3D Printed Sand Casting Revolutionizing the Manufacturing Process
In recent years, the manufacturing industry has witnessed significant advancements driven by technology. Among these innovations, 3D printed sand casting has emerged as a groundbreaking technique, transforming traditional casting methodologies. This novel approach combines the efficiency of 3D printing with the versatility of sand casting, thereby paving the way for enhanced productivity, reduced costs, and increased design freedom.
3D Printed Sand Casting Revolutionizing the Manufacturing Process
One of the most significant advantages of 3D printed sand casting is the reduction in lead time. Since molds can be designed and printed in a fraction of the time it would take to create traditional patterns, companies can accelerate their production processes substantially. This rapid prototyping capability enables manufacturers to iterate designs quickly, allowing for faster testing and refinement of products. For industries where time-to-market is crucial, such as aerospace and automotive, this technology offers a distinct competitive edge.
3d printed sand casting
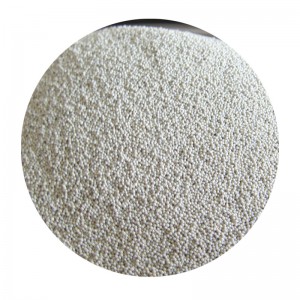
Moreover, the use of 3D printing in sand casting significantly minimizes material waste. Traditional methods often involve excessive material use for the patterns and can lead to additional waste during the machining process. However, with 3D printed sand molds, material is added only where needed, reducing scrap and contributing to more sustainable manufacturing practices. This is particularly important in today's environmentally conscious marketplace, where companies are seeking ways to minimize their carbon footprint.
Additionally, 3D printing provides unparalleled design flexibility. Engineers and designers can experiment with intricate internal structures or lightweight lattice designs that would be impossible to create with traditional casting techniques. This flexibility not only leads to innovative product designs but also allows for optimization of performance, reducing weight while maintaining strength and functionality.
Challenges remain, however, particularly concerning the scalability of this technology. While 3D printed sand casting is already proving effective for small to medium-scale production runs, scaling up for larger production volumes can present logistical and operational hurdles. Furthermore, integrating this technology into existing workflows requires careful consideration of cost, training, and adaptation of current practices.
In conclusion, 3D printed sand casting represents a significant leap forward in manufacturing technology. By streamlining processes, reducing waste, and expanding design possibilities, it holds the potential to reshape the landscape of industries reliant on casting. As the technology matures and evolves, we can anticipate seeing its broader adoption, ultimately leading to more innovative products and sustainable manufacturing practices across various sectors. The future of casting is not only exciting but also indicative of a broader trend towards integration of advanced digital technologies in traditional manufacturing fields.
Post time:Қар . 02, 2024 04:49
Next:types of sand casting process