Lost Foam Casting Manufacturers An Innovative Approach to Precision Engineering
Lost foam casting (LFC) is an advanced manufacturing process that has revolutionized the way complex metal parts are produced. This technique combines the simplicity of traditional casting methods with modern technology to achieve high precision and efficiency in manufacturing. As industries increasingly demand intricate designs and tighter tolerances, lost foam casting manufacturers have emerged as key players in the metalworking landscape.
The core principle behind lost foam casting is relatively straightforward a foam pattern is created to form the shape of the desired metal part. This foam pattern is coated with a refractory material to withstand the pouring of molten metal. Once the metal is poured, the foam evaporates, leaving behind a hollow mold that has the exact shape of the original pattern. This process offers several significant advantages over traditional casting methods.
One of the most notable benefits of lost foam casting is its ability to produce complex shapes with high accuracy. Manufacturers can create intricate designs that would be difficult or impossible to achieve using other methods. This capability is particularly valuable in industries such as aerospace, automotive, and industrial machinery, where components often have intricate geometries and must meet rigorous performance standards.
Moreover, lost foam casting reduces the need for machining operations. Since the casting process allows for a high level of detail and smooth surface finishes, many parts can be produced with minimal post-processing. This not only saves time and costs but also minimizes material waste, making it an environmentally friendly option compared to traditional machining processes.
lost foam casting manufacturers
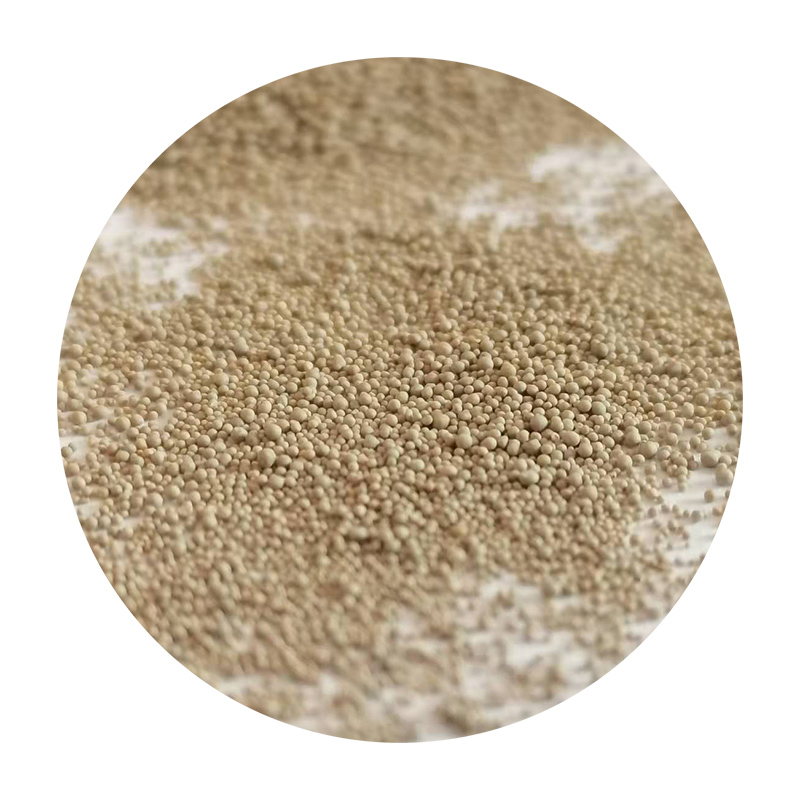
Cost efficiency is another significant advantage of lost foam casting. The process generally requires less labor and shorter production cycles, making it an attractive option for manufacturers looking to optimize their operations. Additionally, the ability to produce short runs of complex parts without the need for expensive tooling means that lost foam casting is ideal for prototyping and small batch production.
In recent years, the demand for lost foam casting has surged, prompting a growing number of manufacturers to adopt this innovative process. These companies typically invest in advanced technology and equipment to ensure high-quality output. Additionally, many lost foam casting manufacturers focus on continuous improvement and innovation to meet the evolving needs of their clients.
However, it is essential for manufacturers to choose a reputable lost foam casting supplier. Factors to consider include the manufacturer's experience in the industry, their ability to work with various materials, and their commitment to quality control. Collaborating with an established manufacturer can significantly impact the success of a project, as they will have the expertise to navigate challenges and deliver the desired results.
In conclusion, lost foam casting represents a transformative approach to metal part manufacturing, enabling the production of complex, high-precision components with reduced lead times and costs. As more manufacturers adopt this innovative technique, they enhance their competitiveness and ability to meet the rigorous demands of modern industries. With a focus on quality, efficiency, and environmental sustainability, lost foam casting is poised to play a significant role in the future of manufacturing.
Post time:სექ . 28, 2024 07:33
Next:砂の科学と3D技術の未来を探る