Understanding Foundry Sand Density Properties and Implications in Metallurgical Processes
Foundry sand, an essential material in the metal casting industry, plays a crucial role in the production of high-quality metal components. The importance of this material extends beyond its basic function as a mold-making substance; one of the most critical properties of foundry sand is its density. Understanding foundry sand density is vital for optimizing its performance and ensuring the success of casting operations.
What is Foundry Sand?
Foundry sand is a high-quality silica sand that is used to form mold cavities for metal casting processes. It is characterized by its angular particles, which provide excellent strength and permeability. The primary types of foundry sand include silica sand, zircon sand, and chromite sand, each possessing unique properties suited for different casting applications. The choice of sand type can significantly influence the resulting metal casting's dimensional accuracy, surface finish, and mechanical properties.
Importance of Density in Foundry Sand
Density is defined as mass per unit volume and is a critical parameter when it comes to foundry sand. The density of foundry sand affects various aspects of the casting process, including mold strength, thermal stability, and the ability to retain its shape under heat. A higher density typically indicates better packing abilities, which can lead to improved mold integrity and reduced likelihood of defects in the cast metal.
1. Mold Strength The density of the sand directly contributes to the strength of the mold. A denser sand mixture can form stronger molds that withstand the high-pressure conditions faced during the metal pouring stage. This is particularly important for complex shapes and intricate designs that are often subjected to thermal stresses.
2. Thermal Conductivity Density influences the thermal properties of foundry sand. Denser sands tend to have better thermal conductivity, which can help in evenly distributing heat during the metal pouring process. This can prevent issues such as hot tearing or uneven cooling, leading to a better quality casting.
3. Permeability While higher density is generally advantageous, it is essential to balance this property with permeability. Permeability is the sand’s ability to allow gases to escape during the pouring process. If a sand is too dense, it may have lower permeability, leading to gas entrapment and defects. Therefore, assessing the right density while ensuring adequate permeability is key to successful casting.
foundry sand density
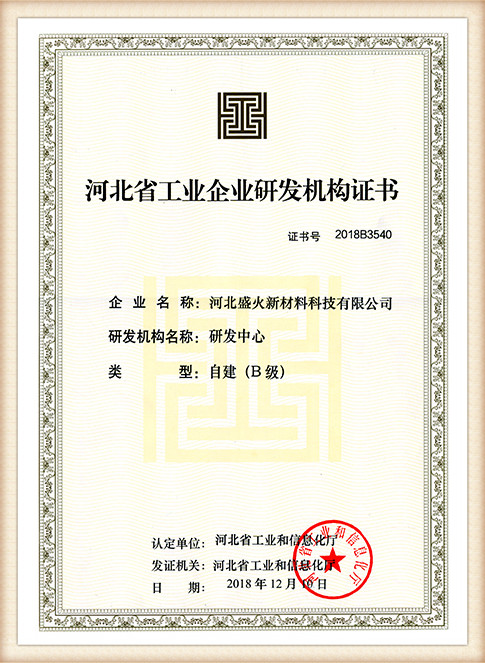
Factors Affecting Foundry Sand Density
Several factors influence the density of foundry sand, including grain size, moisture content, binder type, and compaction level.
- Grain Size The size of the sand particles affects how tightly they can pack together. Finer grains often lead to a denser mix, while coarser grains may create more voids, resulting in lower density.
- Moisture Content The amount of moisture present in foundry sand can alter its density. Excess moisture can lead to swelling of the sand particles and might reduce packing efficiency, thus affecting the overall density.
- Binder Type Many foundry sands are mixed with binders, such as clay or resin, to improve their binding properties. The type and quantity of binder can significantly influence the density and mold strength.
- Compaction The method used to compact the sand before pouring also impacts its density. Proper compaction can maximize density, enhancing the mold's performance.
Conclusion
Foundry sand density is a critical factor in casting processes that impacts mold strength, thermal stability, and permeability. Understanding the intricacies of density and its influencing factors allows foundry engineers to optimize sand mixtures, adjust processing parameters, and ultimately produce high-quality castings. As the metallurgical industry continues to evolve, the importance of refining foundry sand properties, including density, cannot be overstated. Continual research and innovation in sand formulation and processing techniques will further enhance the capabilities of foundry sands, driving improvements in the quality and efficiency of metal casting operations. By focusing on these aspects, manufacturers can not only enhance product quality but also reduce waste and improve overall operational efficiency.
Post time:Жел . 16, 2024 09:36
Next:Addressing Contamination Issues in Foundry Sand for Improved Casting Quality