Sand Casting 101 A Comprehensive Guide to the Basics
Sand casting, one of the oldest and most versatile metal casting processes, has been a cornerstone of manufacturing and engineering for centuries. This method involves creating a sand-based mold into which molten metal is poured, allowing for a wide range of shapes and sizes to be produced. In this article, we will explore the fundamentals of sand casting, including its history, process, advantages, and applications.
A Brief History of Sand Casting
The origins of sand casting can be traced back to ancient civilizations, including the Egyptians and the Chinese, who utilized the technique to create metal objects, tools, and jewelry. The process evolved through the ages, becoming more refined and efficient with the advent of improved materials and technologies. Today, sand casting is widely used across various industries, including automotive, aerospace, and art, for both functional components and decorative items.
The Sand Casting Process
The sand casting process can be broken down into several key steps
1. Pattern Making A pattern, typically made of wood, metal, or plastic, is created to serve as a template for the mold. The pattern is an exact replica of the desired final product, and it must account for factors such as shrinkage and dimensional tolerances.
2. Mold Preparation The sand mold is created by packing sand around the pattern. The sand used in this process is usually a mixture of silica sand, clay, and water, which helps the mold retain its shape. Once the pattern is removed, the two halves of the mold are joined together, resulting in a cavity that mirrors the pattern.
3. Melting Metal The metal to be cast is melted in a furnace. Common metals used in sand casting include aluminum, iron, and bronze. The molten metal must be heated to a specific temperature to ensure proper flow and filling of the mold.
4. Pouring After the metal reaches the desired temperature, it is poured into the mold cavity. This step requires precision to avoid defects such as air bubbles or uneven filling.
5. Cooling and Solidification The molten metal is left to cool and solidify, which typically takes a few hours, depending on the thickness and type of metal used. During this phase, the metal shrinks as it cools, and the mold helps maintain its shape.
sand casting 101
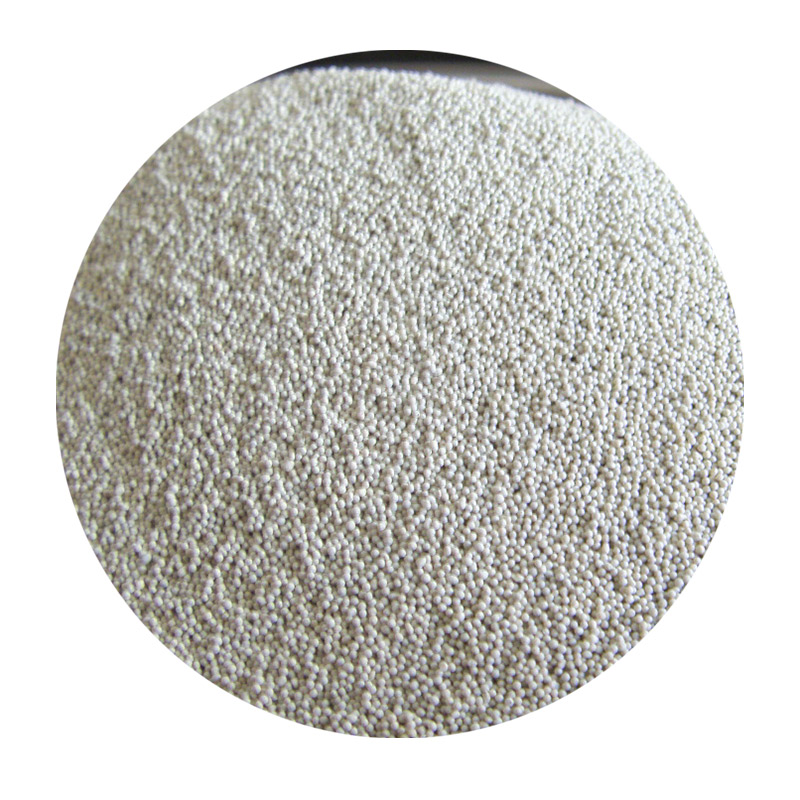
6. Mold Removal Once the metal has solidified, the mold is broken away, revealing the newly created casting. This step may require careful handling to prevent damage to the casting.
7. Finishing The final step involves cleaning the casting to remove any sand residue and imperfections. Additional processes, such as machining or polishing, may be applied to achieve the desired surface finish and dimensional accuracy.
Advantages of Sand Casting
Sand casting offers several significant advantages
- Flexibility This method can accommodate a wide variety of metals and shapes, making it suitable for both small and large production runs. - Cost-Effectiveness The materials used in sand casting, particularly sand, are relatively inexpensive, and the process allows for the production of complex geometries without the need for expensive tooling. - Scalability Sand casting is easily scalable, allowing manufacturers to produce small batches or large quantities as needed. - Low Lead Time Creating a mold and pouring metal can be done quickly, allowing for faster turnaround times in production.
Applications of Sand Casting
Sand casting is employed in numerous applications across various industries. Common uses include
- Automotive Parts Engine blocks, transmission cases, and other critical components are often produced using sand casting techniques. - Aerospace Components Parts like brackets and housings that require high precision and reliability benefit from sand casting. - Art and Sculpture Artists frequently use sand casting to create intricate sculptures and artistic pieces from metal.
Conclusion
In conclusion, sand casting remains a vital process in modern manufacturing due to its versatility, cost-effectiveness, and ability to produce complex shapes. From its rich historical roots to its current applications in diverse industries, understanding the fundamentals of sand casting provides a glimpse into the artistry and ingenuity of metalworking. Whether for industrial components or artistic creations, sand casting continues to play an essential role in shaping our world.
Post time:ოქტ . 01, 2024 18:08
Next:Exploring the Benefits of Unique Sand Casting in Modern Manufacturing Techniques