Sand Casting Materials An Overview
Sand casting, one of the most versatile and widely used manufacturing processes in metalworking, relies heavily on the materials utilized in creating molds and cores. This method allows for the production of complex shapes and large components, making it a favored choice in various industries, from automotive to aerospace. Understanding the materials involved in sand casting is crucial for optimizing the casting process and improving the quality of the final product.
1. Molding Sand
The primary material in sand casting is molding sand, which can vary in composition based on the desired characteristics of the final casting. The most commonly used type of molding sand is silica sand, which is composed primarily of silicon dioxide (SiO2). Silica sand is favored for its high melting point, resistance to thermal shock, and ability to retain shape under heat. However, it is important to add other materials to improve its properties.
2. Binders
To enhance the cohesion of the sand particles, binders are added to the molding sand mixture. The most common binders are clay and synthetic resins. Clay, particularly sodium bentonite, is often mixed with sand in varying percentages to create a mold that can withstand the high temperatures during metal pouring. On the other hand, synthetic resins, such as phenolic and furan resins, are used for their superior strength and ability to cure quickly, allowing for shorter production cycles. The choice of binder can significantly affect the mold's durability, surface finish, and overall casting quality.
3. Additives
sand casting materials
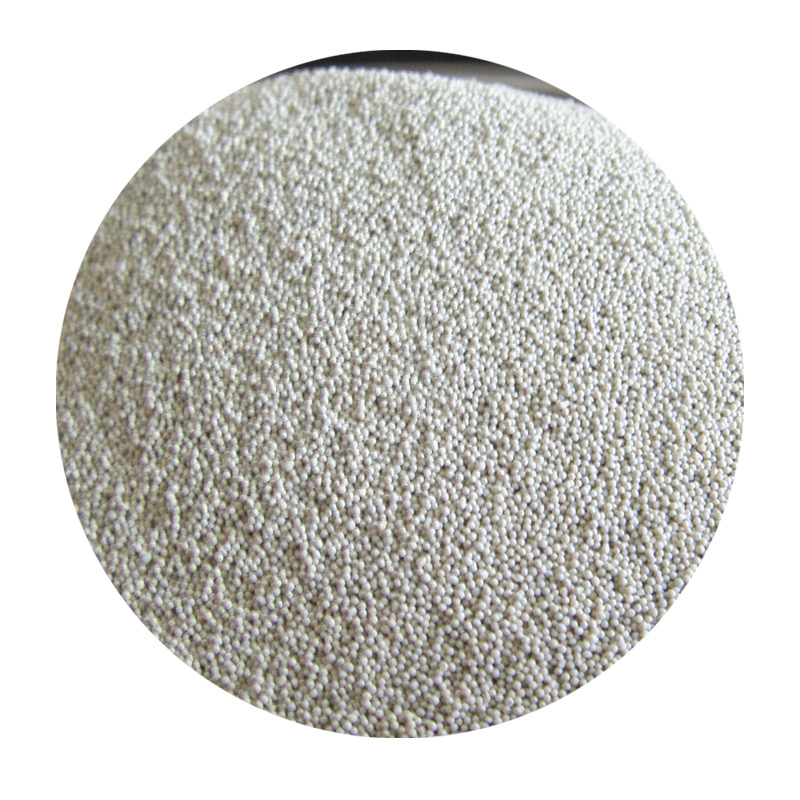
Various additives are incorporated into the sand mixture to improve specific properties. For instance, surfactants can enhance the flowability of the sand, while drying agents and anti-clumping materials can reduce moisture content and improve the mold’s stability. Additionally, colorants may be added for identification and to facilitate the detection of defects during inspection.
4. Core Materials
In sand casting, cores are used to create internal cavities or features in the cast part. Core materials typically include non-refractory sands that are mixed with binders. These core sands are designed to collapse easily after the casting is completed, allowing for the easy removal of the core. Common core materials include oil-bonded sand, which is favored for its high strength and thermal stability.
5. Quality Control
The quality of sand casting materials directly influences the integrity of the finished product. Rigorous quality control measures must be in place to monitor the properties of the sand mixture, including grain size, moisture content, and the effectiveness of binders and additives. Regular sampling and testing ensure that the materials meet the required specifications for the casting process.
Conclusion
In conclusion, the choice of sand casting materials plays a pivotal role in determining the success of the casting operation. Molding sand, binders, additives, and core materials all contribute to the quality and efficiency of the casting process. By carefully selecting and controlling these materials, manufacturers can produce high-quality castings that meet stringent industry standards, thereby enhancing the performance and longevity of the components produced. As the industry evolves, ongoing research and development in sand casting materials will continue to shape the future of manufacturing, leading to improved processes and innovations.
Post time:Қар . 20, 2024 08:48
Next:lost foam casting materials