Understanding Parting Sand in the Foundry Importance and Applications
In the field of metal casting, foundries play a pivotal role in shaping various components that are integral to countless industries. Among the many materials and processes utilized within these foundries, parting sand stands out as a critical component of the molding process. This article delves into the significance, composition, and applications of parting sand in the foundry industry.
What is Parting Sand?
Parting sand, often referred to as parting compound or release agent, is a fine, dry sand that is employed in the molding processes of casting. Its primary function is to facilitate the easy separation of the mold halves once the casting process is completed. Without parting sand, it would be exceedingly difficult to remove the mold from the solidified metal without damaging either the mold or the casting itself.
Parting sand is typically composed of silica or zircon, which have properties that allow for smooth transitions between the mold and the cast material. The choice of parting sand can vary depending on the type of metal being cast and the specific requirements of the foundry.
Importance of Parting Sand
The purpose of parting sand is multifaceted. Firstly, it reduces friction between the mold and the casting, which minimizes the risk of any sticking or tearing during the demolding process. Secondly, it helps to prevent the mold from becoming damaged when the casting is removed. Lastly, parting sand contributes to the overall quality of the casting by ensuring that the surface finish of the casting is preserved and remains free from defects.
Another essential role of parting sand is in the prevention of bonding between the mold and the metal. When molten metal is poured into a mold, it can sometimes bond to the mold surface. Parting sand creates a barrier that mitigates this risk, ensuring a clean release of the casting.
Types of Parting Sand
parting sand in foundry
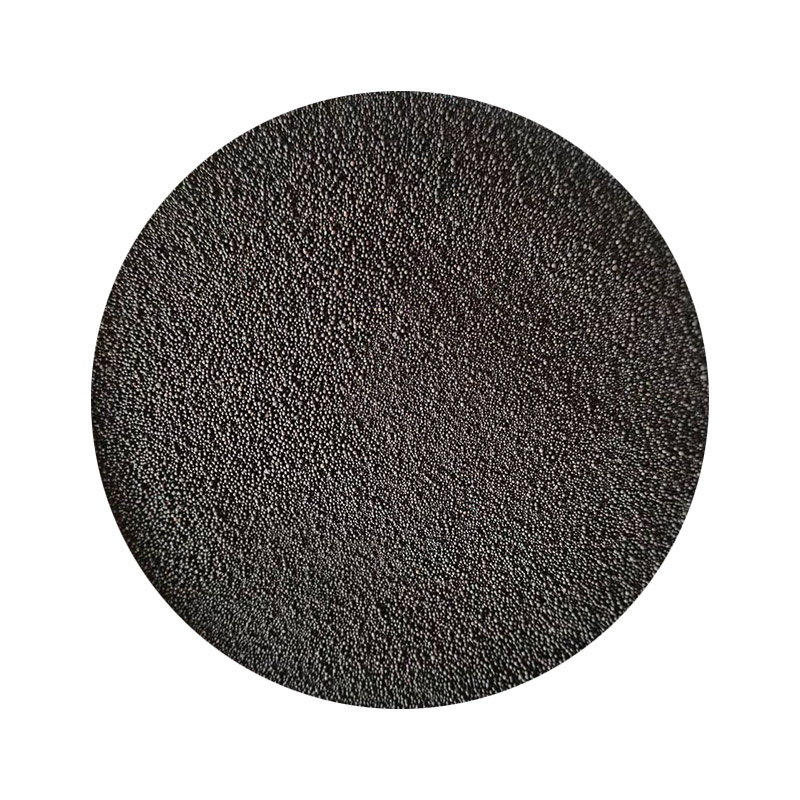
In the foundry industry, various types of parting sands are used, each with unique properties and applications. The most common types include
1. Silica Sand This is the most widely used type of parting sand due to its availability and cost-effectiveness. Silica sand has excellent heat-resistant properties and provides a smooth surface finish. However, it may not be suitable for all metal types, particularly those that have a propensity to react chemically with silica.
2. Zircon Sand Zircon sand is known for its superior thermal stability and is often used for high-temperature applications. While it is more expensive than silica sand, its benefits in specific casting applications, such as steel and aluminum, make it a preferred choice in some foundries.
3. Graphite This is often used as a parting compound due to its lubricating properties. Graphite can help reduce friction even further, which can be advantageous in certain high-precision casting applications.
Applications of Parting Sand in Foundries
The application of parting sand is not limited to just one type of casting process. It is utilized in various casting methods, including sand casting, investment casting, and permanent mold casting. In sand casting, parting sand is crucial as the process involves creating molds from sand mixtures. For investment casting, where molds are often made of ceramic materials, parting compounds can be applied to ease the removal of the investment material.
Additionally, parting sand can enhance the operational efficiency of a foundry. By using effective parting agents, foundries can reduce cycle times, improve casting quality, and minimize defects, which ultimately leads to higher productivity and cost savings.
Conclusion
In conclusion, parting sand is an indispensable material in the foundry industry. Its role in facilitating the casting process, enhancing product quality, and improving operational efficiency cannot be overstated. As the foundry industry continues to evolve, the importance and applications of parting sand will undoubtedly remain a cornerstone of casting technologies, ensuring that manufacturers can produce high-quality metal components with ease and precision.
Post time:ნოე . 10, 2024 18:37
Next:Exploring the Development and Applications of Sand-Based Ceramic Materials in Modern Industries