Understanding Foundry Sand Density A Key Factor in Metal Casting
Foundry sand plays a crucial role in the metal casting industry, serving as the primary material for molding and shaping metal into various forms. One of the most significant properties of foundry sand is its density, which greatly influences the casting process and the quality of the final product. In this article, we will explore the importance of foundry sand density, factors affecting it, and its implications for casting processes.
What is Foundry Sand?
Foundry sand is a high-quality silica sand that is specially processed to be used in the casting of metals. It is designed to withstand high temperatures and harsh conditions in the foundry environment. The sand is coated with a binding agent, which helps to hold the mold together during the casting process. A majority of foundry sands are classified as silica sand, but variations such as olivine sand, zircon sand, and chromite sand are also used depending on the specific casting requirements.
The Importance of Density
The density of foundry sand refers to its mass per unit volume and is a critical parameter in the casting process. This property affects the sand's ability to retain shape and support the weight of the molten metal, ensuring that the final casting is accurate and defect-free. A higher density generally means that the sand has less porosity, which can lead to fewer defects and a smoother surface finish on the metal product.
Moreover, the density of the sand influences its thermal conductivity. Denser sands typically have better thermal properties, which is advantageous when dealing with high-temperature molten metals. This ensures that the heat is distributed evenly throughout the mold cavity, enhancing the casting's integrity.
Factors Affecting Foundry Sand Density
Several factors can influence the density of foundry sand
foundry sand density
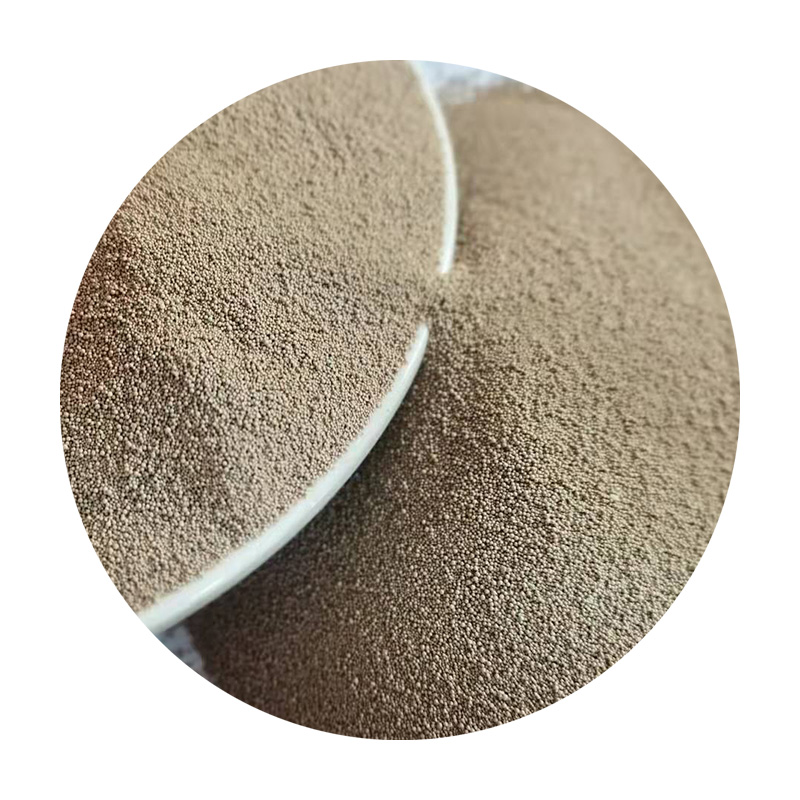
1. Grain Size The size of the sand grains plays a significant role in determining the density. Finer grains can pack more tightly than coarser grains, resulting in a higher density.
2. Moisture Content The amount of moisture present in the sand can affect its density. Wet sand typically has a higher mass due to the inclusion of water, impacting its overall performance during the casting process.
3. Additives and Binders The type and amount of binders and additives used in the sand mixture can also alter its density. These materials may increase the mass and stability of the sand, influencing the final casting characteristics.
4. Compaction The degree of compaction during the molding process directly affects density. Well-compacted sand will exhibit a higher density compared to loosely packed sand, leading to improved mold strength.
Implications for Casting Processes
The density of foundry sand has several direct implications for metal casting processes. Casting defects, such as shrinkage and gas porosity, can often be traced back to issues with sand density. A uniform and appropriately dense sand mixture contributes to fewer defects and better surface finish, ultimately reducing the need for additional machining and refining.
Additionally, understanding the density characteristics allows foundries to optimize their materials and processes. For instance, adjusting the sand composition according to the specific needs of different metals can enhance the quality of castings. More importantly, controlling sand density can lead to significant savings in material costs and improved production efficiency.
Conclusion
In summary, the density of foundry sand is a vital factor in the metal casting process. By carefully considering the factors that influence this property, foundries can optimize their casting operations, minimize defects, and improve the quality of the final products. As the industry continues to evolve, understanding the role of sand density will remain crucial for achieving greater efficiency and excellence in metal casting.
Post time:დეკ . 21, 2024 06:35
Next:Understanding the Process of Sand Casting and Its Applications in Manufacturing