Sand for Metal Casting A Comprehensive Overview
Metal casting is a crucial process in the manufacturing industry, wherein molten metal is poured into a mold to create various shapes and components. One of the most vital elements of this process is the sand used for mold making. The properties of the sand significantly affect the quality and precision of the final castings. This article delves into the various aspects of sand for metal casting, including types, characteristics, and its overall significance in the casting process.
Types of Sand Used in Metal Casting
The most commonly used sand in metal casting is silica sand, known for its high melting point and excellent thermal stability. Silica sand is favored for its availability and cost-effectiveness. Additionally, there are other types of sand, such as olivine sand, zircon sand, and chromite sand, each possessing unique properties that make them suitable for specific casting applications. Olivine sand, for instance, is non-expansive and resistant to high temperatures, making it an ideal choice for casting ferrous metals. Zircon sand is often used for non-ferrous metals due to its high refractoriness and low thermal expansion.
Characteristics of Quality Casting Sand
High-quality sand for metal casting should possess several essential characteristics. Firstly, it should have a consistent grain size that enables even packing and minimizes defects in the mold. A well-graded sand mixture facilitates better mold strength and surface finish. Secondly, the shape of the sand grains is crucial; round grains tend to flow better and form stronger molds than angular grains. Another important property is the moisture content, as it affects the sand's bonding capability. Properly balanced moisture content aids in achieving the desired mold hardness without leading to defects like sand deformation or erosion.
sand for metal casting
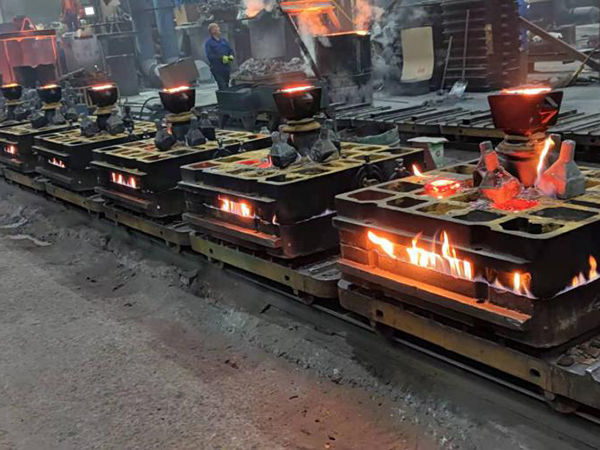
The Importance of Sand in the Casting Process
The choice of sand directly impacts the efficiency and quality of the casting process. A well-prepared sand mold allows for easy and even melting of the metal, thus ensuring dimensional accuracy and a smooth surface finish. Furthermore, the characteristics of the sand significantly influence the thermal behavior during the casting process. For instance, the ability of the sand to withstand high temperatures without breaking down is crucial when casting metals like aluminum and steel.
Environmental considerations are also becoming increasingly important in the metal casting industry. Traditional sand casting processes often make use of synthetic binders and additives, which can pose environmental risks. As a result, there is a growing trend towards the use of more sustainable sand materials and processes that minimize waste and reduce emissions.
Conclusion
In conclusion, sand plays a vital role in the metal casting industry, affecting not only the quality of the final product but also the efficiency of the casting process itself. Understanding the types, characteristics, and importance of casting sand can help manufacturers make informed decisions about material selection and mold preparation. As technology advances, the industry continues to seek innovative solutions to improve sand casting processes, ensuring that they remain sustainable and efficient in the face of increasing demand for high-quality metal products.
Post time:ოქტ . 12, 2024 02:03
Next:Common Materials Employed in the Sand Casting Process for Metal Forming