sand are essential in determining the quality of the casting process and the final product. For example, a sand's grain size can significantly affect the mold's ability to capture fine details from the pattern, influencing the overall accuracy and finish of the casting.
Permeability is another crucial property; it allows gases generated during the pouring of metal to escape. Poor permeability can lead to defects such as blowholes or gas inclusions in the final casting.
Moreover, the moisture content in casting sand must be carefully controlled. Excess moisture can cause the sand to stick to the metal, while insufficient moisture can lead to collapse of the mold structure under the weight of the molten metal.
Environmental Considerations
The use of casting sand also raises environmental concerns. Traditional sand casting can produce waste, and the disposal of used sand is a growing issue. However, many foundries are beginning to implement recycling processes for casting sand, reducing waste and promoting sustainability in metal casting. These practices not only help in conserving natural resources but also minimize the ecological footprint of metal casting operations.
Conclusion
Casting sand is a vital element in metal foundries, influencing the efficiency, quality, and cost-effectiveness of the casting process. By understanding the various types of casting sand and their properties, foundries can optimize their processes to produce high-quality metal components. As the industry evolves, innovations in casting sand technology and recycling methods will continue to enhance the sustainability and performance of metal casting practices. This commitment to improvement ensures that casting remains a cornerstone of modern manufacturing, capable of meeting the demands of various industries.
Post time:តុលា . 16, 2024 04:07
Next:sanding block 3d print