Understanding the Metal Sand Casting Process
The metal sand casting process is a time-honored manufacturing technique that has been employed for centuries to produce a wide variety of metal components and parts. This process is renowned for its versatility, cost-effectiveness, and the ability to create complex geometries that are often challenging to achieve with other manufacturing methods.
The Basics of Sand Casting
At its core, sand casting involves creating a mold from a mixture of sand and a binding agent. This mold serves as a negative impression of the desired part. The primary materials used in the sand casting process include silica sand, which is the main ingredient for the mold, and a metal alloy, which is poured into the mold to create the final product. The sand is usually mixed with a binder such as clay or resin to enhance its cohesiveness.
The Casting Process
The sand casting process consists of several key steps
1. Pattern Making First, a pattern is created that reflects the final product's shape. This pattern is usually made from materials such as wood, plastic, or metal. Patterns can be either one-piece or multipart, depending on the complexity of the design.
2. Mold Preparation The next step involves preparing the mold. The sand mixture is compacted around the pattern to create a mold cavity. After the mold is formed, the pattern is removed, leaving a cavity that represents the part to be cast.
3. Pouring Once the mold is ready, molten metal is poured into the cavity. The metal is typically heated to a temperature sufficient to ensure complete melting and fluidity, allowing it to flow into intricate details of the mold.
metal sand casting process
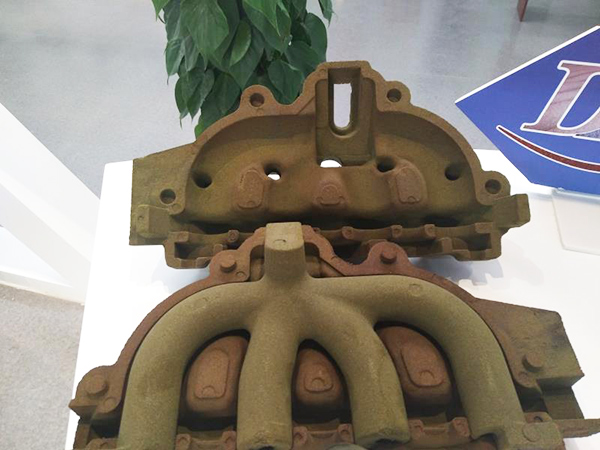
4. Cooling After pouring, the molten metal is allowed to cool and solidify. The cooling time can vary based on the material and the size of the component being cast.
5. Mold Removal Once the metal has cooled and solidified, the sand mold is broken away to reveal the finished casting. This step can include additional processes such as sand reclamation to reuse the sand for future molds.
6. Finishing The final step involves finishing processes, which may include cleaning, grinding, or machining to achieve the desired surface finish and dimensional accuracy.
Advantages of Sand Casting
One of the major advantages of sand casting is its flexibility. It can accommodate a wide range of metals, from ferrous to non-ferrous materials, making it ideal for producing everything from small parts to large components. Additionally, the relatively low cost of materials and simpler tooling requirements compared to other casting methods make sand casting economically attractive, especially for low to medium production runs.
Furthermore, sand casting is known for its ability to produce complex shapes and internal features without the need for extensive machining. This characteristic opens up endless possibilities for designers and engineers, allowing for innovation in product design.
Conclusion
The metal sand casting process remains a pivotal technique in the manufacturing industry. Its rich history, inherent versatility, and cost-effectiveness continue to make it a preferred method for creating intricate metal parts and components. As technology advances, so too does the sand casting process, incorporating new materials and techniques to enhance its capabilities and efficiency in modern production environments.
Post time:სექ . 02, 2024 05:50
Next:Sand Casting Resin - High-Quality Solutions for Precision Metal Casting