Understanding Sand Casting A Comprehensive Overview of Sand Types
Sand casting, a time-honored method of metal casting, utilizes sand as a primary molding material. It is renowned for its versatility and cost-effectiveness, making it a popular choice in manufacturing industries for producing intricate metal parts. This article delves into the various types of sand used in sand casting, highlighting their unique properties and applications.
1. Green Sand
Green sand is perhaps the most commonly used type of sand in the casting process. It is composed of silica sand, clay, and moisture. The clay acts as a bonding agent, while the moisture helps to make the mixture pliable. Green sand is favored for its ability to create detailed molds and its relatively low cost. It is often used for producing castings with complex geometries, as it maintains its shape well during the pouring of molten metal. However, the term green refers to the fact that the sand is unbaked and contains moisture, rather than the color of the sand itself.
2. Dry Sand
Dry sand, unlike green sand, has been heated to remove moisture, resulting in a more rigid and durable casting medium. This type of sand is often used in applications where a higher degree of precision is required. It is especially beneficial for creating larger molds that need to retain their shape under higher temperatures and pressures. The absence of moisture also reduces the likelihood of defects related to water steam explosions during the casting process, resulting in a cleaner casting surface.
3. Resin Sand
Resin sand incorporates a bonding agent made from synthetic resins, leading to enhanced mold strength and stability. This type of sand is ideal for high-precision casting applications, especially in the automotive and aerospace industries. Resin sand molds can withstand higher temperatures compared to traditional sands, which allows them to produce intricate designs with excellent surface finishes. Additionally, resin sands can be reclaimed and reused, contributing to a more sustainable manufacturing process.
sand casting sand types
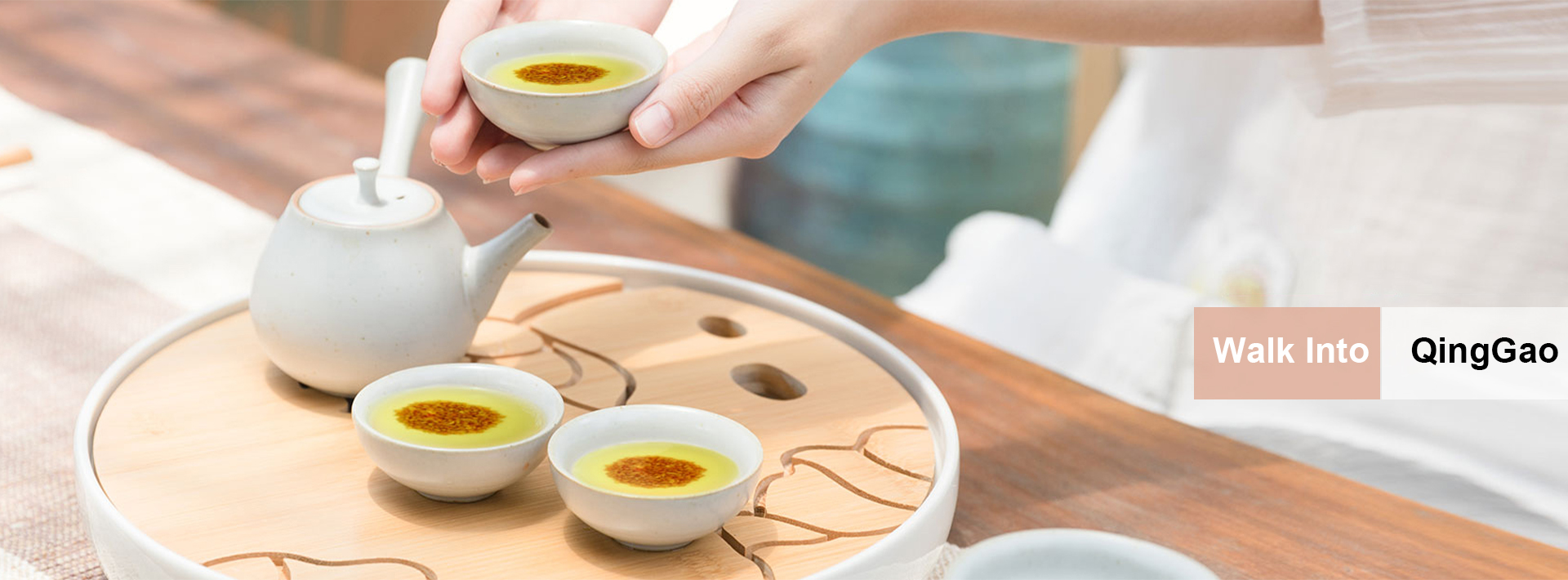
4. Sodium Silicate Sand
Sodium silicate sand is another innovative option for sand casting. It utilizes sodium silicate as a binder, which allows for easy molding and demolding without the need for moisture. This type of sand is particularly advantageous for creating complex shapes and is known for its excellent dimensional accuracy. The use of sodium silicate also reduces air pollution and promotes a cleaner casting environment, aligning with modern environmental standards.
5. Chromite Sand
Chromite sand is a specialized type of sand derived from chromite ore, known for its high thermal conductivity and resistance to high temperatures. It is typically used in the foundry industry for casting ferrous and non-ferrous metals. One of the primary benefits of chromite sand is its ability to withstand oxidation, which improves the lifespan of molds and cores. Although more expensive than conventional sands, chromite sand’s qualities make it an advantageous choice for critical applications requiring exceptional performance.
6. Other Specialty Sands
Beyond the aforementioned types, several specialty sands are employed in niche applications. For instance, zircon sand offers excellent thermal stability and chemical resistance, making it ideal for high-performance casting operations. Similarly, olivine sand possesses good thermal properties and is used when high dimensional accuracy and surface finish are essential.
Conclusion
The selection of sand type in sand casting significantly influences the quality and characteristics of the final casting. Each type of sand—green, dry, resin, sodium silicate, chromite, and specialty sands—has unique properties tailored to specific applications. As industries evolve and seek more efficient, cost-effective, and environmentally friendly solutions, understanding these various sand types becomes crucial for manufacturers and engineers alike. By choosing the right sand, they can optimize the casting process, reduce defects, and ensure the production of high-quality metal components that meet the increasing demands of modern engineering and manufacturing.
Post time:ნოე . 08, 2024 13:05
Next:Analyzing the Importance of Sand in the Sand Casting Process