3D Printed Sand Casting Patterns Revolutionizing the Foundry Industry
In recent years, the integration of 3D printing technologies into various manufacturing processes has transformed traditional methods, enhancing efficiency, accuracy, and customization. One of the most promising applications of 3D printing is in the field of sand casting, where intricate patterns are essential for creating high-quality metal components. This article explores the advantages and implications of using 3D printed sand casting patterns, providing insight into how this technology is reshaping the foundry industry.
Understanding Sand Casting
Sand casting is one of the oldest and most versatile manufacturing processes utilized to produce metal parts. The process involves creating a mold by compacting sand around a pattern, which is then removed to leave a cavity. Molten metal is poured into this cavity to form the desired object. Traditional methods of creating patterns often involve time-consuming and cost-intensive processes such as machining or woodworking. However, with the advent of 3D printing, these challenges are increasingly mitigated.
The Advantages of 3D Printing in Sand Casting
1. Rapid Prototyping One of the primary benefits of 3D printing sand casting patterns is the speed of production. Traditional pattern-making can take weeks, but 3D printing can significantly reduce this to a matter of days or even hours. This acceleration enables manufacturers to respond quickly to market demands and design iterations.
2. Cost-Effectiveness While the initial investment in 3D printing technologies can be substantial, the long-term savings are evident. Fewer materials are wasted compared to traditional pattern-making techniques, and the reduction in labor costs associated with manual pattern creation further enhances economic viability. This makes 3D printed patterns particularly appealing for small to medium-sized enterprises.
3. Complex Geometries and Customization 3D printing allows for the creation of complex geometries that would be difficult or impossible to achieve with conventional methods. Whether it's intricate internal channels for cooling systems or lightweight lattice structures, the design freedom provided by 3D printing opens up new avenues for innovation. Furthermore, custom patterns can be easily produced to meet specific client needs without incurring significant additional costs.
3d printed sand casting patterns
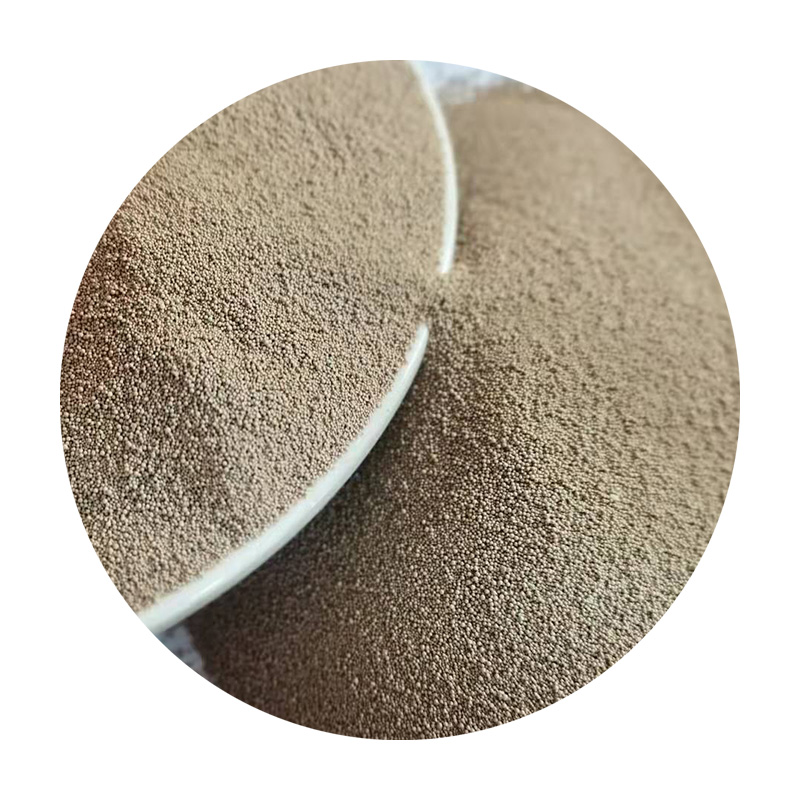
4. Improved Accuracy and Surface Finish The precision offered by 3D printing technologies translates into higher quality molds, resulting in superior final products. Additionally, the surface finish of printed patterns can be optimized to reduce post-processing requirements, further enhancing efficiency.
5. Sustainability and Material Reduction As industries worldwide increasingly focus on sustainability, 3D printing technology contributes by minimizing material waste. The additive nature of 3D printing means that materials are only used where necessary, promoting responsible consumption and reducing the environmental footprint of manufacturing processes.
Applications Across Industries
The advantages of 3D printed sand casting patterns are readily apparent across a multitude of industries. In automotive manufacturing, for example, the ability to swiftly create prototypes allows for rapid testing and development of new components. The aerospace sector benefits from the production of lightweight, complex parts that contribute to fuel efficiency and performance. Additionally, the medical field is leveraging this technology for custom prosthetics and implants, where patient-specific designs can lead to better outcomes.
Challenges to Consider
Despite the numerous benefits, the integration of 3D printing in sand casting is not without its challenges. Material selection poses a significant factor, as the types of sand and binders used must be compatible with the 3D printing process. Additionally, achieving optimal thermal properties in the patterns is crucial, as they must withstand the conditions of molten metal without deforming or failing. As the technology continues to evolve, these challenges will likely be addressed through ongoing research and development.
Conclusion
The adoption of 3D printed sand casting patterns represents a significant leap forward in the foundry industry. With the ability to produce complex, customized designs quickly and cost-effectively, manufacturers are poised to improve their competitive edge. As technology continues to advance, the potential for further innovation in sand casting is limitless, paving the way for a more efficient, sustainable, and precise future in metal manufacturing. As the industry embraces these changes, we can expect to see exciting developments that will shape the next generation of casting processes.
Post time:តុលា . 22, 2024 07:41
Next:Exploring the Properties and Applications of Ceramic Sand in Modern Industries