The Role of Sand in Foundry Operations
Foundries play a crucial role in the manufacturing industry, specializing in the casting of metals to create intricate designs and components necessary for various applications. A fundamental component of the foundry process is sand, which serves as a versatile material for molding and shaping molten metal. This article explores the importance of sand in foundry operations, types of sand used, and the environmental considerations associated with its use.
Types of Sand in Foundries
Foundries primarily utilize two types of sand natural sand and synthetic sand. Natural sand, commonly sourced from riverbeds or beaches, is primarily composed of silica and is known for its thermal stability and strong bonding properties. This type of sand is cost-effective and readily available, making it a popular choice for many foundries.
On the other hand, synthetic sand is engineered from materials that are designed to improve specific characteristics. For instance, clay additives may be incorporated to enhance the sand’s binding properties, while other additives can improve its flowability and reduce moisture retention. The choice between natural and synthetic sand ultimately depends on the desired casting properties and the specific requirements of the metal being cast.
The Molding Process
The role of sand in foundry operations is primarily evident in the molding process. Molding involves creating a cavity in which molten metal is poured to form a solidified shape upon cooling. The sand is mixed with binding agents and water to create a moldable mixture, which is then packed around a pattern that defines the final shape of the casting. Once the mold is formed, the pattern is removed, leaving an impression in the sand. The flexibility of sand allows for the creation of complex shapes and detailed designs, providing foundries with the capability to produce intricate metal components.
Advantages of Using Sand
sand used in foundry
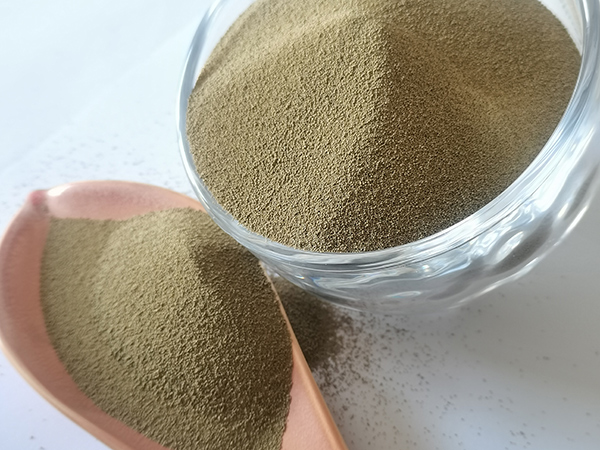
One of the significant advantages of sand in foundries is its high thermal resistance. Sand can withstand extreme temperatures, making it ideal for containing molten metal during the casting process. Additionally, sand molds can be reused, which enhances cost efficiency and reduces waste. The ability to recycle sand is particularly important in today’s manufacturing environment, where sustainability and resource conservation are paramount.
Moreover, sand offers excellent permeability, allowing gases generated during the pouring and cooling process to escape. This property is crucial in preventing defects such as gas porosity, which can severely affect the integrity and quality of the castings.
Environmental Considerations
Despite the benefits of sand in foundry operations, its extraction and use raise environmental concerns. The mining of natural sand can lead to ecosystem degradation, habitat destruction, and increased sediment in waterways. As such, many foundries are exploring sustainable practices that minimize the environmental impact of sand extraction and use.
The recycling of foundry sand has emerged as a viable solution to address these concerns. Used foundry sand, which is collected after the casting process, can be processed and reused for new molding applications, significantly reducing the demand for virgin sand. Additionally, recycled sand can be utilized in the construction industry for applications such as concrete manufacturing and as a base material for roads and pavements.
Conclusion
In conclusion, sand plays an indispensable role in foundry operations, serving as the foundation for molding processes that shape metal into functional and decorative components. With its excellent thermal properties, versatility, and cost-effectiveness, sand remains a key material in casting technology. However, it is essential for foundries to adopt sustainable practices to mitigate the environmental impact associated with sand extraction and usage. Through innovation and responsible management, the foundry industry can ensure that it continues to thrive while protecting the environment for future generations. By balancing economic viability with ecological responsibility, the foundry sector can lead the way in sustainable manufacturing practices.
Post time:ნოე . 27, 2024 16:21
Next:Exploring the Costs of 3D Sand Printers in Today's Market