The Future of Manufacturing 3D Printing in Sand Casting
In recent years, the manufacturing industry has seen a remarkable transformation, particularly with the introduction of innovative technologies such as 3D printing. Among these advancements, the integration of 3D printing into traditional sand casting processes is revolutionizing the way metal components are produced, offering numerous benefits in efficiency, cost-effectiveness, and design flexibility.
Sand casting has long been a staple in the manufacturing of metal parts, known for its ability to create intricate shapes with high dimensional accuracy. The traditional process involves creating a mold from a pattern, which is typically made from materials like wood or metal. This mold is then filled with molten metal, which hardens into the final component. However, this method often faces limitations in terms of time, material waste, and the ability to produce complex geometries.
The Future of Manufacturing 3D Printing in Sand Casting
One of the most significant advantages of using 3D printing in sand casting is the design freedom it affords. Traditional sand casting techniques often impose constraints on the shapes that can be produced, primarily due to the limitations of pattern making and mold removal. With 3D printing, designers are no longer bound by these limitations. They can create more complex and intricate designs that were previously unfeasible, enabling the production of components with optimized geometries and improved performance characteristics.
3d printing sand casting
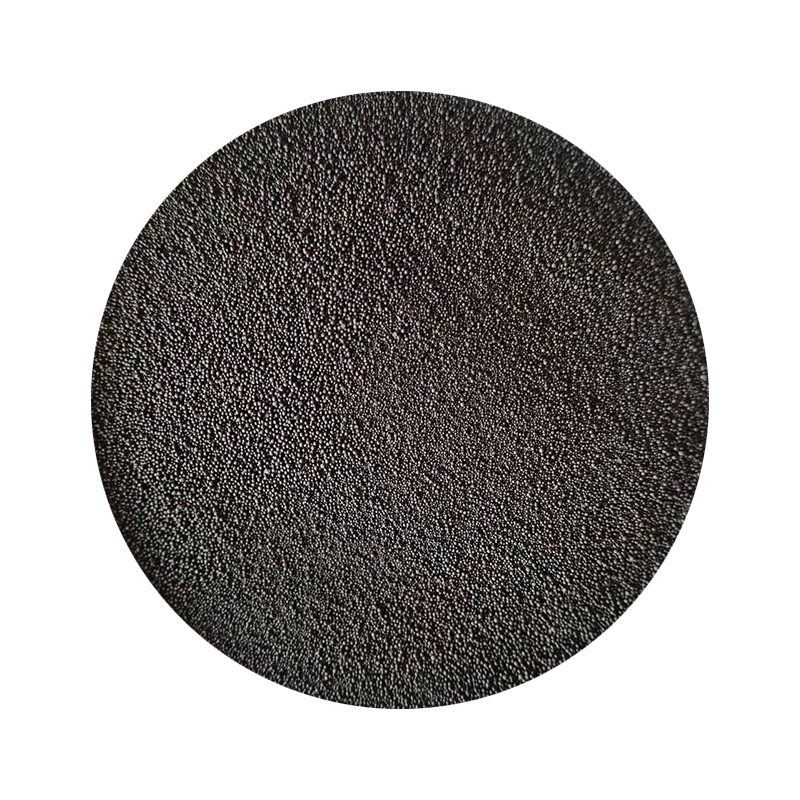
Additionally, the 3D printing process contributes to sustainability in manufacturing. Traditional sand casting processes can be wasteful, generating significant scrap material. However, 3D printing minimizes this waste by producing molds with high precision and reducing the amount of material needed. Moreover, the ability to use recycled sand and other eco-friendly materials in the printing process supports the industry’s shift towards more sustainable practices.
Another remarkable benefit is the reduction in lead times. Because 3D printed molds can be created quickly and tailored to specific needs, manufacturers can respond rapidly to customer demands and market changes. This agility is crucial in industries where time-to-market is a critical factor, such as in aerospace and automotive sectors.
As industries continue to embrace the benefits of 3D printing technology, the future of sand casting looks promising. Companies that adapt to this technology not only gain a competitive edge but also position themselves as leaders in innovation. As research and development in this area progress, we can expect to see even more advanced applications of 3D printed sand casting, further enhancing manufacturing capabilities.
In conclusion, 3D printing in sand casting represents a significant leap forward in manufacturing technology. By merging the traditional methods with cutting-edge advancements, the industry is poised for a revolution that enhances design flexibility, reduces waste, and improves efficiency. As manufacturers continue to explore the potential of this technology, the possibilities for the next generation of products are boundless.
Post time:កញ្ញា . 22, 2024 18:45
Next:casting sand suppliers