The Manufacturing Process of Resin Coated Sand
Resin coated sand has become a critical material in the foundry industry, particularly for manufacturing high-precision castings, owing to its excellent mechanical properties and surface finish. Unlike traditional sand casting methods that rely on natural sand, resin coated sand incorporates a synthetic resin that significantly enhances the sand's compatibility with metal casting processes. This article will explore the steps involved in the manufacturing process of resin coated sand, detailing its preparation, coating application, and curing techniques.
1. Selection of Base Sand
The journey of producing resin coated sand begins with the selection of base sand. Silica sand, being the most popular choice, is preferred for its availability and favorable casting properties. The quality of silica sand is crucial as it affects the final casting's strength and surface texture. The selected sand is screened to achieve uniformity in size and shape, ensuring uniform particle distribution.
2. Preparation of Sand
After selecting and screening, the sand undergoes thorough washing and drying to remove any impurities, moisture, or residual chemicals that could interfere with the coating process. The clean, dry sand ensures a better bond with the resin, which is essential for achieving the desired mechanical properties.
The resin used for coating the sand is typically a phenolic or furan resin, which offers excellent thermal stability and strength. The resin is mixed with a hardening agent and additives that enhance performance characteristics, such as flowability and shelf life. This mixture is then prepared under controlled conditions to ensure consistency in the coating material.
4. Coating Application
resin coated sand manufacturing process
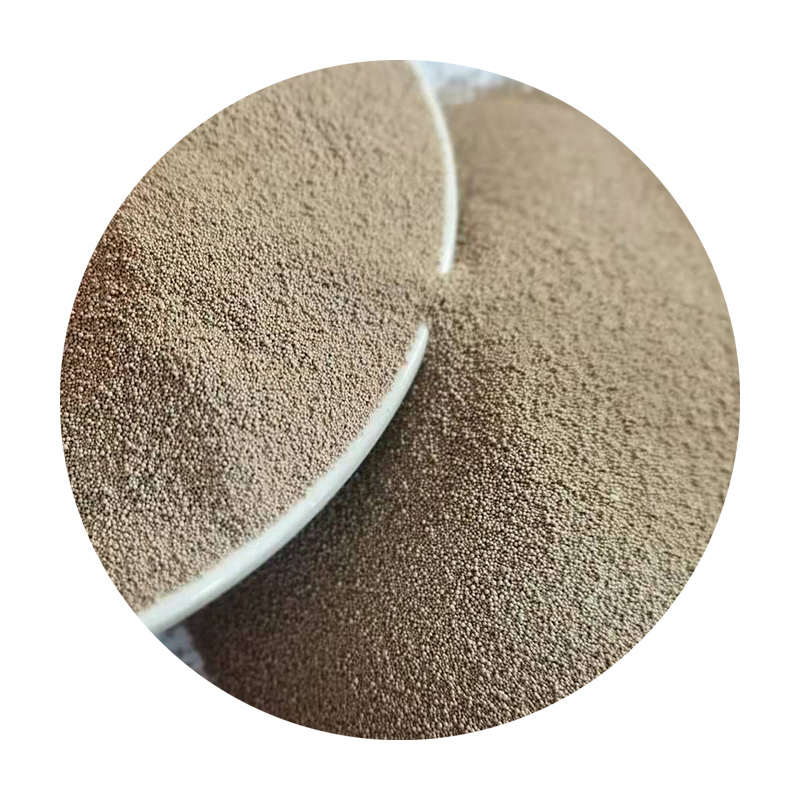
The core step in the manufacturing process is the coating application. The cleaned and dried sand is blended with the prepared resin mixture in a high-quality industrial mixer. This process typically occurs in a controlled environment to minimize contamination and maintain the desired temperature and humidity levels. The mixing must be done uniformly to ensure that each sand particle receives an adequate layer of resin, resulting in a uniform coating.
5. Curing Process
Once the resin-coated sand is prepared, it needs to be cured to harden the resin and ensure proper bonding. This is done by introducing heat, either through an oven or using a hot air process. The curing time and temperature must be carefully controlled, as inadequate curing can lead to poor casting properties, while excessive curing may cause the sand to become too brittle. The duration and temperature are crucial for achieving the optimal characteristics of the sand.
6. Quality Control
As with any manufacturing process, quality control is essential. The resin coated sand is subjected to various tests to evaluate its properties, such as compressive strength, flowability, and thermal stability. Samples are taken from different batches to ensure consistency, and the products need to meet specific industry standards. Any batches that fail to meet the required specifications are reworked or discarded to maintain the quality of the final product.
7. Packaging and Distribution
Once the resin coated sand passes the quality tests, it is cooled and then packaged for distribution. The packaging process also requires careful handling to prevent contamination or damage. The finished product is typically shipped in bulk bags, ensuring that it remains dry and ready for use upon arrival at the foundry.
Conclusion
The manufacturing process of resin coated sand involves a series of meticulously controlled steps from sand selection to packaging. Each step is crucial for ensuring the final product's quality and performance. As the foundry industry continues to evolve, the demand for high-quality resin coated sand is expected to grow, pushing manufacturers to innovate and refine their processes further. Through technology advancements and stringent quality control, resin coated sand remains a cornerstone of modern casting techniques, enabling the production of complex and intricate metal components.
Post time:Қыр . 27, 2024 22:04
Next:Seramik Kum Fiyatları Üzerine Güncel Bilgiler ve Analizler