Understanding Sand Casting of Cast Iron
Sand casting is one of the oldest and most widely used metal casting processes. It involves molding sand around a pattern to create a cavity into which molten metal is poured. Cast iron, a versatile alloy primarily composed of iron, carbon, and silicon, is often the metal of choice for many applications due to its excellent casting characteristics, strength, and wear resistance. This article delves into the intricacies of sand casting cast iron, its benefits, applications, and the overall process involved.
The Sand Casting Process
The sand casting process begins with the creation of a mold. Initially, a pattern, which is a replica of the final product, is made from materials like wood, metal, or plastic. The pattern is placed in a flask, a sturdy frame that holds the sand. The sand mixture, typically composed of silica sand, clay, and water, is packed around the pattern to create a mold. Once the sand is compacted and set, the pattern is removed, leaving a cavity that mirrors the shape of the original pattern.
Next, the mold is prepared for pouring. Sand casting molds can be made in two parts the cope (top half) and the drag (bottom half). After the two halves are joined, holes called risers are added for venting gases and providing a reservoir for molten metal. Once the mold is assembled, molten cast iron is poured into the cavity, filling it completely.
After the metal solidifies and cools, which may take several hours depending on the size and complexity of the casting, the mold is broken apart to reveal the cast iron product. Finally, the casting may undergo processes such as cleaning, machining, and finishing to achieve the desired specifications.
Benefits of Sand Casting Cast Iron
Sand casting offers several advantages when it comes to manufacturing cast iron components. One of the most significant benefits is its cost-effectiveness. The materials used for sand molds are relatively inexpensive and can be reused multiple times, making it an economical option for both small and large production runs.
sand casting cast iron
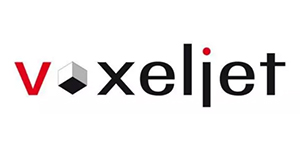
Moreover, sand casting can accommodate a wide range of part sizes and complex geometries. This flexibility is crucial, as cast iron components are often used in various industries, including automotive, construction, and machinery, demanding an array of shapes and sizes. Sand casting is also ideal for producing thicker sections, which is a common requirement for many cast iron applications due to the alloy's heat retention properties.
Additionally, the sand casting process has a relatively short lead time. The ability to rapidly produce molds allows manufacturers to quickly respond to market demands or prototype new designs, an essential factor in today’s fast-paced industrial environment.
Applications of Cast Iron in Sand Casting
Cast iron's unique properties make it suitable for various applications. It is often utilized in the manufacture of engine blocks, pipes, machinery bases, and cookware. The combination of high wear resistance, good machinability, and the ability to absorb vibration makes cast iron components particularly advantageous in machinery and automotive applications.
Another notable application is in the production of sculptures and artistic items, where intricate designs are essential. Moreover, cast iron's ability to withstand high temperatures makes it ideal for cookware such as Dutch ovens and frying pans, favored for their heat retention and even cooking properties.
Conclusion
In summary, sand casting cast iron is a versatile and effective manufacturing process that has stood the test of time. Its cost-effectiveness, adaptability to various designs, and the quality of the final products have solidified its place in various industries. As technology continues to advance, the techniques and materials associated with sand casting may evolve, but the fundamental principles will likely remain pivotal in producing durable and high-quality cast iron components for generations to come. Whether for industrial applications or creative endeavors, sand casting remains a key player in the world of metal fabrication.
Post time:Қар . 10, 2024 13:15
Next:Golden Beach Escape for Ultimate Relaxation and Adventure in Nature's Beauty