3D Printing in Sand Casting Revolutionizing Traditional Methods
The manufacturing industry has always been at the forefront of innovation, and one of the most exciting advancements in recent years is the integration of 3D printing technology into traditional sand casting processes. This combination not only enhances efficiency but also improves the overall quality of cast products.
Sand casting has been a staple method for producing metal parts for centuries. The conventional process involves creating a mold from sand and then pouring molten metal into that mold. While this method is well-established, it does have its limitations, including long lead times, the need for skilled labor, and inefficiencies in producing complex geometries. Enter 3D printing—a technology that can reliably address these challenges.
3D Printing in Sand Casting Revolutionizing Traditional Methods
Moreover, 3D printing enables the production of complex geometries that were previously nearly impossible or economically unfeasible with traditional methods. For instance, intricate cooling channels and lightweight lattice structures can be printed directly into the mold. This not only enhances the performance and efficiency of the end product but also minimizes waste material, which is increasingly important in today’s eco-conscious world.
3d print sand casting
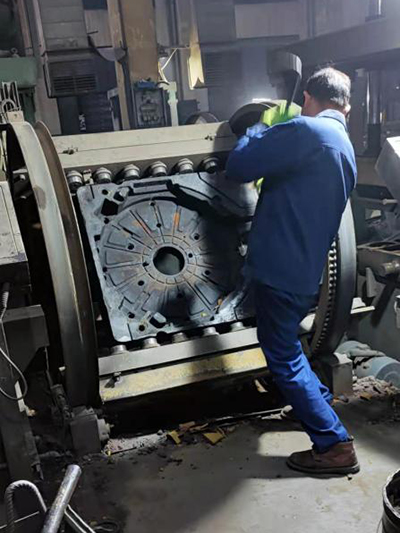
Another significant advantage of combining 3D printing with sand casting is the reduction of material costs. Traditional mold-making methods often require a significant amount of waste material. In contrast, 3D printing allows for more efficient material usage, which cuts down on costs and environmental impact. By utilizing digital designs, manufacturers can optimize the use of sand and reduce the overall material needed for each mold.
The adoption of 3D printing within the sand casting process also serves to democratize manufacturing. Smaller companies can now access sophisticated manufacturing capabilities that were once reserved for larger players with substantial resources. This accessibility promotes innovation and allows for a greater variety of products to enter the market, catering to niche demands.
Despite its advantages, the integration of 3D printing in sand casting is not without challenges. It requires investment in new technologies and a shift in mindset among traditional manufacturers. Training personnel to work with new systems and processes is essential for successful implementation. However, many forward-thinking companies understand that the potential benefits outweigh these initial hurdles.
In conclusion, the fusion of 3D printing and sand casting represents a transformative step forward in the manufacturing landscape. As industries continue to evolve, embracing this innovative approach will not only streamline production but will also lead to unprecedented design freedom and sustainability. Ultimately, combining these two powerful technologies is paving the way for a new era in manufacturing, one that emphasizes efficiency, customization, and environmental responsibility.
Post time:កញ្ញា . 11, 2024 13:43
Next:Golden Sands Prices - Competitive Rates for Your Dream Destination