Advantages of Lost Foam Casting
Lost foam casting (LFC) is an innovative manufacturing process that has gained traction in various industries, particularly in producing complex metal parts. This method offers several advantages over traditional casting techniques, making it an appealing option for engineers and manufacturers alike. In this article, we will explore the key benefits of lost foam casting, highlighting why it is a preferred choice for many applications.
1. Complex Geometry
One of the most significant advantages of lost foam casting is its capability to produce intricate shapes and designs that would be challenging, if not impossible, to achieve with traditional casting methods. The foam pattern used in LFC can be easily molded into complex forms, allowing for the creation of detailed geometries. This flexibility enables designers to optimize parts for performance, aesthetics, and functionality, making LFC ideal for industries such as aerospace, automotive, and artistic applications.
2. Reduced Machining Requirements
LFC minimizes the need for post-casting machining operations. The foam pattern is designed to account for shrinkage and other factors, resulting in castings that often require little to no machining. This not only reduces the cost and time associated with secondary operations but also enhances the overall efficiency of the manufacturing process. Reduced machining also minimizes material wastage, making LFC an environmentally friendly option.
3. High-Quality Surface Finish
The surface finish of cast parts produced through lost foam casting is typically superior to that of traditional methods. The foam pattern, when vaporized during the casting process, leaves behind a smooth surface that reduces the need for extensive finishing work. Customers often find that parts produced through LFC require less surface treatment, resulting in lower production costs and a faster turnaround time.
advantages of lost foam casting
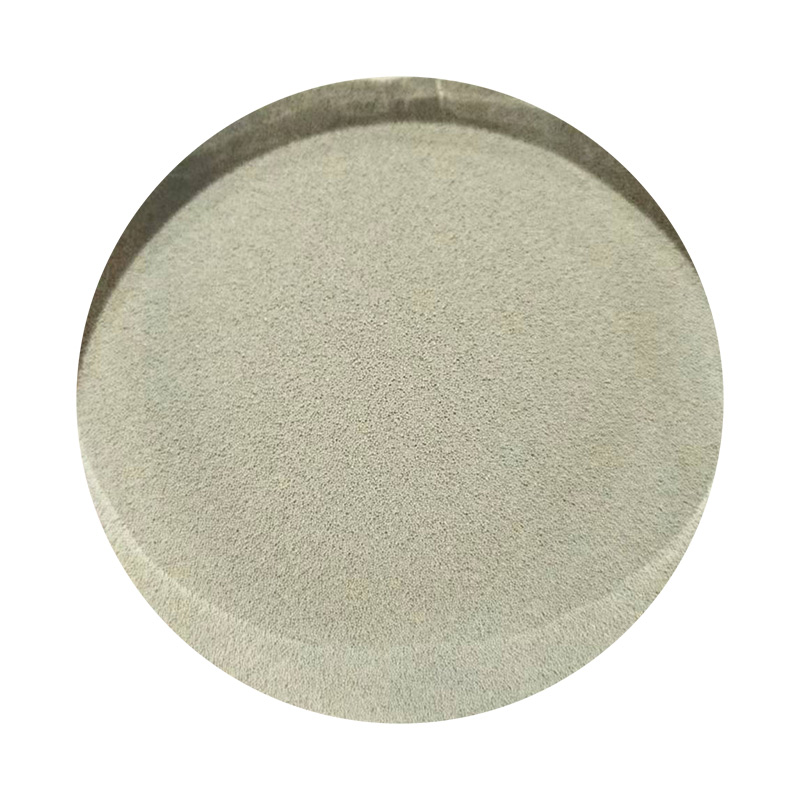
Lost foam casting is compatible with a wide range of metal alloys, including aluminum, iron, and stainless steel. This versatility allows manufacturers to select the most appropriate material for their application, taking into account factors such as strength, weight, and corrosion resistance. Furthermore, LFC can handle both ferrous and non-ferrous metals, expanding its applicability across industries.
5. Environmentally Friendly Process
Lost foam casting is considered a more sustainable manufacturing process compared to conventional methods. The use of a foam pattern eliminates the need for complex tooling, reducing energy consumption and material waste. Additionally, the process generates minimal scrap material, as the foam pattern is fully consumed during casting. Many manufacturers are increasingly prioritizing sustainability, and adopting LFC aligns with these goals.
6. Cost Efficiency
Although the initial setup for lost foam casting may involve some investment in pattern creation, the long-term cost savings can be substantial. The reduction in machining time, lower material waste, and the ability to produce complex parts in a single step lead to overall cost efficiency. Companies can often produce high-quality parts at lower prices compared to traditional casting methods, making LFC an economically viable solution.
7. Improved Dimensional Accuracy
Precision is crucial in manufacturing, and lost foam casting excels in this respect. This method provides better dimensional accuracy than many traditional casting techniques due to the direct conversion of the foam pattern to the final part. The vaporization of the foam creates a near-net-shape casting, which reduces the amount of dimensional deviation typically encountered with other casting processes. This improved accuracy can lead to fewer rejected parts and, consequently, lower production costs.
Conclusion
Lost foam casting represents a significant advancement in casting technology, offering numerous advantages that appeal to a wide range of industries. From the ability to produce complex geometries to reduced machining requirements and improved surface finishes, LFC demonstrates its potential to enhance manufacturing processes. As environmental concerns grow and the demand for high-quality components continues to rise, lost foam casting is likely to become an increasingly popular choice among manufacturers seeking innovative and sustainable solutions. The flexibility, cost efficiency, and precision offered by this casting method make it a valuable tool in the modern manufacturing landscape.
Post time:Жел . 20, 2024 01:41
Next:steps in sand casting