The Intersection of 3D Printing and Sand Casting Revolutionizing Manufacturing
In recent years, the manufacturing industry has seen a significant transformation driven by advancements in technology. One of the most innovative developments is the synergy between 3D printing and sand casting, which together promise to optimize processes, enhance design flexibility, and reduce costs. This article explores the integration of these two technologies, highlighting their benefits and implications for various industries.
Understanding the Technologies
3D printing, also known as additive manufacturing, involves creating three-dimensional objects layer by layer from a digital model. This technology allows for complex geometries and intricate designs that are often impossible to achieve with traditional manufacturing methods. On the other hand, sand casting is a conventional technique where molten metal is poured into a mold made from sand to produce metal parts. While sand casting has been around for centuries, it often requires substantial lead times for mold creation and can be limited in design flexibility.
The Synergy of 3D Printing and Sand Casting
The integration of 3D printing into the sand casting process is a game changer. Manufacturers can now use 3D printing technology to create the sand molds themselves. This approach drastically reduces the lead time for mold production, as traditional methods can take days or even weeks to fabricate. By using 3D printers, manufacturers can generate highly precise and intricate molds in a matter of hours.
Furthermore, this confluence allows for the production of complex parts that were once considered too costly or time-consuming to make using standard sand casting techniques. With 3D-printed molds, manufacturers can design components with internal channels, lightweight structures, and other features that optimize performance while minimizing material usage. This capability is particularly beneficial in sectors such as aerospace, automotive, and even art, where precision and complexity drive both functionality and aesthetic appeal.
Cost Efficiency and Sustainability
3d printing sand casting
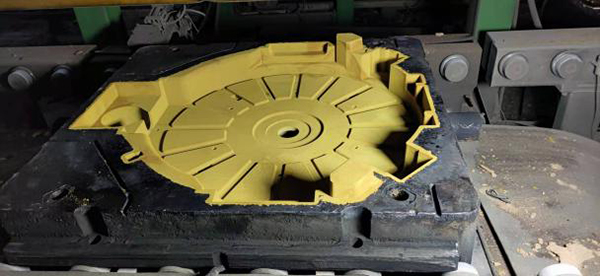
Cost reduction is another significant advantage of combining 3D printing and sand casting. Traditional mold-making processes often involve exorbitant costs, particularly for low-volume production runs. By utilizing 3D printing for molds, companies can minimize material waste and cut down on labor costs associated with mold fabrication. This efficiency translates directly to lower production costs and increased profitability.
Moreover, the sustainability aspect cannot be overlooked. 3D printing enables the use of recycled sand and other eco-friendly materials for creating molds, contributing to reduced environmental impact. As industries increasingly prioritize sustainable practices, this integration offers a pathway to manufacturing that aligns with global initiatives for reducing waste and emissions.
Challenges and Future Prospects
Despite the promising benefits, the integration of 3D printing and sand casting does face challenges. One of the primary concerns is the material compatibility between the 3D-printed molds and the molten metal. Innovators are continuously working on developing new materials and processes to resolve these issues, ensuring the printed molds can withstand the high temperatures and stresses involved in casting.
Looking ahead, the future of this technology combination is bright. As businesses become more aware of the advantages, we can expect greater adoption and further advancements. Researchers and engineers are exploring novel materials for both 3D printing and sand casting that can enhance performance and expand the range of applications. Furthermore, the advent of artificial intelligence and machine learning can optimize designs and predict the most efficient production methods, ensuring continuous improvement in manufacturing processes.
Conclusion
The fusion of 3D printing and sand casting represents a significant milestone in the evolution of manufacturing. By leveraging the strengths of both technologies, industries can achieve unprecedented levels of design freedom, cost efficiency, and sustainability. As more companies embrace this innovative approach, we are likely to witness a profound shift in how products are designed and produced, ultimately leading to faster, cheaper, and more environmentally-friendly manufacturing solutions. The future looks promising, and the possibilities are truly exciting.
Post time:វិច្ឆិកា . 10, 2024 04:41
Next:Essential Components of the Sand Casting Process Explained in Detail