Different Types of Sand Casting
Sand casting is one of the oldest and most widely used casting methods in the manufacturing industry. This process involves creating a mold by compacting sand around a pattern, which is then removed to leave a cavity that closely resembles the final desired shape of the casting. While there are several types of sand casting processes, each tailored to specific needs, they all share a common principle of utilizing sand as a primary molding material. Here are some of the most prevalent types of sand casting techniques.
1. Green Sand Casting
Green sand casting is the most traditional method, where a mixture of sand, clay, and water is used to form the mold. The term green refers to the moisture content in the sand mixture rather than the color. This process is popular due to its cost-effectiveness and the ease of mold creation. The green sand molds are reusable for several cycles, making them a favorable option for large production runs. However, green sand casting may have limitations in producing very intricate designs or fine surface finishes.
As the name suggests, dry sand casting involves using a sand mixture that has been baked or dried to a specific hardness before molding. This technique results in a more robust mold capable of withstanding higher temperatures and producing better surface finishes. Dry sand molds are typically reusable and suitable for larger, more complex parts. However, the initial setup cost is higher compared to green sand casting, making it more suitable for specialized applications.
3. Sodium Silicate Sand Casting
different types of sand casting
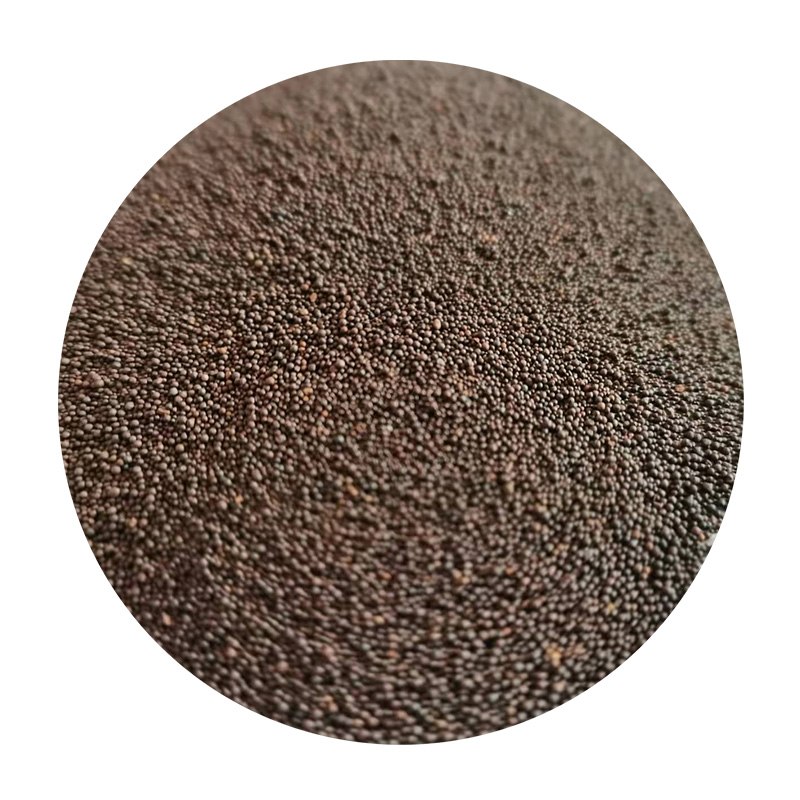
This method employs sodium silicate as a binder in the sand mixture. The process is generally cold, meaning that there is no need for moisture, unlike green sand. Sodium silicate sand casting can create highly detailed molds and is known for its superior dimensional accuracy. It is often used in applications requiring lower thermal conductivity or in cases where intricate patterns are necessary.
4. No-Bake Sand Casting
No-bake sand casting, also known as chemically bonded sand casting, utilizes a chemical binder that hardens when mixed with sand. This process allows for precise mold creation without the need for moisture or heat during the initial setup. One of its primary advantages is the flexibility it offers in terms of mold shape and complexity. This method is often employed in manufacturing intricate parts that demand high precision and exquisite details.
5. Investment Casting
Although not a traditional sand casting process, investment casting often involves a sand core to achieve complex geometries. This technique uses a wax model covered with a ceramic material to form the mold. Once the mold is created, the wax is melted away, leaving a cavity for the molten metal. While not purely sand casting, this process highlights the versatility of sand in various casting applications.
Conclusion
Sand casting remains a critical technique within the manufacturing sector, providing flexibility for producing diverse metal parts. Each type of sand casting encompasses distinct characteristics, making it imperative for engineers and manufacturers to select the appropriate method based on their project's unique requirements. As manufacturing continues to evolve, the fundamental principles of sand casting will undoubtedly remain a foundational element of the industry.
Post time:Қыр . 24, 2024 08:07
Next:Techniques for Effective Wet Sanding on Resin Surfaces for a Smooth Finish