Facing Sand in Foundry An Essential Component in Metal Casting
In the realm of metallurgy, the foundry industry plays a pivotal role in shaping metal into various components that serve countless applications across different sectors. Among the many techniques employed in metal casting, the use of facing sand is fundamental. This specialized sand layer significantly influences the quality and characteristics of the final casted product, making it a crucial aspect of the foundry process.
What is Facing Sand?
Facing sand is a finely graded sand used to form the surface layer of a mold, directly in contact with the molten metal. It serves several critical purposes it creates a smooth surface finish, improves dimensional accuracy, and enhances the overall aesthetic of the cast product. Typically, facing sand is composed of silica sand, which can be mixed with various additives to improve its properties. These additives may include clay to enhance plasticity or organic materials that help adjust the burning characteristics of the sand during the casting process.
The Role of Facing Sand in Casting
1. Surface Finish The primary function of facing sand is to ensure a high-quality surface finish on the final casting. A smooth and fine-grained facing sand layer results in a more polished surface, reducing the need for excessive post-casting finishing work. This is essential for applications where aesthetics matter, such as in architectural components or consumer products.
2. Thermal Properties Facing sand acts as a thermal barrier, insulating the mold from the intense heat of the molten metal. The right type of sand can withstand high temperatures without breaking down, ensuring that the mold retains its shape and integrity during the casting process. This thermal resistance also allows for better solidification rates, which can improve the mechanical properties of the final product.
3. Moisture Control Maintaining the correct level of moisture in the facing sand is paramount. Properly controlled moisture levels help in achieving better mold hardness and strength, which are critical for withstanding the pressures exerted by molten metal. Too much moisture can lead to defects like gas porosity or surface imperfections, while too little can cause the mold to break during casting.
4. Gas Elimination A well-prepared facing sand can assist in venting gases generated during the melting and cooling processes. Efficient gas escape is crucial to preventing defects such as blowholes, which can significantly compromise the integrity of the cast iron or metal components. The porous nature of facing sand allows for better gas flow, thereby reducing the likelihood of these imperfections.
facing sand in foundry
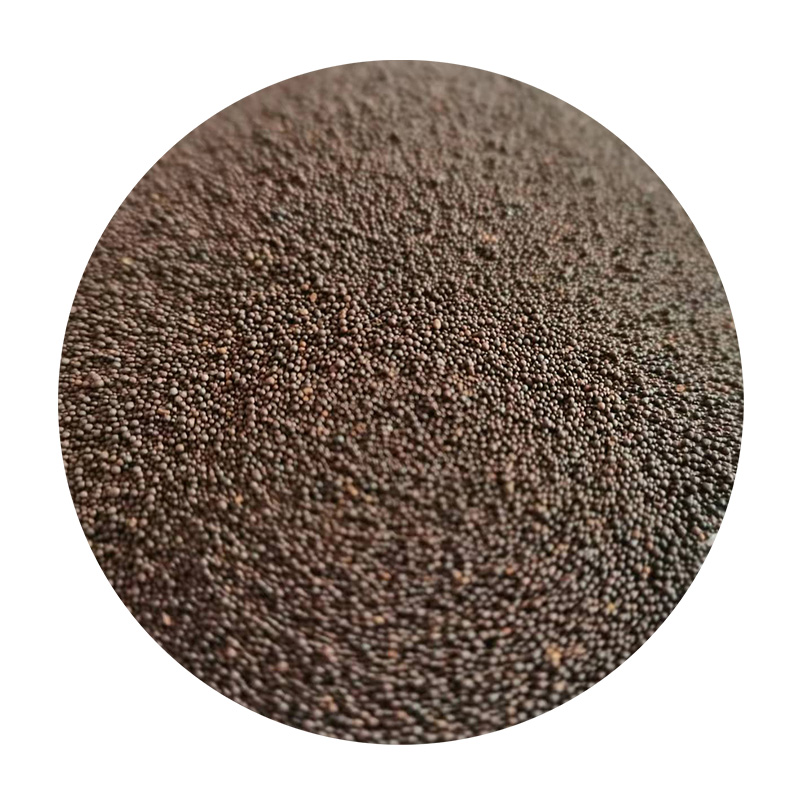
5. Cost-Effectiveness Using high-quality facing sands can also contribute to the cost-effectiveness of the casting process. Investing in the right sand composition can reduce defects and decrease the time and resources spent on finishing processes. Additionally, reduced scrap rates enhance overall productivity and profitability.
Types of Facing Sand
Different foundries may choose specific types of facing sands based on their casting needs. Common types of facing sand include
- Green Sand A mixture of silica sand, clay, and water, green sand is the most commonly used mold material in foundries. It is highly favored for its ability to retain moisture and strength.
- Dry Sand Comprising only sand and additives, dry sand is used when a faster drying time is needed. It is beneficial in mass production scenarios where efficiency is critical.
- Resin-Coated Sand This type of sand is coated with a resin binder that hardens under heat. It offers excellent surface finishes and is suitable for high-precision casting applications.
Conclusion
Facing sand is an indispensable component in the foundry industry, vital for producing high-quality castings with improved surface finishes and structural integrity. The choice and preparation of facing sand directly influence the overall efficiency, quality, and cost of the casting process. As foundry technology continues to evolve, innovations in facing sand formulations and applications will undoubtedly enhance capabilities, ensuring that the foundry industry remains adaptable and competitive in an ever-changing manufacturing landscape.
Post time:Қаз . 06, 2024 23:21
Next:3d sand printing casting