Types of Sand Used in Foundry
In the foundry industry, sand plays a critical role in the casting process, serving as the primary molding material. The type of sand selected significantly affects the quality, precision, and integrity of the final casted products. Here, we will discuss the various types of sand commonly used in foundries, highlighting their characteristics and applications.
1. Silica Sand
Silica sand, primarily composed of silicon dioxide (SiO₂), is the most commonly used sand in foundry applications. Its high melting point and excellent thermal stability make it ideal for metal casting. When mixed with a bonding agent, silica sand forms a mold that can withstand the high temperatures of molten metals. Additionally, its fine grain size ensures a smooth surface finish on cast products and can be reused multiple times, making it a cost-effective choice for foundries.
2. Green Sand
Green sand is a mixture of silica sand, clay, and water. This type of sand is often used because of its excellent molding properties. The clay component adds binding characteristics that allow the sand to hold its shape during the casting process. Green sand is often used for Iron and steel casting because it provides good surface detail and strength. Its moisture content contributes to a unique chemical reaction when molten metal is poured, which helps in producing high-quality casts.
types of sand used in foundry
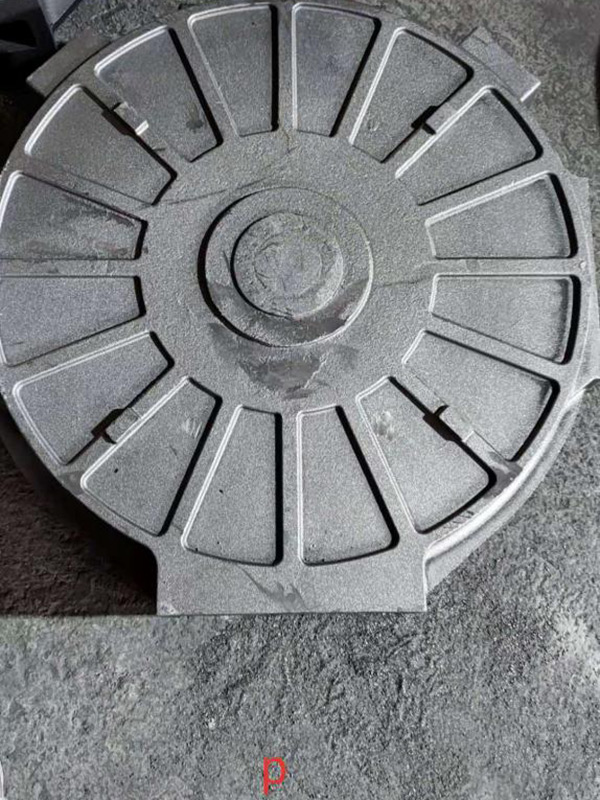
3. Resin-coated Sand
Resin-coated sand is a mix of silica sand coated with a thermosetting resin. This type of sand is known for its superior strength and ability to produce intricate patterns. The resin coating enhances the sand’s durability and reduces the amount of binder needed. Foundries often utilize resin-coated sand for precision casting applications where high dimensional accuracy is required. It is particularly popular for casting non-ferrous metals and in situations demanding exceptional surface finish.
4. Castable Sand
Castable sand, or shell sand, combines sand with a resin and a curing agent. This type of sand can endure significantly higher temperatures than its uncoated counterparts and is used in making shells that form strong, thin-walled molds. Castable sand is ideal for applications requiring thin, intricate parts and provides excellent surface finish as well as high dimensional accuracy.
Conclusion
In conclusion, the choice of sand in foundry applications is crucial for achieving the desired quality of cast products. Silica sand, green sand, resin-coated sand, and castable sand each have unique properties that make them suitable for various types of metal casting. By understanding the strengths and limitations of these different sands, foundries can enhance their production processes, optimize costs, and improve the final product's performance. Proper selection and use of sand in foundries not only affect the efficiency of the casting process but also the overall quality and durability of the cast items.
Post time:ოქტ . 16, 2024 19:48
Next:Innovative Techniques in 3D Sand Printing for Advanced Casting Applications