High-Quality Sand Casting An Insight into the Process and Benefits
Sand casting is one of the oldest and most versatile methods of metal casting. It is widely used in various industries to create parts and components of all sizes and complexities. High-quality sand casting is crucial for producing durable and precise metallurgical parts. In this article, we will explore the essentials of high-quality sand casting, including its process, materials, applications, and benefits.
The Sand Casting Process
The process of sand casting begins with the creation of patterns, which are replicas of the final product. These patterns are typically made from materials such as wood, metal, or plastic and can be either single-use or reusable. Once the pattern is ready, it is placed in a molding box and sand is packed around it to create a mold.
The primary material used for sand casting is silica sand, which provides excellent thermal stability and permeability. For high-quality outcomes, the sand is often mixed with a binding agent, such as clay, which helps maintain the mold’s shape. The molding sand must have the right mixture of fine and coarse grains to ensure it can withstand the molten metal's pour.
Once the mold is prepared, it is filled with molten metal, typically aluminum, iron, or bronze. After the metal solidifies, the mold is broken away to reveal the cast part. The final step involves cleaning the cast part to remove any sand residues and excess material, a process known as finishing.
Key Elements of High-Quality Sand Casting
1. Material Quality The quality and type of sand used significantly influence the final product's integrity. The ideal sand should have the right grain size, shape, and distribution to produce strong molds that accurately capture details.
2. Pattern Design Precision in pattern design is vital for achieving high-quality casts. The pattern needs to account for shrinkage and thermal expansion to ensure that the final product meets the required specifications.
3. Controlled Pouring The temperature and speed of pouring the molten metal into the mold are critical. Slow and controlled pouring minimizes turbulence that can lead to defects, such as air pockets or inclusions.
4. Temperature Management Proper temperature management during both the pouring and cooling stages is essential. Too hot or too cold can lead to irregularities in the metal structure, affecting the overall quality.
high quality sand casting
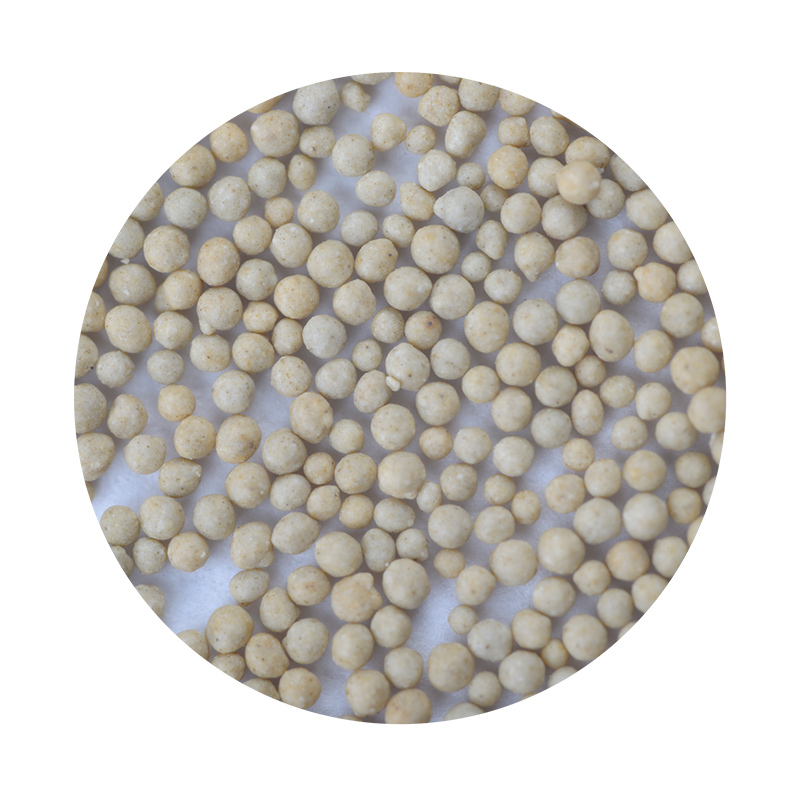
5. Post-Casting Treatments After casting, various treatments such as heat treatment, surface finishing, or machining can be employed to enhance the mechanical properties of the cast, ensuring it meets industry standards.
Applications of High-Quality Sand Casting
High-quality sand casting is employed in numerous industries, including automotive, aerospace, and consumer goods. It is particularly valuable for manufacturing engine blocks, gears, frames, and intricate components that require high strength and durability.
In the automotive industry, sand casting is used to produce lightweight yet strong components that improve fuel efficiency. Aerospace applications benefit from the ability to create components that withstand extreme environments while maintaining low weight. The versatility of sand casting also allows for rapid prototyping and the production of customized parts on demand.
Benefits of High-Quality Sand Casting
1. Cost-Effectiveness Sand casting is relatively inexpensive compared to other casting methods, especially for low to medium-volume production runs. The materials and processes involved are generally less costly.
2. Design Flexibility This method allows for complex designs and shapes that may be challenging to produce using other techniques. It enables intricate detail and precision in the final product.
3. Material Choices A wide range of metals can be cast using sand casting, providing manufacturers with the flexibility to select materials that best suit their application needs.
4. Environmentally Friendly Sand used in casting can be recycled and reused, minimizing waste and environmental impact.
Conclusion
High-quality sand casting remains a fundamental process in metalworking, appreciated for its versatility, cost-effectiveness, and ability to produce intricate parts. By focusing on material quality, precise pattern design, and careful handling, manufacturers can achieve superior results that meet today’s demanding standards across various industries. With ongoing advancements in technology and techniques, the future of sand casting looks promising, catering to the evolving needs of modern manufacturing.
Post time:ოქტ . 20, 2024 15:32
Next:super sand g2