Lost Foam Casting Coating An Essential Component for Precision Casting
Lost foam casting is an innovative manufacturing process widely utilized for producing complex metal parts with high precision and intricate details. One of the key components that greatly influences the efficiency and quality of lost foam casting is the coating applied to the foam patterns. This article delves into the importance of lost foam casting coating, its applications, advantages, and the factors that affect its performance.
What is Lost Foam Casting?
Lost foam casting is a method that involves the use of a foam pattern to create a mold for metal casting. The foam pattern is coated with a material that serves as a barrier between the foam and the metal. Once the mold is created, molten metal is poured into it, vaporizing the foam in the process and leaving behind a solid metal part that matches the shape of the original foam pattern. This technique is particularly favorable for industries requiring high-quality castings, such as automotive, aerospace, and art.
The Role of Coating in Lost Foam Casting
The coating used in lost foam casting plays a critical role in ensuring the success of the casting process. The primary functions of the coating are to
1. Provide a Barrier The coating acts as a thermal and chemical barrier, preventing the molten metal from reacting with the foam and ensuring that the final product retains its desired specifications. 2. Enhance Surface Quality A well-applied coating improves the surface finish of the casting by preventing defects such as sand inclusion, burn-on, and other surface imperfections.
3. Control Heat Transfer The coating regulates the heat transfer during casting, which is essential for achieving the correct metallurgical properties in the final product.
4. Facilitate Mold Recovery The coating aids in the rapid vaporization of the foam pattern, facilitating a smoother and more efficient mold recovery process.
Types of Coatings
Lost foam casting coatings can vary based on the desired characteristics and application requirements
. Some commonly used coatings includelost foam casting coating
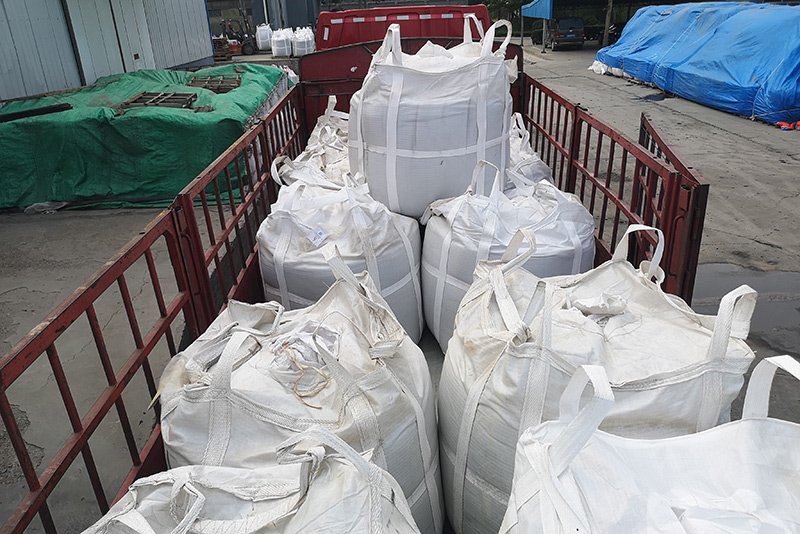
- Ceramic Coatings These provide excellent thermal resistance and are known for their durability and ability to handle high temperatures.
- Polymer-based Coatings These coatings are generally easier to apply and can provide a smooth finish, but their temperature tolerance may not match that of ceramic coatings.
- Refractory Coatings Typically composed of materials that can withstand high temperatures, refractory coatings enhance mold integrity and protect against metal erosion.
Factors Affecting Coating Performance
Several factors can influence the effectiveness of lost foam casting coatings
1. Thickness The thickness of the coating layer can impact the outcome of the casting. A fine balance must be struck, as too thick a coating might delay foam vaporization, while too thin a layer could result in defects.
2. Application Method How the coating is applied—whether by spraying, dipping, or brushing—affects the uniformity of the layer and, consequently, the casting quality.
3. Curing Conditions The conditions under which the coating cures, including temperature and humidity, play a critical role in the properties of the final coating.
4. Material Compatibility The compatibility of the coating material with the foam pattern and the molten metal being used is crucial for achieving optimal results.
Conclusion
Lost foam casting is a sophisticated technique that offers numerous benefits in precision manufacturing. The coating applied to the foam pattern is a fundamental element in this process, significantly influencing the quality, efficiency, and integrity of the final product. By understanding the role and requirements of coatings in lost foam casting, manufacturers can optimize their casting processes, ensuring high-quality outputs that meet the demanding standards of modern industries. With continual advancements in coating technology, the future of lost foam casting looks promising, paving the way for even more intricate and precise manufacturing capabilities.
Post time:ოქტ . 13, 2024 04:48
Next:3d sand printing process