The Emergence of 3D Sand Printing Revolutionizing Manufacturing
In recent years, the manufacturing industry has experienced a seismic shift thanks to the advent of additive manufacturing technologies. Among these innovations, 3D sand printing has emerged as a groundbreaking technique, particularly in the production of intricate sand molds and cores for metal casting. This technology not only enhances productivity but also offers unparalleled design flexibility and sustainability.
Understanding 3D Sand Printing
3D sand printing is a specific form of additive manufacturing that utilizes sand as the primary material to create complex shapes. The process involves a 3D printer that layers fine grains of sand, binding them together using a binding agent. This method allows for the creation of detailed geometries that would be difficult or impossible to achieve with traditional mold-making techniques.
One of the key advantages of 3D sand printing is its ability to produce molds quickly and at a lower cost compared to conventional methods. Traditional mold-making requires the creation of metal or wooden patterns, which can be time-consuming and labor-intensive. With 3D sand printing, manufacturers can generate molds directly from digital files, drastically reducing lead times and labor costs.
Applications in Metal Casting
The primary application of 3D sand printing is in the metal casting industry. Traditionally, foundries have relied on sand molds to shape molten metal. However, these molds are usually created through manual processes, which can result in inconsistencies and a long production cycle. 3D sand printing streamlines this process by allowing foundries to produce custom molds rapidly.
For instance, the automotive industry has embraced 3D sand printing to create engine block molds and complex components. This technology enables manufacturers to design lightweight structures that maintain strength while also optimizing performance. It's not just automotive; aerospace, art, and even medical industries are exploring 3D sand printing for bespoke solutions.
3d sand printing
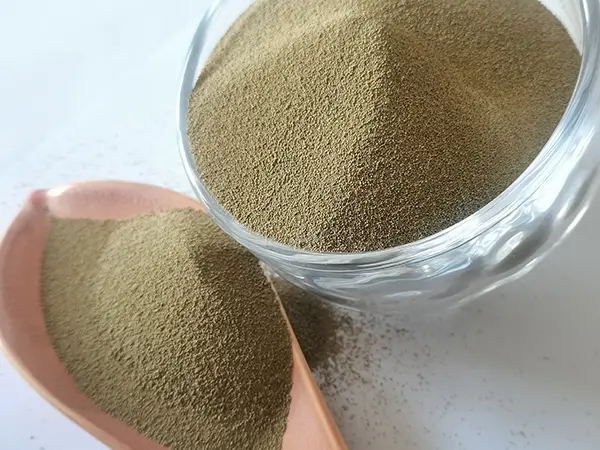
Sustainability Benefits
Another significant advantage of 3D sand printing is its alignment with sustainability goals. Traditional mold-making practices often result in substantial waste, both in material and energy consumption. However, 3D sand printing produces molds with a much higher efficiency, generating minimal waste. Additionally, the used sand can often be recycled and reused, reducing the overall environmental footprint of the manufacturing process.
Future Prospects
As technology continues to evolve, the potential for 3D sand printing seems limitless. Ongoing research and advancements in materials science are likely to expand the capabilities of this technology, enabling even more complex designs and integrating various materials into the printing process. Furthermore, advancements in automation and artificial intelligence could improve the speed and accuracy of 3D sand printing systems, making them even more accessible to manufacturers of all sizes.
The integration of 3D sand printing into traditional manufacturing workflows represents a paradigm shift that combines the best of both worlds the precision of digital design and the age-old practice of casting metal. As industries face increasing pressure to innovate and operate sustainably, 3D sand printing stands out as a viable solution that addresses both challenges.
Conclusion
In conclusion, 3D sand printing is reshaping the landscape of manufacturing by offering increased flexibility, reduced lead times, and significant sustainability benefits. As industries continue to explore this technology, we can expect to see an increase in its adoption and a diversification of its applications. The future of manufacturing looks promising, as 3D sand printing paves the way for more efficient and environmentally friendly production methods.
Post time:Жел . 07, 2024 14:44
Next:golden sands concrete